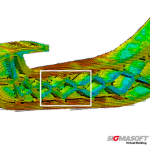
The mechanical properties as well as the shrinkage and warpage behavior of fiber-reinforced parts are strongly depending on its fiber orientation. If the lightweight construction properties of these plastics shall be used effectively, the fiber orientation needs to be considered from the start during the part and process design. However, cost pressure should always be kept in mind in addition to the technical requirements.
Sigmasoft Virtual Molding supports all decisions throughout the project via its virtual DoE (Design of Experiments). This DoE not only validates a specific design, but also compares it to other designs at the same time. Hereby, the user can be sure of having found a solution which is not only working but fulfills the general requirements at the best possible rate.
To optimally utilize the Sigmasoft DoE for making project decisions, the user clearly defines all requirements and transforms them into a shape which is comprehensible for the software. Afterwards, the software guides him through the process set-up and the user defines multiple designs for comparison, needing just a few clicks.
For an automotive application, Sigma Engineering optimizes a part regarding mechanical properties and shrinkage by illustrating the influence of various parameters and comparing the solutions with each other via Sigmasoft DoE. In this case, the glass fiber content of the material and possible injection point positions are varied. Additionally, further criteria, as filling pressure and maximum flow distance, are included to ensure a robust and economic process. By weighting these criteria individually and adjusting their limits the ideal solution is found: a mechanically and dimensionally stable part which can be produced in a robust process.
Sigmasoft Virtual Molding provides a sound basis which outlines all requirements relevant for important project decisions, enabling the user to decide fast, economically and without wasting material. Therefore, he can be sure to have found not just one possible solution but the best solution to meet the general requirements. With the help of Sigmasoft Virtual Molding, user make efficient, transparent and comprehensible project decisions.
Source: Sigmasoft