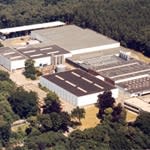
Thermoplastic compounding requires a careful balancing act as improving one property can unintentionally have negative consequences for another property, leading to compromises in the final compound because it was not possible to achieve desired performance for all properties simultaneously.
This is especially common in situations where it is necessary to have both a good balance of mechanical properties as well as halogen-free flame retardance (FR), because modification techniques that increase FR properties tend to reduce mechanicals and service life.
However, for at least one thermoplastic resin family, this seems no longer to be the case, thanks to a consortium of Dutch companies – including a thermoplastics compounder, colorant house, molder, and OEM– that have joined together to develop a new family of colored and flame-retarded long-fiber thermoplastic (LFT)-polypropylene (PP) compounds and masterbatches whose mechanical properties actually are better than those of the non-FR base resin.
The technology required to develop the new FR LFT-PP grades arose from the needs of one member of the consortium – TULiPPS Solar B.V. (Eindhoven, The Netherlands), a startup company working on a new composite-based solar photovoltaic (PV) module system for flat roofs – to find a flame-retarded version of the LFT-PP materials targeted for the system’s structural components.
New regulations are anticipated in many geographies requiring all polymeric materials used on roofs to be flame retarded. Since the composites used in TULiPPS’ module system have been formulated to offer an extremely demanding target service life of 25 years or longer, company founder and managing director, Paul Stassen wanted to ensure the units would comply not only with current regulations but also with future requirements where possible.
That presented an interesting challenge, since the composite module system needed both to be flame retardant as well as lightweight and thin, and therefore required high stiffness and strength plus excellent long-term durability – properties that can be affected by the non-halogenated additives package.
Fortunately, Stassen has a strong background in polymer additives and compounding himself, plus a network of industry-leading contacts developed during his many years working on LFT-PP compounding for the automotive-composites industry. To solve his formulation challenges, he turned to companies whose expertise could help meet the extremely challenging performance he sought for his solar PV composite support structure.
“What we are trying to make LFT-PP polymers do for the TULiPP’s module is a breakthrough that has never been done before – not even in the demanding automotive industry where these materials got their start,” explains Stassen.
“Meeting any one of these criteria would have been challenging enough, but meeting all of them at once – high but balanced mechanicals, high flame retardancy without use of brominated flame retardants or antimony, good processing, good aesthetics, and service life that is two-and-a-half-times longer than automotive specifications – really provided us with major challenges as well as opportunities. Balancing stiffness and toughness with FR was particularly difficult, because everything you do to improve halogen-free flame retardancy usually has a negative effect on mechanicals, processing, and service life.”
Stassen looked to his previous automotive-composites contacts for a creative compounder with a lot of formulation experience, particularly in the area of flame retardancy. He chose to partner with RESIN (Products & Technology) B.V. (Enschede) to find the right recipe to meet his project’s demanding performance specifications.