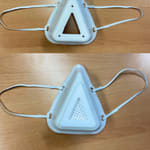
While high-quality thermoplastic elastomers (TPEs) from Kraiburg TPE are used in many everyday applications such as toothbrushes, razors, automotive components, and others, they have also become indispensable in numerous areas of systemic importance. The current corona pandemic is an increasing challenge for both healthcare and social systems in particular. Currently, our TPEs are used in medical applications such as valves, connections and tubes for ventilators, face masks, respirators, as well as simple buttons and elastic straps
Specialty Thermolast® M and Thermolast® K compounds are needed here. The Thermolast® M medical compounds in particular are characterized by a high degree of purity, which is guaranteed through a constant production process, permanently assigned production units and numerous quality assurance tests.
In the current situation, Kraiburg TPE has decided to increase its production capacities for these materials and to give top priority to their production. It goes without saying that the internal procedures for protecting staff members have been optimized and adjusted accordingly. Stocks of the relevant raw materials have been increased to ensure constantly smooth and stable production capacity. These procedures guarantee a rapid supply with our TPEs to meet the growing worldwide demand of a wide variety of medical applications.
For example, BaS Kunststoffverarbeitung GmbH from Eslarn is one of the German companies that have decided to use their production capacities in the fight against Covid-19. Instead of components for the automotive and electrical industry, the company is now producing reusable face masks/respirators for welfare and social-service institutions and medical offices. It was the company’s close collaboration with Kraiburg TPE in the project, among other things, that made this possible.
After BaS had designed a 3D model, Rietsch GmbH Werkzeug- und Formenbau produced the mold required to manufacture the masks. Thanks to forward-looking planning, Kraiburg TPE was able to promptly deliver the compounds needed to produce the masks, so that it took only a few days for the first sample to come off the conveyor belt. A total of 1,500 masks with breathing apparatus filters can now be produced daily.
The unique feature of this mask system is its modular design that combines a cleanable half-mask and an exchangeable filter. The plastic mask is easy to clean – in a dishwasher, for example – and can be reused with a new filter afterwards.
“Our TF5CGN material was selected for the BaS mask. The mask is very easy to clean and has a pleasantly soft surface that allows it to fit snugly onto the face,” says Matthias Schmidt, Sales Manager Medical at Kraiburg TPE. “This is one of many different face-mask applications that have recently been implemented using our TPEs. What we like most about this special project is the supportive collaboration there was between all of the companies involved. Thanks to the rapid implementation of the project, local and regional retirement homes, outpatient services, and medical offices are quickly receiving masks so they can work in a protected and safe way during the coronavirus crisis.”