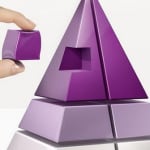
Whether in sports equipment, pressure lines in trucks, medical devices, or 3D printed high-tech parts, polyamide 12 elastomers from Evonik have over the last four decades repeatedly found their way into new high-end applications demanding a unique balance of material properties. The polymer designers of the specialty chemicals group have continually been developing the thermoplastic high-performance polymer and expanding the range of its possibilities.
PEBA: Master of versatility
Digitalization, automation, and Industry 4.0 are currently major talking points in business and the economy. In this cloud of buzzwords, 3D printing is often identified as the game changer in industrial production. Interest in the tool-free production of high-tech components has been growing for some years. The highly dynamic 3D-printing market has been developing promisingly and, with current growth rates in two digits, is now on a roll. Evonik has been active in additive manufacturing technologies for more than 20 years and is now a global leader in the development and production of customized polymer powders for various 3D-printing technologies. In a worldwide first, the specialty chemicals company has developed a flexible plastic material based on PEBA (polyether block amide), for use in 3D printing. The new high-performance powder has impressively high elasticity and strength and can be used in a variety of powder-based 3D-printing technologies.
''Flexible polymer materials significantly expand the options for additive manufacturing because they allow us to realize new, demanding applications in attractive markets,'' says Fabian Stoever, senior product manager for polymers at EOS, the global technology and quality leader for high-end solutions in the area of additive manufacturing from Germany. ''In addition, the variety of materials not only enables us to produce individual high-tech functional components, but also to develop much more sophisticated 3D concepts that make use of the entire material range.''
An innovative material for individual solutions
3D printed parts made from the new PEBA powder show a high degree of flexibility, excellent resistance to chemicals and outstanding durability over a wide temperature range from -40°C to 90°C. The powder is also ideally suited for the manufacture of functional 3D high-tech plastic parts - for prototypes as well as series products, and can be used in a variety of powder-based 3D-printing technologies such as selective laser sintering (SLS), high-speed sintering (HSS), and binder jetting - all of which are new manufacturing technologies discovered only a few years after the market launch of polyamide 12 (PA 12) elastomers.
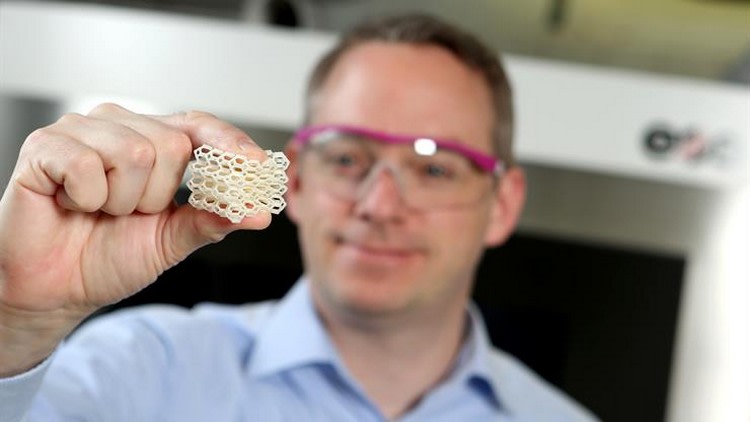
Evonik celebrates 40 years of PEBA
In 1979 Evonik launched on the market, from its largest global production site in Marl Chemical Park, a polyether block amide (PEBA) thermoplastic elastomer under the brand name Vestamid E. At the time, hardly anyone could have imagined that four decades later the material would be used in powder form for additive manufacturing. Then, as now, the high-performance polymer impressed by its excellent low-temperature impact strength, resistance to chemicals, high elasticity, and good resilience. It was easily processed, colored, and overmolded. Right from the beginning, the thermoplastic material offered a unique balance of properties allowing the realization of high-end applications with freedom of design.
Performance and design are essential attributes in the sports industry. The PA 12 elastomer molding compounds from Evonik were quickly recognized as the material of choice for, e.g., sports shoe soles, ski touring and ski mountaineering boots, and subsequently as decorative protective films for skis and snowboards.
Ski boots and mountaineering boots made of PEBA are, even today, light, waterproof, and wear-resistant, and retain good flexibility even in the cold. Due to its outstanding mechanical properties, the high-performance material can be used efficiently to optimize the wall thickness of the shoes, which in turn optimizes production costs.
Sports shoes also need to be tough, which means that the high-performance polymer must withstand the highest mechanical stresses, both static and dynamic. The shoes must convey an impression of lightness so as to give the sprinter wings, the long-jumper a tailwind, and the cross-country skier light legs. They must also withstand environmental effects. Extreme performance in sport is required at temperatures as low as -40°C as well as in extreme heat, and abrupt temperature changes also need to be taken into account here.
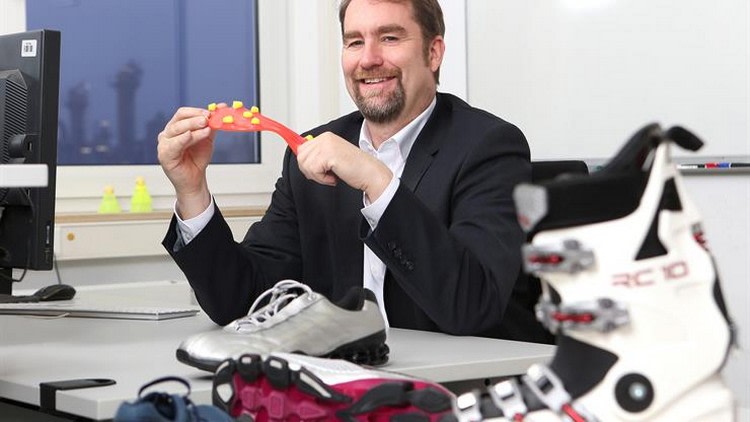