Vertical machines for assembly injection molding
Since electrical drives and an electronic control are the state of the art in closing and locking systems, virtually every one of the door closing and locking devices produced has a housing component with embedded electrical conductors. These are inserted into the mold of the overmolding machine either manually (for simple, mostly flat and therefore solid structures), or passed on by robots fully automatically and directly from a progressive cutting and stamping machine (in the case of three-dimensional multiple-track structures formed in several steps, which are difficult to handle manually). To provide ergonomically favorable conditions for this type of work, primarily injection molding machines with vertical injection units are used for this purpose. They make up about a quarter of the total machinery stock, ranging from simple 1-station clamping units for manual operation to 2-station rotary table machines in various sizes and automation levels. The majority comes from Wittmann and is partly combined with Wittmann robots and material handling technology.
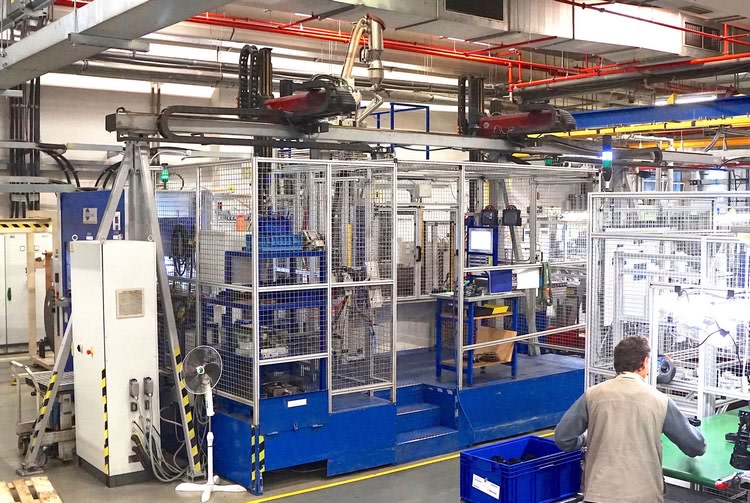
Appreciated by machine operators
Since Witte Automotive is the sole supplier for a number of lock modules, reliability is right at the top of its list of priorities for production equipment. Kamil Hušek, the company’s project leader for injection molding systems, comments: "Eight of our twelve Wittmann Battenfeld machines in operation have a vertical clamping unit. The oldest one is a Battenfeld VM-50 R and was built in 2002. It has been producing parts for more than 15 years in combination with a robot for insert feeding and parts removal without showing any decline in reliability or increase in maintenance expenses. In our newer machines, which we operate mainly as fully automatic production cells with two- to four-cavity molds, our workers on the production floor appreciate above all the excellent control system integration of robots and machines. For example in the event of a production interruption, resetting all robots to their defined starting positions is not necessary to resume automatic operation. In most cases, it is sufficient to simply press the cycle key. This is an advantage not to be underestimated, above all in shift work, when expert staff cannot always be called in for "trouble-shooting" immediately."