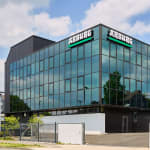
The refurbished Arburg Technology Center (ATC) in Radevormwald is back to normal operations. During the two-year modernisation phase, the Arburg staff in Radevormwald did everything possible to continue to offer customers the best support, with total dedication and flexibility. On 7 June 2024, Arburg Managing Partners Juliane and Michael Hehl, together with the Managing Directors and project leads, cut the reopening ribbon. This event, marked by an open house, followed an exclusive event the previous evening. The two-day event was attended by a total of around 250 guests. In 1982, Radevormwald was the first Arburg location outside Lossburg. Today, it is a sought-after contact point for customers and prospective buyers from the west and north of Germany.
"Our decision to undertake a multi-million Euro investment in the renovation of the ATC not only demonstrates how important our customers and staff are to us, but also emphasises the great significance of the German market for Arburg," stressed Michael Hehl, Managing Partner and spokesperson for the Arburg management team, in his speech. "Today, you can see that the wait has been more than worth it. We're all very proud of what has been created here: a building for the future that marries aesthetics with functionality and environment protection in an outstanding way."
New from old: a model of energy efficiency
Shortly after the 40th anniversary celebrations, the ATC was cleared and gutted in August 2022. All that was left was a shell, which was then outfitted from the ground up with the latest technology. The comprehensive renovations and modernisations included installing photovoltaic and geothermal systems, a triple-glazed glass facade and efficient roof insulation. Following the renovation and thanks to the use of renewable energies, the annual primary energy requirement of the ATC Radevormwald is around just 40% of that of a newly built reference building. The photovoltaic system alone, which produces almost 100,000 kWh a year, covers 60% of the total consumption. The building project is also a very clear reflection of the corporate philosophy: no matter whether developing Arburg products and processes or undertaking a building project, the name of the game is combining high tech and innovation with resource conservation and sustainability.
Two-year transition period: always there for the customer
During the transition period, the team of thirty plus were based in an office building around a kilometre away. At the temporary location, the office work and customer service hotline were able to continue 100% in house. The good, long-standing relationships with customers proved to be an advantage. For application technology and training, the Arburg staff was able to use the customers' machines on site.
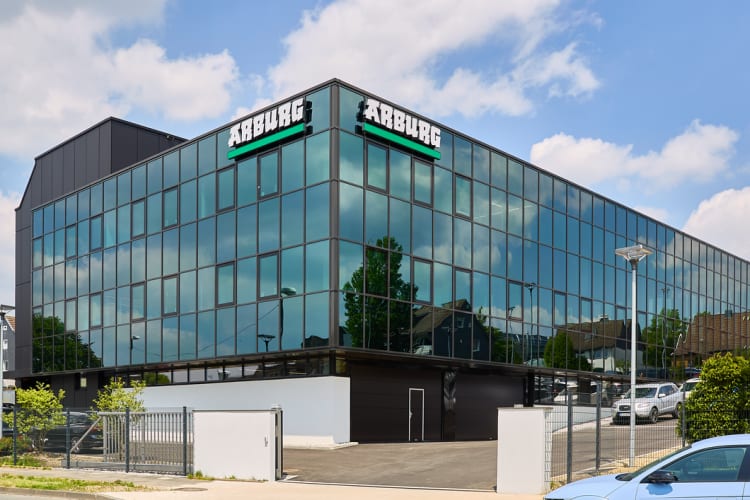
State-of-the-art training rooms and technical centre
The top floor of the ATC now accommodates redesigned training rooms with state-of-the-art presentation equipment. The technical centre also fulfils the latest requirements. Ulf Moritz, Manager of ATC Radevormwald: "In the technical centre, seven injection moulding machines of the latest design with clamping forces ranging from 400 to 1,600 kN are available for our customers, for sampling, testing and training. Each is equipped with a robot system - from the sprue picker and linear Multilift robot systems to the 6-axis robot. The high-quality machine technology and equipment leaves nothing to be desired."
Evening event and open day
An exclusive event was held the evening before the reopening. The highlight was the following open day on 7 June, attended by high-ranking representatives from the company's Lossburg headquarters. The official portion included the ribbon cutting by the Managing Partners Juliane and Michael Hehl together with Managing Directors Gerhard Böhm and Guido Frohnhaus as well as ATC Director Ulf Moritz and project leads Dieter Novotny (Architecture) and Florian Schmitz (Building Services Engineering).
After this, the around 250 invited customers and partners took full advantage of the opportunity to take in the new facilities and equipment. All seven Allrounder machines were in operation, showcasing interesting applications live to demonstrate the wide range of injection moulding products and services. These included the hydraulic Allrounder 270 S with Integralpicker, which reliably processed biomaterial based on sunflower seed shells, high-performance electric machines from the Alldrive series with linear Multilift robot systems and the two-component Allrounder More 1600 with six-axis robot, which produced spatulas made from thermoplastic and liquid silicone fully automatically. The presentation of energy-efficient hybrid machine technology and the assistance functions in the Gestica control system also generated a lot of interest. The programme of events was rounded off with fascinating presentations on hot topics such as digitalisation, sustainability and hybrid machine technology.