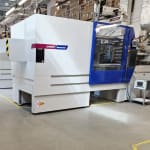
Transparency is an essential part of Bell’s corporate philosophy, with the main emphasis not so much on the transparent plastic materials which take up the lion’s share of the company’s production, but rather on transparent communication directed towards consumers. For the Polish cosmetics manufacturer’s commitment to sustainability is setting high standards. Only particularly energy-efficient machinery and equipment are admitted to the company’s injection molding floor, such as the injection molding machines, robots and dryers from Wittmann.
Visitors are already impressed by the building on their way from the car park to the reception. A lot of wood built into the facade, green roofs, and large old trees surrounding the premises. Here, the strong emphasis on sustainability and responsibility catches the eye at once.
We have arrived at Bell PPHU Kosmetyki in Józefów, 20 kilometers south-east of the Polish capital Warsaw, and are now sitting in the office of Production Manager Waldemar Gula. Through the window on his right, he enjoys an unobstructed view on nature, through the opposite window he keeps an eye on the injection molding floor, which at present contains 48 injection molding machines - all of which have come from the Wittmann Group and are equipped with linear robots from Wittmann. An extension is planned for the next few months, since the demand for cosmetic products from Bell is increasing rapidly.
Output more than doubled with energy consumption unchanged
Everything started 35 years ago with the production of lipsticks. Now Bell covers the entire range of decorative cosmetics and delivers its products to more than 60 countries worldwide.
All primary packaging for make-up, eyeshadow, mascara etc. is produced in-house with a strong focus on sustainability. Servo-hydraulic SmartPower and all-electric EcoPower injection molding machines dominate the picture. The number one decision-making criterion for investments in new injection molding technology is energy efficiency. “With every new machine, the energy efficiency increases even further”, Gula reports. “At the beginning of our efficiency boosting program, we were producing nine million parts per month. Now this has gone up to twenty million, but still our energy consumption in the injection molding shop has remained the same.”
Gula attributes this success to the consistent use of injection molding technology from the Wittmann Group. The machines from the EcoPower series come with highly dynamic servo motors to drive the main movements. Thanks to Kers, the deceleration energy of the drives is recovered and used within the machine, for example to supply the necessary voltage to the control system, or for barrel heating. “Kers stands for Kinetic Energy Recovery System”, explains Bogdan Zabrzewski, Managing Director of the Wittmann subsidiary in Poland. “With Kers, a further reduction of energy consumption by up to 5 per cent is possible.”
The servo-hydraulic SmartPower machines from the Wittmann Group also operate with Kers. In this series, the combination of fast-responding servo motors with powerful constant displacement pumps is the standard. For the injection molding process, this means maximum speed and precision of the machine’s movements with simultaneous minimal energy consumption.
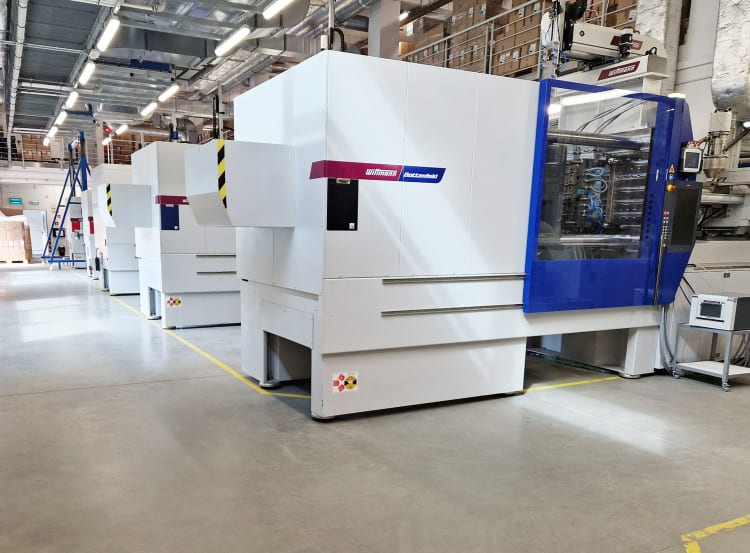
Specialized dryer solution for PETG
On the day of our visit, small, slender bottles produced inside a 16-cavity mold are running off the clock-out belt of an EcoPower 300 injection molding machine. Anyone unfamiliar with the material would take it for glass. In reality, it is PET. “PET looks like glass, but it does not break when it falls down”, explains Gula, which is why this material is playing a more and more significant part in cosmetics packaging. Twelve years ago, Bell was the pioneer in this field. “We were the first cosmetics producer to manufacture bottles for mascara and lip gloss from PET”, says Gula.