Let's move on to the company's current activities. What type of equipment does MAS offer?
As well as classic extrusion, melt filtration, and gas venting processes of various plastics, MAS extrusion technology also enables the finishing of these commodity plastics with multiple additives.
The re-compound line is one of our solutions for recycling and compounding in one step, even for materials that are difficult to degas. In addition, MAS twin-screw extruder offers the option to mix all recycling fractions - such as materials with the lowest bulk density, mill materials, or fibers with additives and filler materials – or to homogenize fluctuating input qualities excellently.
For more complex requests, we recommend the twin-compound lines, which create recycling compounds for exceptionally high-grade applications. The first conic, concurrent twin-screw extruder mixes all recycling fractions, such as materials with the lowest bulk density, mill materials, or fibers with additives and filling materials. Having run through the first twin-screw extruder, contaminants such as wooden parts, paper, non-melting unusable plastics, or rubber are removed with the CDF continual melt filter.
Afterward, the material is transported into another MAS twin-screw extruder, where more additives, filling, and reinforcing materials can be added. The large pour hole also allows the insertion of long and irregular fibers, such as natural, wood, or carbon fibers. In addition, the material is efficiently degassed inside the twin-screw extruder thanks to the large melt surface. The conical construction facilitates the pressurization of the consequent granulation process without requiring an additional melt pump. Material granulation is executed via strand granulation, water-cooled die-face granulation, or underwater granulation.
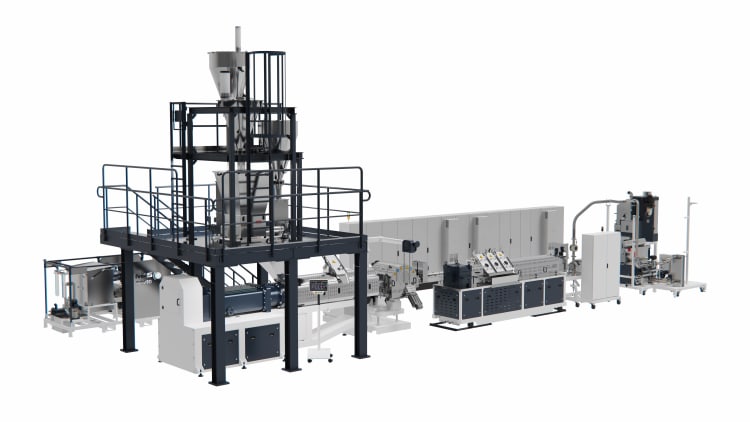
MAS PET- lines are also the ideal solution for processing PET in re-granulate and inline applications. The patented technology facilitates processing all PET recycling and new material fractions (such as bottle mill materials, mill materials from sheets, granulates, and additives) at low rotation speed and high screw filling degree for the shortest process length at low mass temperatures.
MAS technology also guarantees an excellent homogenization of fluctuating input material qualities and a large gas venting surface. As a result, the MAS solution leads to outstanding intrinsic viscosity, color, and AA levels at low energy consumption.
Depending on the application, this can enable optimization of subsequent condensation polymerization steps, reduction of pre-drying new materials and industrial waste, and achieving FDA / ESFA certifications in combination with pre-drying and a high-performance vacuum gas venting system without subsequent condensation polymerization step.
So a customer can build a complete process line with your help?
The significant benefit of MAS is that we offer not just machines but complete service as well. The service starts as early as the decision to acquire MAS equipment. Our experienced, competent experts accompany the customer from the place of the order.
The experienced and qualified project management team directs the successful realization of the project idea while always considering quality specifications and deadlines. Customers' wishes and potentially changing requirements throughout the project are flexibly checked for feasibility, incorporated, and implemented across the span of the project.
Our project managers are the central communication intermediary between our customers and specialist departments, taking care of the project from order placement to final acceptance.