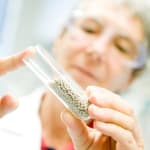
AIM3D, a manufacturer of multi-material 3D printers, has developed a new, more powerful 3D printer for the CEM (composite extrusion modelling) process. The new ExAM 510 boasts a larger build area, higher precision and faster build rates. The ExAM 510 printer is a multi-material printer for additive manufacturing that can print up to three different materials in parallel. The ExAM 510 printer is a performance-enhanced version of the previous ExAM 255, both of which will be part of the Rostock company’s product range in the future. The new model will be on show as a prototype at Formnext 2021. After a beta phase with pilot processors, the ExAM 510 is planned to be ready for series production in time for Formnext 2022, according to the manufacturer.
Setting new standards with the ExAM 510
As the latest addition to the Rostock company’s product line-up, the ExAM 510 printer is a further development of the smaller EXAM 255 model. The innovative multi-material printer can process up to three materials. This allows for two building materials and a support material. The extended build platform of 510 x 510 x 400 mm enables a multitude of applications. The build area can be heated up to 200ºC in order to reduce stresses in the component and to process high-performance materials. It also features a considerably increased build rate, depending on the material, of up to 250 cm³/h (when using a 0.4 mm nozzle).

Entry-level CEM 3D printer: EXAM 255
High precision and excellent component quality
The ExAM 510 concept enables significantly increased precision of printed components. The objective of developing the machine was to get even more out of the patented AIM3D extruder technology. This extruder class enables an output up to 10 times higher than standard filament extruders. The use of linear motors and a stable mineral cast bed makes extremely precise operation possible even at high speeds, thus fully exploiting the potential of the technology.
Key advantages of diverse materials and cost savings
The use of a wide range of materials is the particular appeal of the ExAM 510. AIM3D equips the machine with a heated process chamber specially designed for high-temperature plastics. This enables the processing of high-temperature plastics such as PEEK, PEI, PSU, PPS, with and without fibre filling. Corresponding experience with the extruders had already been gained with the ExAM 255. This means that a user can, for example, process PEEK, either unfilled or filled with fibre material, directly in pellet form in additive manufacturing. This results in an enormous cost advantage in terms of the raw materials. Recycling this material is also much easier and cheaper. According to the manufacturer, a material can be tested in 1 to 2 working days and established for production in 5 to 10 working days. The material PEEK, for example, demonstrates these high cost savings most clearly: if the price for PEEK filament is around €700/kg used on conventional additive manufacturing machines, the ExAM 510 can use PEEK pellets, as deployed in classic injection moulding. The market price of around €50/kg for PEEK pellets amounts to only 7% of comparable material costs or a cost reduction by a factor of 14. This opens up completely new dimensions in terms of cost efficiencies.
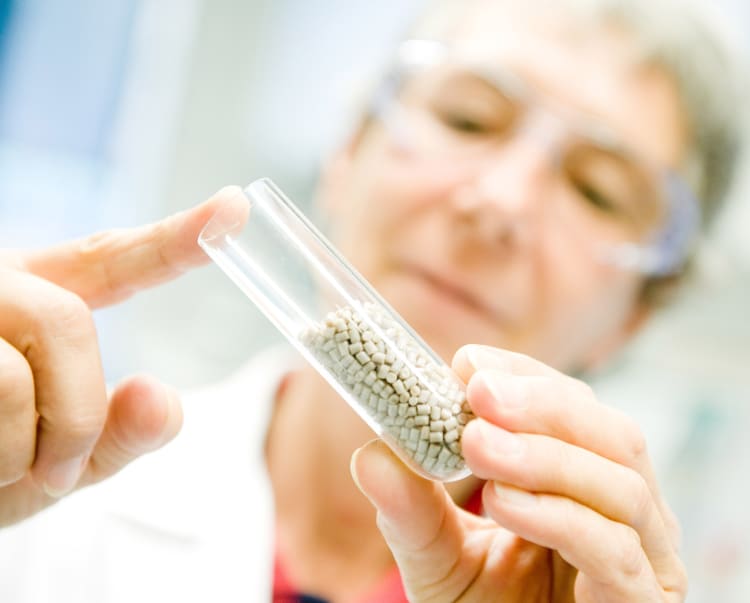
Radiopaque plastic material in implant quality based on polyetheretherketone (PEEK).
Areas of application and potential
Classic areas of application for high-performance polymer materials can be found in automotive, medical technology or aerospace. AIM3D's pilot customers are from these industries. Clemens Lieberwirth, CTO at AIM3D: “The further development of our patented ExAM 255 machine into the ExAM 510 is a technological leap for us. So you could say we are now offering a faster, bigger, hotter and more precise CEM process technology for additive manufacturing.”