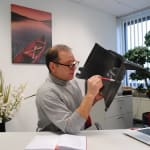
During weaker economic periods investment, given sound judgment, is indispensible in order to reestablish competitiveness - to get orders through the door. Any mould maker active in the plastics processing industry will need to think twice, and carefully, before investing in a multi-component machine for special sampling operations. An automotive parts supplier may face this very question at a time when orders are thin on the ground and requirements are on an upward trend. Why not upgrade an existing single-component IMM to a multi-component IMM instead? Hence, why not make enquiries at Windsor, Hanau, Germany, to establish possible options?
Over a number of years, Windsor has retrofitted many an IMM from single-component to multi-component units offering most attractive economic solutions. The PlugXPress series - PxP from 42 to PxP 1780 - are autonomous injection units, basically equivalent to an IMM without a clamping unit. Windsor’s great strengths include the company’s special adaptations for its customer: "We offer adaptations to fit the overall configuration – exactly“. The result: Individual systems with individual specifications where the PxP unit communicates via an interface with the IMM. There is no need for the customer to make any modifications to his IMMs, he simply needs to connect the PxP operating with a three-zone screw from 16 to 105 mm, a B&R control and a 15“ touch screen. The PlugXPress supplementary unit for multi-component injection moulding can be connected to any machine. “One of our customers produces toothbrushes applying this solution - in three plastics materials and in four different colours." Rising multi-component demand and the success of the PxP are demonstrated by the number of sold units during 2017 has more than doubled compared with the previous year. “Our strengths include the individual adaptations available; our high flexibility sets us apart from our competitors. When standard solutions no longer fit the bill PXP comes to the rescue." As soon as the PxP unit has completed an order on one IMM it can - as soon as required - be plugged onto another IMM as a mobile unit.
The PlugXPress series takes its queue from the ‘plug and play‘ concept; the units are ready to be easily connected to the IMM. As an independent plasticizing unit the PXP communicates with the ma-chine via a standard interface: “All processes can be handled straightforwardly - simplifying the tasks at the IMM immensely“, emphasizes Andreas Janisch, product manager at Windsor. The beauty of the easy application is that the PxP series is top of the class - state-of-the-art. According to Janisch a technical upgrade is in the pipeline enabling B&R control to function via Open Protocol. The injection units are not simplified, but a mobile moulding machine without a clamping system that fits any IMM - of any given type or origin – thus injects a second and/or subsequent component/s into the mould. "PxP is no scaled down variation but a fully functional unit“, explains Janisch. Highly wear-resistant materials for screws are standard. Virtually all prevalent thermoplastics as well as bespoke blends are processed, including polyamides containing fibre glass and engineering plastics. “We offer a standard three-zone screw and also special adaptations. Overall, we offer nine basic PxP units equipped with three screws each", continues Janisch.
How does injection moulding take place at the PxP? "First of all, we require a substrate, the first shot of the IMM - in the standard process for the basic part - followed by the other components via the PxP unit“, elaborates Janisch. The machine signals the moment the substrate is ready. This indicates the go-ahead for the first of “n“ PxPs." During the entire process, the products are logged most meticulously: The PxP unit encompasses storage for 1000 programmes. That number can be increased significantly with the use of a USB memory device. The advantage of PxP is its variability resulting in considerable cost savings for users. Janisch: "A typical starter machine would be a standard IMM. The user manufactures parts to the completion of the order. With a new order the possibility of issues with differing moulds may occur, in particular when dealing with multi-component part production. This would necessitate investing in a multi-component machine. Not an issue with PxP: At a third of the cost of a multi-component system users could enjoy upgrading their standard IMM.“ Subsequently, orders with different requirements can now be processed flexibly. Following the financial and economic crisis during 2008/2009 such significant cost savings derived from retrofitted PxPs benefitted a number of companies in the plastics industry.
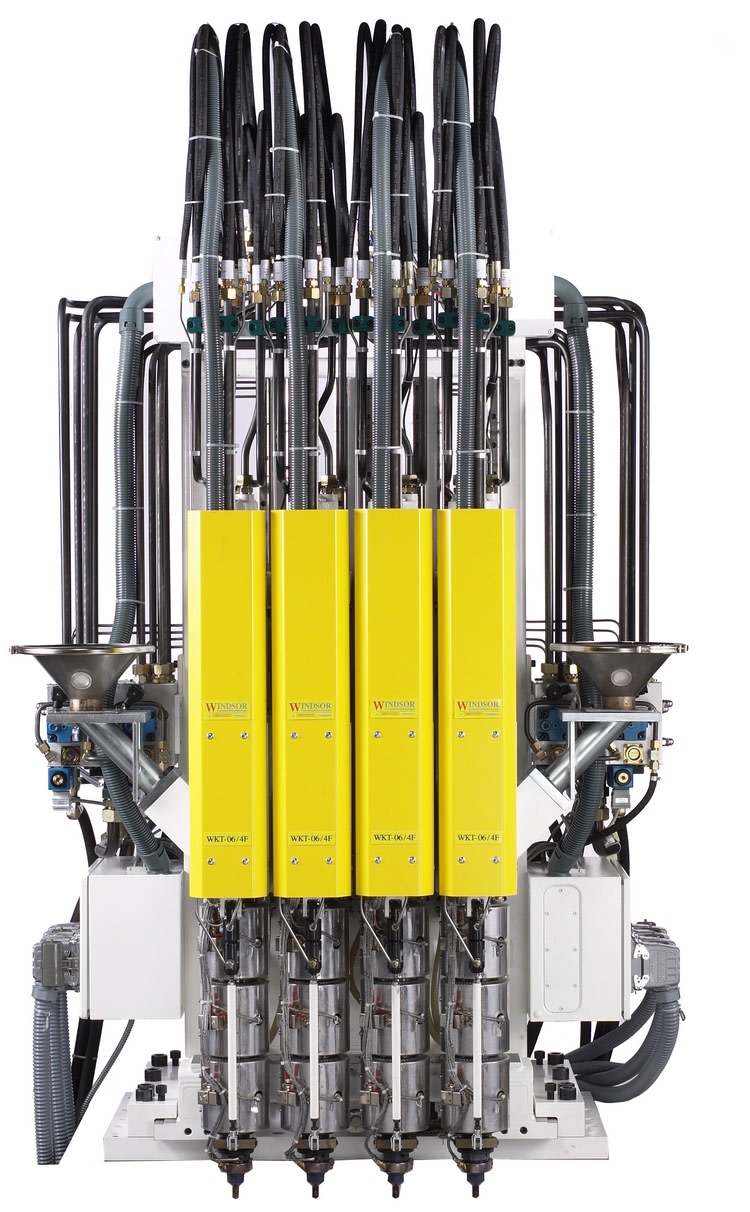