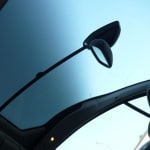
Due to fast cycle times, specific energy input and a clean appearance, ultrasonic welding is a good solution for joining plastic materials. Ultrasonics can be used to weld, form, embed and stake automotive parts. The applications range is wide: instrument-panels, interior door trim, roll-up sun shields and lighting, to name just a few.
In ultrasonic welding, supply voltage is converted to mechanical vibrations in ultrasonic frequencies through the piezoelectric effect. This vibration - at 20 kHz it amounts to as many as 20,000 movements per second - generates heat. The plastic material melts in the specifically aimed points and after solidification the parts form a positive material joint.
Headliner with cable channel
Customer project: Cable channel for extended wind shield
The project is a flat cable conductor (FPC = Flexible Printed Circuit), which supplies power to the electrical functions of console illumination, rain sensor and dimming function in the rearview mirror of a vehicle via the main cable harness in the headliner. The FPC is protected by a cable channel, which consists of an upper and a lower half shell. The cable channel is mandatory since the vehicle has an extended wind shield which results in a shorter headliner. Therefore, the FPC must be enclosed in a duct for visual reasons. The cable duct is fully visible and spans the A-area ranging from the headliner across the wind shield to the rearview mirror.
Complete product (FPC cable set in cable channel)
Process improvement: Welding instead of clipping
Initially, the half shells were to be mechanically clipped to one another in order to compensate for high temperature variations in the wind shield area. However, this did not provide sufficient rigidity of the product and resulted in undesirable noise from vibration and twisting due to friction between the two half shells. For these reasons, a product and process improvement was required for the cable channel: i.e. welding the two half shells by means of ultrasonic.
With the new ultrasonic solution the elaborate clipping hooks and eyes, which are very complicated from a tooling point of view, are no longer required; instead, the part was equipped with an energy director in the form of a stepped weld joint suitable for ultrasonics. This joint ensures optimum strength, invisible melt encapsulation and good part guidance in manufacturing. The new injection-molding tool provided a number of advantages in comparison to the originally planned tool due to the simpler part design.
Old version: complex lower half shell with clips
New solution: simpler lower half shell for ultrasonic welding
The delicate part surface is protected by film
The surfaces of both the lower and the upper half shells have a grained structure. This grained surface structure must be protected during the entire process. Particularly for the fixture of the lower half shell and at the contact areas between the upper half shell and the weld tools (Sonotrodes) suitable measures had to be taken without compromising the weld quality.
These requirements were catered for by a special sound-protected machine with two Sonotrodes and two actuators. Polished brass fixtures for the parts are guaranteed not to leave any marks on the lower half shell. Intactness of the upper half shell is ensured by a film indexer, which covers the part in a new piece of foil with every weld process. Thus, the Sonotrode does not come into direct contact with the part and the grained surface is kept intact while welding is performed.
Contact:
Marcin Tomczyk – Herrmann Ultraschalltechnik Gmbh & Co.KG
marcin.tomczyk@herrmannultraschall.com