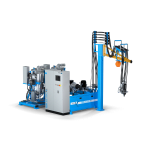
With the introduction of the Topline MK2 in the latter half of 2023, Hennecke will complete the "Next-Generation" series of its high-pressure metering machines. Following the introduction of the Ecoplus MK2 in the previous year and the new Highline MK2 at the beginning of the year, the top model Topline MK2 is the crowning glory of Hennecke's Next-Generation series. Alongside powerful basic equipment, it offers maximum flexibility and adapts to even the most complex process requirements thanks to numerous optional modules.
First choice for demanding tasks
The Topline MK2 covers all conceivable PU applications. This is the case too when it comes to highly demanding raw material systems typically requiring the most exact temperature control possible. It is also the first choice for highly automated applications such as refrigerated furniture production, seat foams or roof modules for automotive production. It is used as a stand-alone solution or in all conceivable system configurations where the highest quality, the greatest possible production and process stability as well as automation and scalability are required. "It's not without reason that the Topline MK2 is also the basis and heart of a wide variety of large-scale production systems - these often including several metering machines at the same time," explains Patrick Brüninghaus, Director Product Management at Hennecke.
Comprehensive premium equipment
For the design of the new generation of high-pressure metering machines, Hennecke analyzed and summarized the range of applications among its customers. Thus, the new Topline MK2 already covers more than 80 percent of all common applications in its basic configuration. Despite the extensive equipment features in this standard version of the premium model, customers benefit from a significantly shorter delivery time and high cost efficiency. "To be able to actually realize almost all feasible configurations in terms of production, we've put an emphasis on customization in the Topline MK2" reports Jens Winiarz, Senior Director Sales Metering & Composites. Thanks to the multi-platform design, there are no limits to the options - meaning a wide variety of applications can be realized. Maximum flexibility in adapting to specific requirements makes the Topline MK2 the first choice for individual and unusual customer requirements - for highly customized processes and special applications.
The machine processes almost all PUR raw materials and can also be adjusted to special features such as higher or lower raw material temperatures as well as special raw material systems - such as those with high viscosity. To this end, the Topline MK2 features the TS5evo temperature control unit as standard: this ensures powerful and constant temperature control - even under the most difficult processing conditions. What is more, the top model of the series can be equipped with up to ten mixheads. All Hennecke mixheads are available for this purpose: from the MT 3 for low output rates and the smallest part weights to the MT 36-2 for extremely high output rates, multi-component mixheads such as the MT-A 22-4, the MN series for spray applications and the new MT 12-3 CC mixhead for fast color changes.
Highest flexibility for all special requirements
Thanks to its modular system, the "High Performance" machine can be upgraded with numerous options. The multi-platform design means larger tanks with a volume of up to 1,000 liters are available for large-scale production - as are 60-liter tanks for smaller components or quantities. The Topline MK2 is pretty well prepared for all Hennecke peripherals that utilize the complete spectrum of modern raw material systems - thereby enabling an extremely diverse range of properties in the finished component. These typically include the Pentamat for metering flammable blowing agents such as pentane, the Lambdamat for non - flammable blowing agents, the Carbomat for CO2 loading of the polyol component, the Aeromat for gas loading of the polyol component or the Vacumat for efficient degassing of the raw materials for the production of high-quality compact components without air pockets. Future-proofing is guaranteed, because future peripheral equipment will also be perfectly matched to the top model from Hennecke.
The new Topline MK2 also offers the greatest possible flexibility in terms of the boom: instead of the 3-meter standard boom, other booms with a longer reach or automated mixhead handling through the use of robotics are also available. Especially for highly automated productions, the Topline MK2 offers optional motorized edge filters and thus ensures significantly less maintenance effort. Another highlight is the optional flow measurement by means of a mass flow meter. "This automatically measures the density of the raw material without the need for manual input. This is ideal for laboratory applications or in productions with frequent raw material changes," explains Patrick Brüninghaus.
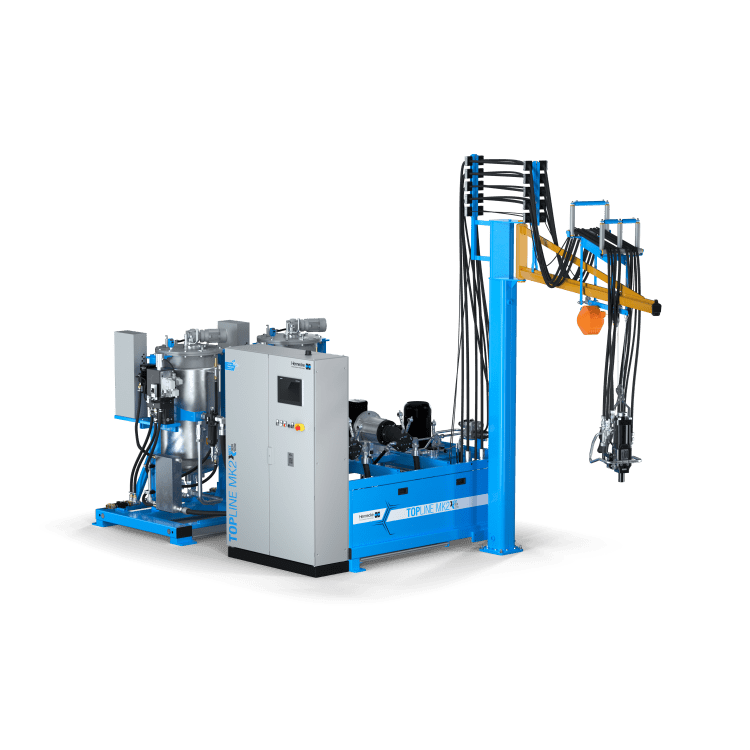
Excellent energy and resource efficiency
The careful use of resources has always been anchored in Hennecke's thinking and actions - and with the "Next Generation" line-up it is moving further into the foreground. This is why the Topline MK2 also benefits from Hennecke's "Blue Intelligence" technology - the latter comprising a whole package of measures for mechanical, hydraulic and thermal efficiency. This includes optimized components to reduce pressure losses, automatically determined pump lead times, intelligent standby timers, efficient pumps and much more. "Depending on the production scenario, energy savings of up to 50 percent are already possible in the standard configuration of the Topline MK2," adds Jens Winiarz. Top quality thanks to HX pump and latest nozzle generation As befits a state-of-the-art model, the Topline MK2 also offers all the other innovations that have already proven their worth in the HIghline MK2. These include the latest nozzle generation from Hennecke, which stands for high metering accuracy, best mixing quality and first-class efficiency. Besides the HP series, the innovative HX pump generation is also used in the Topline MK2: the world's first axial piston pump developed exclusively for PU applications. Hennecke's own development is based on decades of experience in polyurethane processing and offers noticeable added value. It is characterized by a significantly optimized design of the pump housing - enabling maximum bearing flushing thanks to a newly developed bearing seat. This ensures efficient heat dissipation and at the same time prevents the reactive media from heating up. That provides clear advantages in terms of resistance, especially to the chemical attack potential of polyol materials. The pump also features significantly improved suction behavior. This is a real advantage when using highly viscous polyols.
New control and IoT connection
Especially in combination with the diverse options offered by the new Foamatic software and the integrated "Blue Intelligence" technology, the HX enables high savings potentials and scores in terms of sustainability aspects. The Foamatic control software has also been completely redeveloped for the "Next Generation" series. Operation is via a high- resolution 12-inch HMI with a modern and intuitive visualization. Furthermore, other smart devices such as tablets or mobile phones can be connected thanks to optional WLAN connectivity. A major focus of the new Foamatic is on the topic of energy and raw material efficiency. For example, the software offers numerous setting options to optimally adjust standby or lead times or temperatures and thus achieve noticeable savings effects. In addition, the Topline MK2 enables connection to the Internet of Things with the standard Foamatic-IoT equipment feature. The acquisition and storage of extensive process data offers Hennecke customers unimagined possibilities for evaluation, early detection and prevention of problems, as well as predictive machine maintenance. For example, specific operating states of the machines can be sent to the mobile phone via push message. Hennecke is once again a true pioneer in this area of application.
Since the software for all high-pressure metering machines of the "Next Generation" is from a single source and uniform across all machines, switching between the individual series is very convenient for the user. "This is a great advantage for growing productions and companies with several locations or in different countries. User training can be reduced to a minimum in such a scenario," says Oliver Girnstein, Director Service BU Germany.
"Next Generation" - an investment in the future
The design and construction of theNext Generation Metering Machines was one of the company's largest development projects in the past 75 years. "In the process, the product portfolio in the area of high-pressure metering machines was not only optimized and improved, but also completely revised and rethought in a long development process under the aspects of energy efficiency, sustainability, productivity and digitalization," reports Patrick Brüninghaus. The entire development of the Next Generation portfolio is based on the "Hennecke Production System" (HPS). The focus of this lean production system involves interlinking individual production areas to enable synchronized, waste-free production oriented to the customer cycle. The extremely short delivery times in the standard range of next-generation machines would be inconceivable without the HPS
"Hennecke Production System" cushions cost increases
A central goal of the revision was to offer preconfigured solutions that already cover a large part of the market requirements in the standard version. These new standards offer customers decisive advantages: they speed up production, shorten delivery times, reduce costs and substantially simplify the entire process from machine selection to commissioning. This is also reflected in the price. "We're very proud that the Hennecke production system is so effective. Despite its numerous improvements, the Topline MK2 is thus able to stand up to the general price increases and absorb a large part of the increased costs," Patrick Brüninghaus is pleased to say. An important factor here is the use of common parts and part families across machines and series. This not only makes production significantly faster and more cost-effective - but also offers the user many advantages due to the better supply of spare parts and the use of uniform standards, especially if the user is already using other Hennecke systems