To supply the system with power, ultra-modern ecological salt battery technology on sodium-nickel basis from innovenergy will be used. The battery has a total capacity of over 45 kWh, more than sufficient for uninterrupted machine operation throughout an entire 8-hour trade fair day. In addition, electro-chemical capacitors, known as supercaps, will be used to complement the sodium-nickel storage units by balancing out short-term load peaks. Both the robot and the temperature controller will be powered directly via the EcoPower’s DC voltage interim circuit. The injection molding machine as well as the robot will also return any excess deceleration energy from the axes to the interim circuit.
EcoPower B8X - high dynamism with low energy consumption
At the Fakuma 2024, Wittmann Battenfeld will also demonstrate the high performance of its energy-efficient EcoPower B8X by producing darts tips made of POM, using a 32-cavity mold supplied by Hasco, Austria, on an EcoPower B8X 110/525. The mold is equipped with a pneumatic needle shut-off nozzle. The parts will be removed by a Wittmann robot and subsequently fed to a tubular bag system supplied by Ravizza Packaging, Italy, for packaging.
The machine’s high dynamism is achieved by optimizing the toggle system in the new EcoPower B8X together with a further acceleration of the injection units’ top speed. The encapsulated system filled with gear oil and a separate oil compartment for the drive unit and ball screw drive enable an increase in energy efficiency with a simultaneous reduction of wear. Added to this is the higher clock frequency of the machine’s Unilog B8X control system developed in-house to enhance both the machine’s precision and speed.
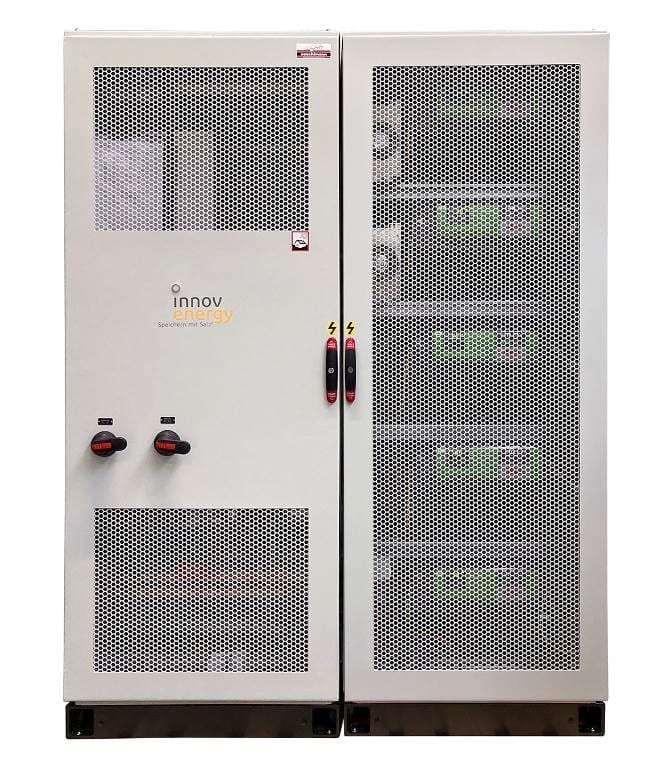
Efficient production of nano structures with new technology
Finally, the company will also present at the Fakuma its capacities in the field of micro injection molding. The MicroPower, designed for injection-molding micro and nano parts, comes with a two-step screw-and-piston injection aggregate able to inject thermally homogeneous melt with shot volumes ranging from 1.2 to 6 cm3. This makes it possible to manufacture parts of outstanding precision in a maximally stable production process with minimal cycle times.
At the Fakuma, Wittmann Battenfeld will demonstrate the production of demo tiles measuring 8.5 by 8.5 mm, on which a world map showing the locations of the Wittmann production sites is depicted, using a MicroPower 15/10. This is done with a 4-cavity mold with nano structures produced by 3D-printing and supplied by NanoVoxell, Austria. The main advantage of this new technology is the ability to produce minute structures within a short time and at low cost.
Silicone machine on a third-party booth
At the booth No. A6-6222 of Nexus Elastomer Dosing&Nexus Elastomer Molds (Austria), liquid silicone processing will be shown using an EcoPower B8X 110/350 LIM. With an 8-cavity series production mold, equipped with a Nexus “Timeshot” needle shut-off system, piston stoppers for disposable syringes will be produced from LSR and subsequently assembled fully automatically.
This application will also serve to demonstrate a central conveyor system for liquid silicone. Here, a Nexus Servomix X200 dosing system will handle the central LSR supply. A Servomix X1 booster unit will transport the liquid silicone from the main supply line to the injection molding machine.