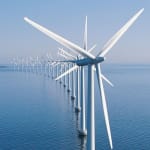
The UK Minister for the Environment had announced potential plans for another 29,000 wind turbines mainly offshore, and Siemens Energy had unveiled its latest 6MW turbine with rotor diameters of 120 and 154 metres.
In the same month the American Wind Energy Association (AWEA) announced that more than 1200MW were installed in the US in the third quarter of 2011, which is better than any quarter since 2008: the US wind energy market has been boosted by the federal Production Tax Credit.
The advances in the wind industry were reviewed by Frank Virenfeldt Neilsen, the Chief Technology Officer of LM Windpower, from the earliest windmills dating back to 4000BC. The first windmill to produce electricity was built by Poul La Cour in 1891.
The global wind energy market took off in the late 1970s as oil prices rose and many governments commissioned research, for example NASA and Tvind both had a 2MW project. LM Windpower has been involved in marine composites for 55 years and in wind blade manufacture for several decades.
The company is developing longer offshore blades of 73.5m in length weighing in at 26 tons, using experience from current installations, such as Alpha Ventus in Germany, Vattenfall in the UK, Thornton Bank in Belgium and Vindeby in Denmark.
The latter installation was set up in 1991 and used 33 blades: inspection over the next 20 years showed only minor leading edge erosion, which was restored. In 2000, 60 more blades were installed at Middelgrunden, Copenhagen and inspection 10 years later revealed only limited surface damage to gel coats, 9 blades with laminate cracks and 2 with lightning damage. Routine inspection and maintenance of blades can keep operating costs to a minimum and LM has extended its services beyond manufacture to support wind farm operators.
The limiting factor in blade scale up has been weight, and the solutions lie in new technology coming from studies of aerodynamics, load control and integrated design. Managing loads on blades can maximise the windswept area and increase energy production.
A prototype glass fibre-polyester blade takes around 9 months to develop and testing takes a further 6-12 months. LM has set up blade production in many areas of the world, with around 36% in China and 32% in Europe, and relies on suppliers to provide consistent, cost-effective supplies.
The cost breakdown of an onshore wind turbine shows that the drivetrain, hub and nacelle absorbs 25%; the tower, electrical systems and civil work each take up about 13%; and the rotor blades make up 11% of the total expense. Blade development can affect the load and cost of other components and this is being studied extensively by Christian Bak at Riso Danish Technical University (DTU) looking at drivers such as high aerodynamic efficiency (high power), blade-tower clearance, loads, transportation and moulding.
The virtual 5MW turbine of the EC Upwind project was used as the model in this investigation, which took into account the structural dynamics of the whole turbine. In the new slender blade design, the blade chord length was reduced by 16.7%, and the slender blades reduced the extreme loads on components by up to 24% and fatigue loads by up to16%.