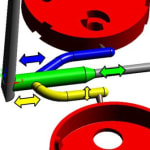
In einem Fallbeispiel sollte das Angusssystem eines Familienwerkzeugs optimiert werden, um eine balancierte Füllung der verschiedenen Bauteile zu erreichen. Diese unterscheiden sich deutlich in Volumen und Wandstärken. Im ursprünglich geplanten Angussdesign erfolgte die Füllung deshalb sehr ungleichmäßig und ein einzelnes Bauteil bestimmte die Produktivität des gesamten Prozesses.
Bestandteil der Autonomous Optimization ist die Möglichkeit, eine virtuelle DoE (Design of Experiments) durchzuführen. Diese kam auch für das Familienwerkzeug zum Einsatz, um das Design zu verbessern und eine gleichmäßigere Füllung aller Kavitäten zu erreichen. Zunächst erfolgte dazu die Bestimmung der zu variierenden, geometrischen Parameter (Bild 1). Als Freiheitsgrade wurden die Länge der Aufdickung des Hauptanguss, der Radius des im Bild unteren Anguss und die jeweiligen Startpunkte der seitlichen Angussarme, an denen sie vom Hauptanguss abzweigen, variiert. Zusätzlich wurden bereits die gewünschten Zielgrößen festgelegt. Diese sind geringe Differenzen in den Füllzeiten der einzelnen Kavitäten sowie ein niedriger Fülldruck.
In der Auswertung wird jede Variante durch eine Linie repräsentiert, die vertikalen Schieber zeigen die Freiheitsgrade und Zielgrößen auf (links). Über die Schieber grenzt der Anwender beides weiter ein und ermittelt so die beste Variante (rechts)
Nach der Berechnung aller Geometrievarianten in einer virtuellen DoE, werden diese mit Blick auf die Unterschiede in den Füllzeiten verglichen und bewertet. Die linke Seite zeigt zunächst alle gerechneten Varianten, die je von einer bunten Linie repräsentiert werden. Die einzelnen Spalten bilden die Freiheitsgrade und Zielgrößen und ihre jeweils möglichen Ausprägungen ab. Anschließend grenzt der Anwender über Schieber an den Spalten die Zielgrößen auf die gewünschten Werte ein und identifiziert so die beste Variante (Bild 2, rechts). Im vorliegenden Fallbeispiel sollte der Fülldruck geringer als 600 bar sein, bei einer gleichzeitigen maximalen Differenz von 0,1 s in den Füllzeiten der Kavitäten. Das ermittelte Angussdesign zeigt eine deutlich balanciertere Füllung der einzelnen Kavitäten (Bild 3). Diese Geometrie wird im Anschluss als Ausgangspunkt für detailliertere Optimierungen des Werkzeugs und der Prozesseinstellungen genutzt.
Das beste Design zeigt eine balancierte Füllung mit annähernd gleichen Füllzeiten in allen Kavitäten
Mit Hilfe der in Sigmasoft Autonomous Optimization enthaltenen virtuellen DoE lassen sich auch geometrische Änderungen mit geringem Aufwand überprüfen. Gleichzeitig wird ihr Einfluss auf definierte Ziele, wie z.B. die Differenzen in den Füllzeiten mehrerer Kavitäten oder den Fülldruck, bewertet. Auf diese Weise finden Anwender auch für Werkzeuge, die sehr unterschiedliche Bauteile kombinieren, sicher und schnell das optimale Angusskonzept, um ihre Anforderungen zu erfüllen.
Quelle: Sigma Engineering GmbH