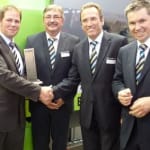
Engel identified this trend at an early stage and paved the way for hydraulic machines to a sustainable future with the servohydraulic Engel ecodrive. At Fakuma, the injection moulding machine manufacturer celebrated the delivery of its 1000th machine with ecodrive. Volkswagen in Braunschweig, Germany, will be using this machine to produce dashboards for the Golf, Golf Plus and Tiguan models.
“Within the Volkswagen Group, energy efficiency isn't just an important consideration for our products, but for the entire process chain", emphasises Marco Heinemann, who is responsible for machine planning at Volkswagen Braunschweig's plastics technology unit. "Our growth strategy means that we need to deploy existing resources in a more efficient way." This made energy efficiency an important decision making criterion for the latest investment in the automobile group's injection moulding machine farm. "We didn't expect to be operating the millennium machine here in Braunschweig", says Heinemann, who was delighted to accept the award at the Engel trade fair booth at Fakuma in Friedrichshafen.
Depending on the application and type of machine, hydraulic injection moulding machines fitted with Engel ecodrive servohydraulics realise energy savings of up to 70 percent compared to legacy hydraulic machines, thereby achieving consumption levels on a par with those of fully electric machines. This is made possible by reducing the loss energy during the machine's idle phases, a factor that accounts for a significant part of the energy consumption of a hydraulic machine without ecodrive. Drive standstill when operations stop is the key.
Where ecodrive is deployed, the pump is idle during cooling phases, for example, and thus no energy is consumed. On top of this, the oil cooling overhead is lower because, normally, only part of the supplied electrical energy is converted into kinetic energy, with the remainder transferred to the hydraulic oil in the form of heat. Engel ecodrive reduces energy losses to such a high extent that – with the exception of high performance applications – only minimal heating of the hydraulic oil occurs. Cooling water consumption at the oil cooler is reduced to a minimum, in many cases to zero.
"By reducing the loss energies compared to our older machines, we can now operate the new machines with their superior equipment in a cost-optimised way. This helps us to keep unit costs stable, and improve the division's competitiveness although energy costs have risen", says Heinemann. "One positive side-effect is the machines' quiet action."
By now, one in two hydraulic injection moulding machines from the Austrian Engel works is equipped with Engel ecodrive. This makes Engel the undisputed market leader in the hydraulic injection moulding machine sector with energy-saving options. Thanks to the successful market launch of Engel ecodrive, Engel has substantially increased its turnover in the 101 to 400 tonne machine sector.