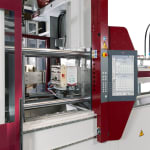
From September 26 to 28, 2023, Wittmann Battenfeld will present to visitors at the Interplas in Birmingham, hall 3A, booth No. CC10, state-of-the-art injection molding technology, automation and auxiliary equipment by way of fascinating applications.
As the leading plastics trade fair in Britain, the Interplas in Birmingham is also an important platform for the Wittmann Group for introducing its latest technologies to the UK market jointly with its local subsidiary. Among other things, Wittmann will demonstrate its expertise in the area of LSR processing and in processing alternative, bio-based materials.
A major focus of the machine presentation lies on the processing of special materials. On a SmartPower 120/350 LIM, an optical lens for motor vehicle headlamps, known as Smartlens, will be manufactured with a single-cavity mold supplied by the Austrian company Elmet, made of DOW Corning MS-5002, an injectable 2-component silicone, for Adaptive Driving Beam (ADB). This material was specially developed for highly transparent optical applications. The lens weighs just 10.38 grams. The mold comes with ventilation and overflow mechanisms for smooth production and maximum performance. What is more, Sigmasoft mold flow technology is used for mold analysis, which enables a preliminary simulation, to shorten the design and sampling phase. In preparation, the simulation software has been used in designing the mold. The dosing pump, which also comes from Elmet, is a Smartmix Top 7000 pro, the latest model. With a footprint of only 1,150 x 790 mm, it features the lowest space requirements of all dosing systems suitable for 200 liter barrels currently on the market. This also reduces the quantity of LSR present inside the system, which, in turn, increases process reliability and reduces the rinsing volume.
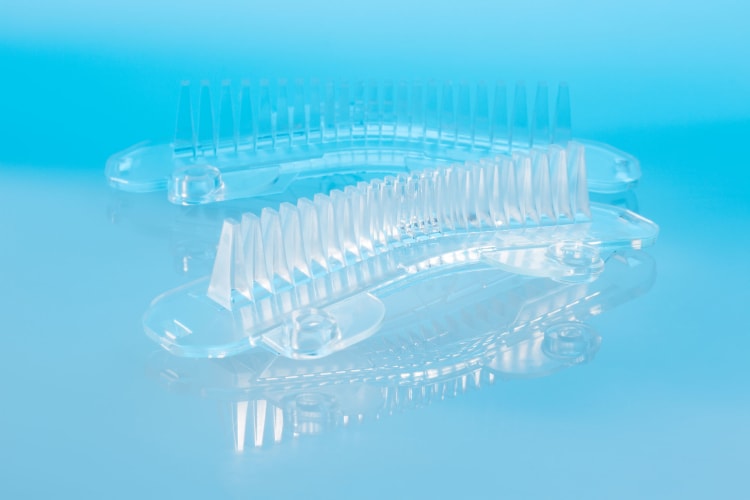
Smartlens – optical lens for motor vehicle headlamps
In the second application, a bio building block made of Fasal is manufactured on an EcoPower 110/350 with the new B8X control system, using an 8-cavity mold supplied by Bioblo, Austria. This raw material is a compound made by Fasal Wood GmbH, Austria, from wood flour and post-industrial polypropylene supplied by Borealis, Austria. The equipment is designed as an Insider cell, which has a W918 robot and an S-Max 3 screenless granulator from Wittmann, a conveyor belt and also the protective housing all integrated in the production system. The molded parts and the sprue are removed by the W918 robot, and the sprue is passed on directly to the granulator, where it is ground and then returned to the process. The finished parts are deposited on the integrated conveyor belt, transported to a flow wrapping machine and packaged.
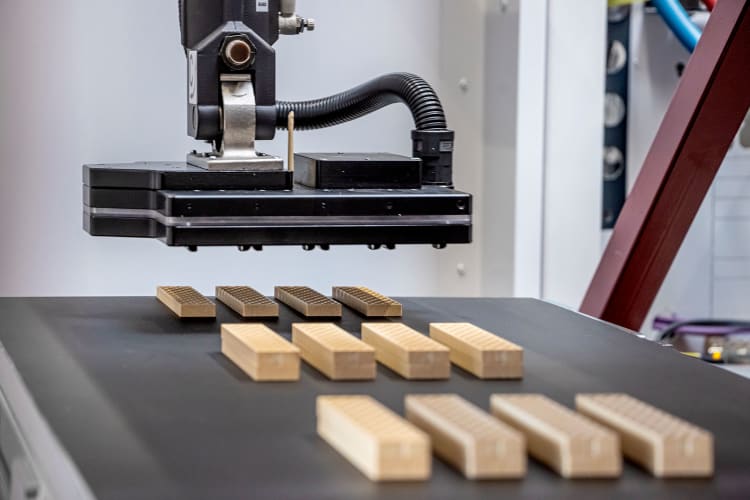
Depositing of Bioblo building blocks on conveyor belt
To ensure top quality for the parts, the software packages HiQ Metering for active closing of the check valve and HiQ Melt for measuring the MFI are used in addition to HiQ Flow. The resulting MFR (melt flow rate) is an indicator of the material’s flow attributes.