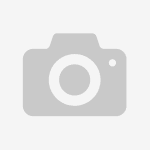
- Over the years, we`ve seen an increase in high speed solutions for conveying and packaging - said Mariusz Gradowski, senior area engineer for Unilever Polska. - This is tied in directly to the increased rate of changeover required for new products and packaging on the production line. Because of this, it is important that we embrace a high-speed conveying solution to replace the system currently in place.
The tea was being transported by a bucket conveyor over a distance of 15 meters. The conveyor was also on a vertical rise of 5.5 meters, reaching a capacity of three tons per hour. - The bucket conveyor was proving to be an inefficient solution - said Gradowski. - It would break down approximately once a month, which was resulting in nearly a full work day of downtime that effected the entire production line and mixing shop.
The bucket conveyor was also dropping roughly 100 kilograms of tea each shift. This represented two percent of the total product that was destroyed every day, or 5,250 Euros of raw materials each month.
Another issue was the dust being emitted from the open conveying system, creating a work environment that was not as healthy as it could be for employees. Unilever Polska decided to work with PIAB to find a solution that would increase productivity by reducing downtime and product loss, while also improving the air quality in the facility. The company installed two VCP1600 conveyors equipped with adapters and a de-dusting system.
- The PIAB solution is one that fully met our requirements - explained Gradowski. - It`s a fast, enclosed solution that was proven to be much more reliable than the bucket conveying system. Since the installation, we have nearly eliminated downtime that was causing a business loss of 8,400 Euros each month. Aside from eradicating machine breakdown, we also greatly reduced our maintenance costs.
Unilever Polska saw the biggest return-on-investment with the reduction of product loss - both in raw materials and end product. - Our overall savings has been measured at almost 165,000 Euros per year. This doesn`t take into account the end products that we are no longer losing - remarked Gradowski. - The results would then be over 730,000 Euros per year.