Separation process of ABS and PS
It is easy to separate ABS and PS from each other with the electrostatic separation technology. A double-stage separation process is used for this purpose!
In the first separation stage, a pure ABS fraction is firstly separated from an ABS-PP mixture that has been pre-concentrated by float-or-sink separation and then dried. This is achieved by selectively charging the materials in the plastics mixture in a special charging unit. ABS takes on a positive charge, the other plastics PS and PP a negative charge. The ABS is then separated from the product stream with a positively charged electrode as a clean fraction with purity in some cases of > 99 %.
The remaining fraction, consisting mainly of PS and some residual ABS and PP, is taken up in a second separation stage, in which it is also electrostatically charged. The PS is separated by the electrode system as a clean PS fraction of purity > 98.5%. A so-called mixed fraction is also obtained, consisting of PS and ABS, which is mixed in with input material. Filled PP is obtained as a further fraction, mixed with some PS. The PS and ABS fractions are largely free of PP after electrostatic separation - ideal prerequisites for production of clean high-grade compounds.
A separation line for plastics from electronics waste therefore consists of two hamos EKS separators working on electrostatic principles in the first stage. These two pieces of equipment work parallel to each other, separating together at a rate of approx. 1.500 kg/h. As the ABS proportion separated in the first stage accounts for approximately 50% of input material, only approx. 750 kg/h comes out of the second stage with its single hamos EKS separator. So approx 1,500 kg PS and ABS per hour can be separated with use of the hamos KRS line equipped with three electrostatic separators, whereby the PP20 fraction is separated off in its own separation process. Photo 2 shows a KRS installation.
All of the machines are of course linked together by bucket elevators, conveying screws, etc. Equipment for filling of separated fractions into large “Big Bags” is also equally standard, so that the entire hamos KRS separation line can work in 24-hours operation, seven days a week.
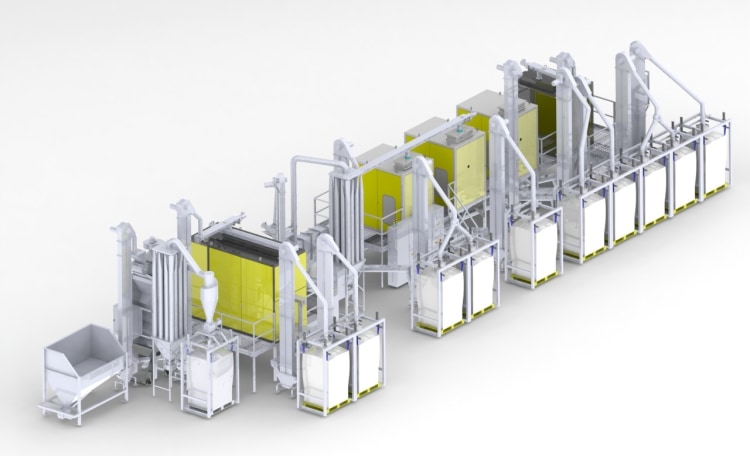
Photo 2. hamos KRS - separation line for plastics from electronics scrap
Separation of elastomers
Elastomers present a large problem in recycling of mixed plastics from electronic scrap. These elastomers arise in the form of rubber, silicone, elastomer foams, etc. They have the unpleasant property of not melting during extrusion of granulated material, leading to reduction in quality of the finished product, despite accounting for only a small proportion of the material. These elastomers therefore absolutely have to be removed from the granulated material.
ABS and PS mixtures charge mainly negatively in electrostatic separation. So they are mainly separated along with the equally negatively charged PS fraction. The ABS fraction is practically free of rubber after electrostatic separation!
The hamos RSS rubber separator has been developed by hamos in order to also free the PS fraction from rubber. The undesired elastomers can be almost entirely removed from highly concentrated waste fractions with this equipment. The energy consumption required here for separation is minimal. Photo 3 shows such an elastomer fraction.
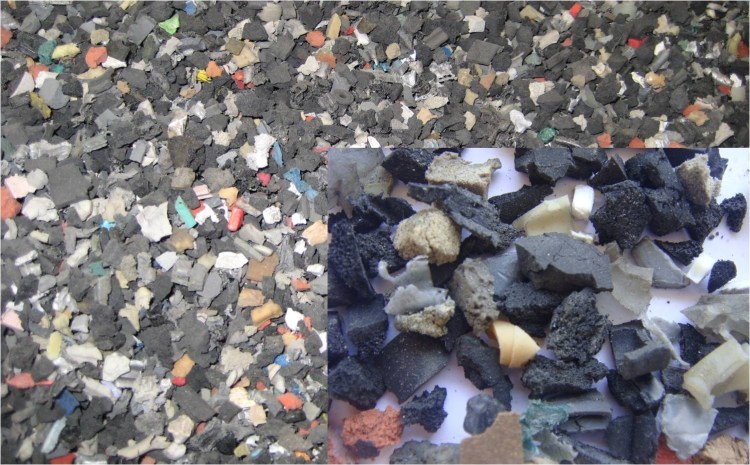
Photo 3. Elastomer fraction after separation by a hamos RSS line