The location also benefited from the global production network of the BSH Group. The same washing machine models are produced in other countries, too, and cer-tain injection-molded parts were already manufactured in-house there for earlier generations of appliances. “We cooperated very closely with our colleagues from other countries, and were thus able to learn a lot for our new injection molding shop”, Pirek reports. ‘Network of Experts’ is the designation of this concept at BSH, which functions for all technologies being used within the Group. All locations are part of a digital network. “Industrie 4.0 makes cooperation beyond the boundaries of individual locations very simple”, says Pirek.
Automation made to measure
The housing geometry of the new washing machine generation, however, present-ed all production sites with a new challenge. “We had to completely re-design our automation concept”, says Zabrzewski. Starting with the grippers and all the way to stacking the molded parts on pallets for transport to FIFO storage.
The W863 pro robots with a maximum load capacity of 75 kilograms perform several different functions. They insert the bearing bushes into the mold to be over-molded, demold the housing halves and stack these on the pallets according to a prepro-grammed storage pattern. To handle the pallets, Wittmann has developed a multi-level conveyor system. The pallet exchange is carried out fully automatically. The pallets are prepared for collection on the upper level of the conveyor while an empty pallet is moving up from the lower level.
Another special feature is the integration of the robot’s control system in the produc-tion cell. The robot program is downloaded via the injection molding machine’s control system, with an RFID code to ensure that the correct gripper has been attached.
“The success of this project is the result of extremely close cooperation between the process experts at BSH, the automation specialists at Wittmann in Germany and our local technical lab at Wittmann Battenfeld Polska”, says Zabrzewski. BSH benefits from the fact that the injection molding machines and the automation equipment have all come from a single source. “That was our target from the very beginning”, says Pirek. “We had only one central contact partner for the entire project and are convinced that this was why we were able to start up the system so quickly and smoothly.”
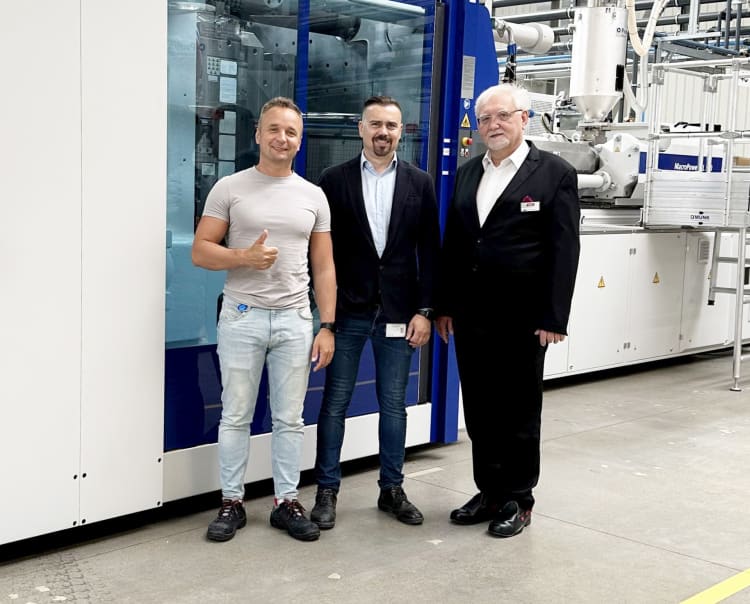
The availability of the machines is vital. They must be “ready for production” at any time, as Bogdan Zabrzewski emphas. For there is no production of goods to be kept in stock. If the injection molding production came to a halt, this would also immediately bring the assembly line to a standstill. So, reliability in service was another decisive argument in favor of choosing Wittmann as injection molding partner. In any case of trouble, the Wittmann service engineers are very quickly on site. Particularly critical spare parts are kept in stock.
“Within the walls of our plant, we have built up a completely new factory. Without Wittmann, we would not have been so successful in this project”, emphas Pirek, and praises above all the very open communication as an essential success factor. “Here, the right people are working together. People with a lot of knowledge and experience communicating openly with each other at any time. The plant in Łódź has now become the benchmark within our production network.”
A wonderful confirmation of this success story came in the form of a special award. Project Leader, Michał Zimowski and his team had submitted an entry for an internal BSH award contest. From a total of 50 projects submitted, the foundation of the injec-tion molding facility in Łódź was chosen as Project of the Year 2024.