“35 minutes is our target for mold changes”, explains Israel Almeida Furtado, Tech-nical Manager at the Joinville facility. “This is what we need on average for cost-efficient production.” Without the special features of the MacroPower, the bulky molds could not be set up within such a short time.
An additional gain in efficiency is achieved by the fact that extremely large molds fit on comparatively small machines. In this way, the machine can be chosen on the basis of the clamping force required for the injection molding process rather than based on mold dimensions. “The door-opener for Wittmann at Krona was a machine request for a special fitting mold”, Marcos Cardenal from Wittmann Battenfeld do Brasil remembers. “We finally delivered a machine two clamping force s smaller than the one originally requested. This was perfectly adequate for the mold and led to an increase in overall efficiency.” After all, smaller machines not only reduce the investment costs. They also come with lower energy consumption and a smaller footprint.
Perfect setup for PVC
Almost all products leaving Krona Group are made of PVC. In total, all units process 10.000 tons of PVC per month, of which just under 2000 tons go into injection mold-ing.
PVC melts have a high viscosity and are sensitive to shear stress and heat. The consequence is a very small processing window, since the plasticizing time must also be long enough to achieve good surface quality. Although the products are invisible when installed, their surface quality still plays a major part. Pipe segments and fittings are also sold in do-it-yourself markets, and consumers buy according to optical impression. “The outward appearance of parts must reflect their quality”, says Gonçalves. Professional tradespeople, on the other hand, judge the products’ quality by their durability. Piping components must keep intact and function for a long time. Once installed, they cannot so easily be dismantled and replaced.
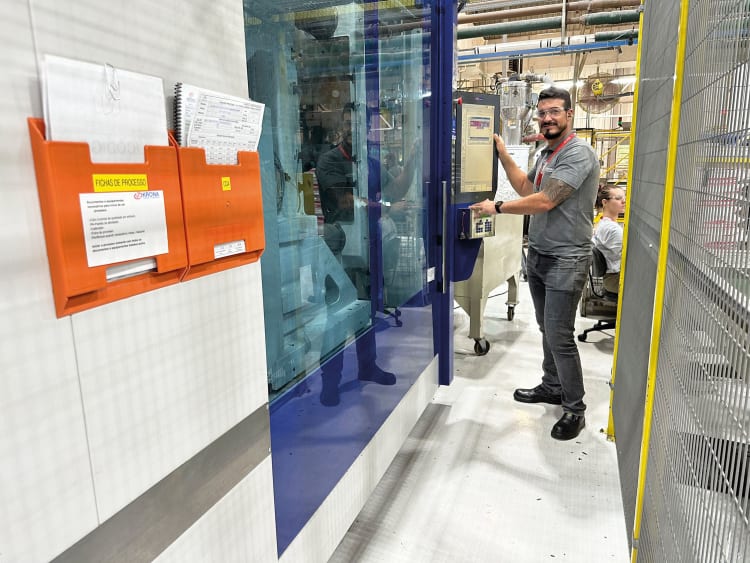
To ensure a consistently high quality standard for the parts, all Wittmann injection molding machines at Krona are equipped with plasticizing units optimized for PVC processing. “The Wittmann PVC package was originally a customized special de-velopment for Krona”, says Saltori. The geometry and surface attributes of the screws have been adapted to the specific requirements of the material, and the drive torques are higher than normal. In addition, Wittmann has developed a new special screw tip. It reduces the shear load and by its flow-optimized geometry makes complete material discharge possible.
The PVC package is now an integral part of the options catalog for all Wittmann injection molding machines. Nevertheless, the machines for Krona have not come off the peg. “PVC is not the same everywhere”, Furtado points out. “The plasticizing units have also been adapted to the types of PVC available here in Brazil.