Today, primarily PETG is processed, a glycol-modified variant offering a particularly high degree of transparency and impact strength, and simultaneously excellent processing attributes. With their standardized universal screws, the SmartPower and EcoPower machines deliver first-class injection molding results. “Only the drying process presents a special challenge for this material”, Gula discloses. While normal PET is dried with temperatures around 160 °C, PETG requires significantly lower temperatures between 60° and 70 °C. “So, we have specially fitted the Wittmann Drymax dryers for our customer Bell with a cooling device”, reports Bogdan Zabrzewski. In this customized solution, it was of special importance for Bell that the cooling can be switched on or off as required. For the dryers are being used flexibly for other materials, too.
“The Drymax from Wittmann has absolutely convinced us”, says Gula. “We are reaching a dew point of -67 °C with it. This has not been achieved so far by any other dryer model.” Zabrzewski explains the high performance of the Drymax dryer with the use of two desiccant cartridges. “The dryers deliver process air continuously, and drying air of constant high quality.” Thanks to countercurrent regeneration, the dryer also stands out by its extremely energy-efficient operation.
Machines with short delivery times
Bell’s customer base is heterogeneous. In addition to long-standing customers, who place their orders well in advance and invariably for large quantities, there is a daily inflow of many short-term orders involving relatively small batch s. What is more, every national market sets different requirements, all of which has led to a very large number of active molds and frequent mold changes. “Elastic production” is the term used by Waldemar Gula to describe this great flexibility required from Bell every day.
Production planning is getting even more complex due to the innovation cycles becoming shorter and shorter. “Often a completely new packaging design emerges after just one year”, Gula reports. Here, the in-house mold making shop helps the company to keep up with the trend in a fast and flexible way. But the cosmetics manufacturer also expects this flexibility from its suppliers. “Short delivery times are vital for us”, emphas Gula, who has occasionally purchased a Wittmann machine from existing stocks and once bought a SmartPower 300 directly from the booth at the Fakuma.
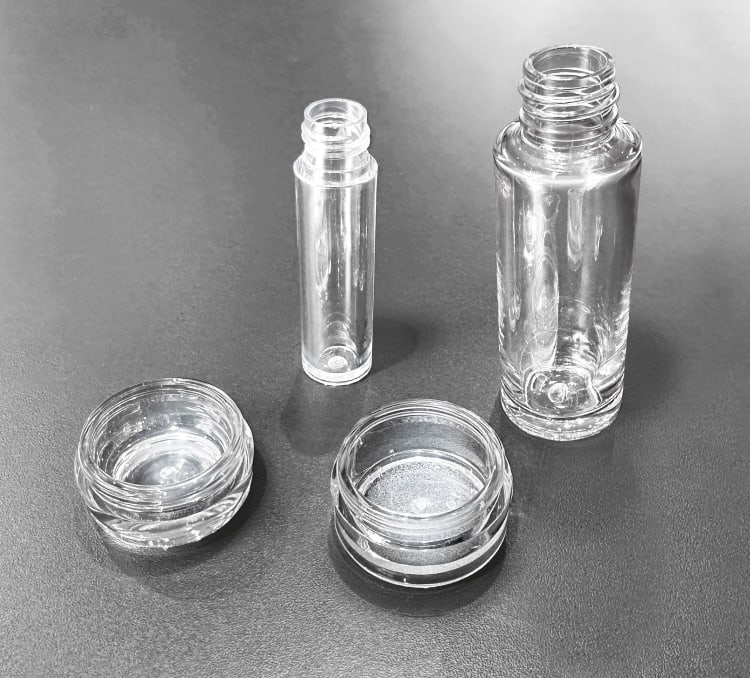
Mono-material packaging in vogue
“We are able to fulfill all packaging wishes. Any form and any color - from transparent and matt-finished right up to high-gloss”, says the Production Manager, and then adds that at present primarily high-gloss surfaces generated inside a mold are increasingly in demand. Here, sustainability is also an issue, since metalizing and chrome plating are more and more often dispensed with to protect the environment as well as the staff members. The current trend favors non-coated mono-material packaging, because it is easier to recycle.
“We bear a great ecological responsibility” emphas Waldemar Gula. “It is important for us to include the consumers’ interests in all our decision-making”. On its website, for example, Bell posts information about sustainable production and instructions for correct disposal of the packaging, so that the plastic materials will be returned to the cycle. Every piece of cosmetic packaging leaving the Bell plant in Józefów is provided with a QR code. This gives consumers very easy access to information about the packaging materials used and the correct way of disposal for recycling. “This is the only way for a circular economy to function”, states Waldemar Gula, “by integrating the consumers into our network as part of the value chain.”