Processing of alternative materials
Processing of alternative materials, especially renewable and recycled materials, presents a special challenge due to the viscosity fluctuations which such materials undergo during processing. Wittmann Battenfeld solves this type of problem by using HiQ application software, which is continuously evaluated and further improved in order to ensure highest quality standards in processing these materials, too.
At this year’s K fair, Wittmann Battenfeld will present two more applications where renewable materials are used. In both cases, the machines are equipped with the HiQ Flow software, which compensates viscosity fluctuations in the material.
One of these applications will be shown at the Wittmann Battenfeld booth C06 in hall 15. It is a bio-degradable ice-cream cup, manufactured with a 6-cavity mold supplied by Precupa, a high-precision mold-making specialist based in Germany. The parts are produced on an EcoPower 110/750 equipped with the new B8X control system. The material used is BAOPAP from HopeTree, Germany, consisting of water, vegetable oils and fats, starch, vegetable thickening and swelling agents and natural fibers, and is entirely free of chemical substances. It is disposable via the organic household waste can, with the material being decomposed completely and without residues within 50 days at the most. Its attributes recommend it as an ideal substitute for cardboard. This material can be fed into the injection molding process directly without pre-drying. Downstream finishing is also dispensed with. The parts are removed and deposited on a conveyor belt by a W918 robot from Wittmann.
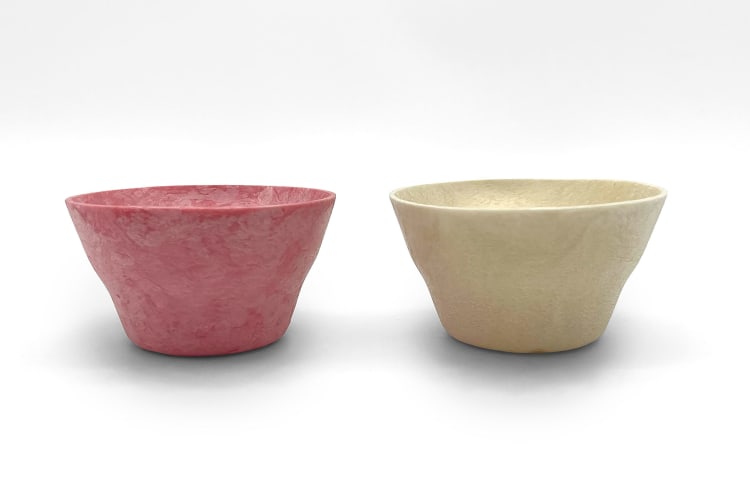
The second application in which a renewable material is used can be found at the VDMA Circular Economy Forum, outdoor area, booth CE10. In this application, a bio building block made of Fasal is manufactured on an EcoPower 110/350 with the new B8X control system, using an 8-cavity mold supplied by Bioblo, Austria. This raw material is a compound made by Fasal Wood GmbH, Austria, from wood flour and post-industrial polypropylene supplied by Borealis, Austria. The equipment is designed as an Insider cell, which has a W918 robot and an S-Max 3 screenless granulator from Wittmann, a conveyor belt and also the protective housing all integrated in the production system. The molded parts and the sprue are removed by the W918 robot, and the sprue is passed on directly to the granulator, where it is ground and then returned to the process. The finished parts are deposited on the integrated conveyor belt, transported to a flow wrapping machine and packaged. The tubular packaging bags are made of the BornewablesTM FB4370 material from Borealis.
To ensure top quality for the parts, the software packages HiQ Metering for active closing of the check valve and HiQ Melt for measuring the MFI are used in addition to HiQ Flow. The resulting MFR (melt flow rate) is an indicator of the material’s flow attributes.
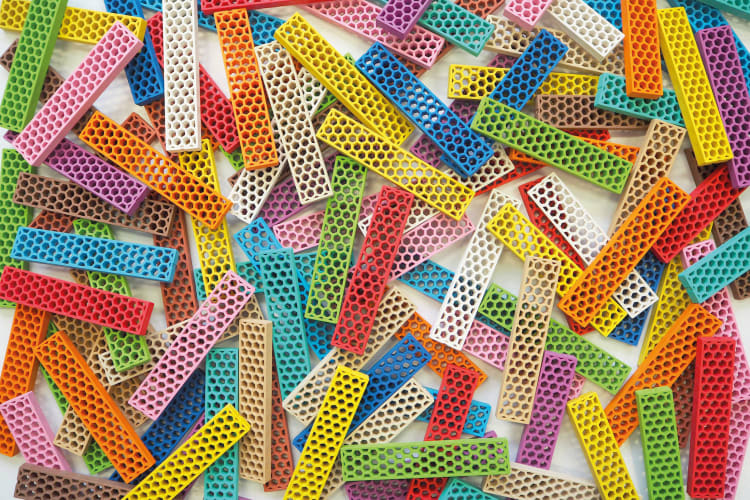
Injection-compression molding for thinner wall thicknesses
In injection-compression molding (ICM), the melt is injected into a not yet completely closed mold. Final forming of the part takes place following complete closing of the mold by displacement of the melt into the cavity. This enables the mold to be filled under lower pressure, which in turn leads to a reduction of warpage inside the part. Injection-compression molding allows processing of an extended range of materials with particularly high efficiency in material and energy input. Moreover, it offers innovative approaches to solutions where conventional processes have reached their limits. This process enables the production of extremely thin, precisely reproducible wall thicknesses and accurate reproduction of surface structures.
Wittmann Battenfeld will demonstrate this technology on a high-speed EcoPower Xpress 160/1100+. With a 4-cavity mold supplied by Glaroform, Switzerland, a 230 ml cup made of polypropylene from SABIC, the Netherlands, with a wall thickness of 0.28 mm will be produced within a short cycle time. Thanks to the highly dynamic drive technology of the high-speed EcoPower Xpress, especially the short injection times required for the ICM process can be realized. The machine is equipped with a 4-fold IML system supplied by BECK Automation, Switzerland. This system stands out by its high speed and compact design. One of its special functions is automatic positioning of all four labels. Regardless of its position inside the magazine, every label is invariably placed into exactly the same position on the IML core. This reduces both reject rates and operating effort, since manual adjustment of the label magazines is no longer necessary. Quality inspection of the cups decorated with IML labels supplied by Verstraete, Belgium, will be carried out by a vision system with 10 cameras integrated in the production line, which comes from Intarvis, Germany.