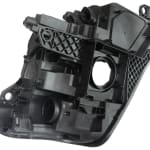
MuCell technology has been widely applied in industries such as automotive, electronics, medical, sporting goods, and green manufacturing. Under the growing trends of lightweighting and carbon reduction, it has become a major breakthrough in sustainable and efficient manufacturing. Particularly in the transportation and bicycle industries, MuCell offers lightweighting solutions that reduce plastic usage while enhancing product strength and durability-further lowering carbon footprints.
Overview of MuCell Technology
MuCell (Microcellular Injection Molding) technology was developed in the 1980s by Professor Nam P. Suh and his research team at the Massachusetts Institute of Technology (MIT), and commercialized in the 1990s. The core of MuCell technology lies in using Supercritical Fluid (SCF) techniques to inject carbon dioxide (CO₂) or nitrogen (N₂) into molten plastic to form a uniform microcellular structure. This process reduces material consumption, lowers product weight, and improves both product performance and processing efficiency.
Development History of MuCell Technology
1980s - Concept Formation and Initial Research
The research team at MIT developed a Supercritical Fluid (SCF) process that injected CO₂ or N₂ as physical blowing agents into molten polymers, forming a uniform microcellular structure.
The initial aim was to reduce material usage while enhancing mechanical properties such as dimensional stability and warpage control.
1990s - Industrial Applications and Patent Development
MIT's research outcomes led to the commercialization of MuCell technology, and the establishment of Trexel, Inc., which specialized in promoting the technology and developing dedicated equipment.
Trexel began applying MuCell technology to sectors such as automotive, electronics, and medical devices, and obtained numerous patents covering gas control systems, mold design, and injection molding process optimization.
Post-2000s - Global Expansion and Technology Optimization
As the technology matured, MuCell gained acceptance in European and Asian markets. Driven by demands for automotive lightweighting (to reduce fuel consumption) and sustainable energy (to reduce plastic usage), many companies adopted this solution.
To meet various application needs, MuCell technology further evolved to include:
- High-precision foaming control (for 3C products and precision manufacturing)
- Hybrid foaming techniques (to improve stiffness and mechanical strength)
Recent Years - Smart Manufacturing and Sustainability
MuCell technology has been integrated into smart manufacturing (e.g., Industry 4.0), enhancing process stability through data monitoring and automation.
The development of MuCell is no longer limited to reducing plastic use and maintaining part rigidity. New applications are emerging, such as ultra-lightweight, high-rebound shoe midsoles, noise-reducing, insulating, cold-retaining industrial products, and biomimetic medical applications.
Many companies are combining MuCell technology with recyclable plastics to further improve sustainability0for example, by using bio-based or recycled materials to reduce carbon footprints.
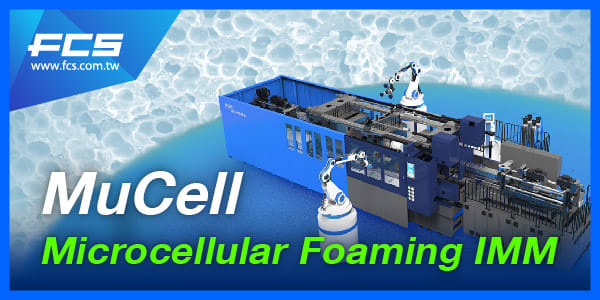
MuCell Molding Process
Compared with traditional injection molding, MuCell adds an extra step where a supercritical fluid is injected. The detailed steps are as follows:
- Step 1: Plastic Melting - Thermoplastics (such as PP, ABS, PC) are melted inside the injection machine, forming a hot viscous melt.
- Step 2: SCF Injection - Under high pressure, a small amount of CO₂ or N₂ is injected into the barrel, saturating the melt with gas evenly.
- Step 3: Injection Molding - The gas-saturated melt is injected into the mold. Due to pressure drop, gas expands and forms microbubbles, resulting in a lighter, more uniform internal structure.
- Step 4: Cooling and Ejection - After cooling and solidification, the microcellular structure remains stable, producing lightweight, high-strength foamed plastic parts.
Environmental and Energy-Saving Benefits of MuCell
MuCell (Microcellular Injection Molding) significantly reduces energy consumption and carbon emissions through material savings, reduced energy usage, improved productivity, lightweight design, and use of recycled materials-meeting corporate sustainability and carbon neutrality goals.
Material Reduction → Lower Carbon Emissions from Plastic Manufacturing
Traditional injection molding requires a large amount of virgin plastic, while MuCell can reduce plastic use by 10%-20% through microcellular foaming.
Carbon emissions from plastic manufacturing:
- Virgin PP, ABS, and PC generate 2.5-6 kg of CO₂ per kg produced.
- MuCell saves 5-20% of material, equivalent to reducing 125-1,200 kg of CO₂ per ton of plastic.
For example, a factory using 1,000 tons of plastic annually can save 200 tons by using MuCell-reducing 250-1,200 tons of CO₂, equivalent to planting 11,000-55,000 trees (each absorbing about 22 kg of CO₂ per year).