Lower Injection Pressure and Machine Power Usage → Reduce Carbon Emissions During Manufacturing
Traditional Injection Molding vs. MuCell:
- Traditional molding requires high-pressure mold filling. MuCell reduces filling pressure by 30%-50%, thereby reducing injection machine energy usage by 10%–40%.
- Injection machines account for about 60% of a factory’s total energy usage. CO₂ emissions from power generation average about 0.5 kg/kWh (depending on the energy source).
Example: A plant using 10 million kWh/year and saving 20% energy with MuCell would reduce around 1,000 tons of CO₂-equivalent to the CO₂ absorbed by 91,000 trees.
Shorter Cycle Times → Improved Productivity, Further Carbon Reduction
MuCell shortens cooling and packing times by 15%–50%, resulting in:
- Higher output per unit time-more parts made with the same energy input, reducing emissions per part.
- Less idle or standby time for machines, minimizing energy waste.
Assuming 20% increased machine productivity, the same output can be achieved with 20% less energy, thus reducing CO₂ emissions accordingly.
Product Weight Reduction → Lower Transportation Carbon Footprint
Automotive Industry Application:
- MuCell can reduce the weight of automotive interior parts by 10%-30% (e.g., dashboards, seat frames, door panels).
- Every 100 kg reduction in vehicle weight reduces fuel vehicle CO₂ emissions by approximately 8-10 grams per kilometer; energy consumption in EVs is also lowered.
- If a vehicle is reduced by 5%-20% in weight, and applied to 100,000 vehicles, it can reduce 250-1,000 metric tons of CO₂ annually-equivalent to planting 22,500-90,000 trees.
Electronics & Packaging Materials:
- Reducing the weight of plastic housings and packaging helps cut fuel consumption during transportation, lowering greenhouse gas emissions.
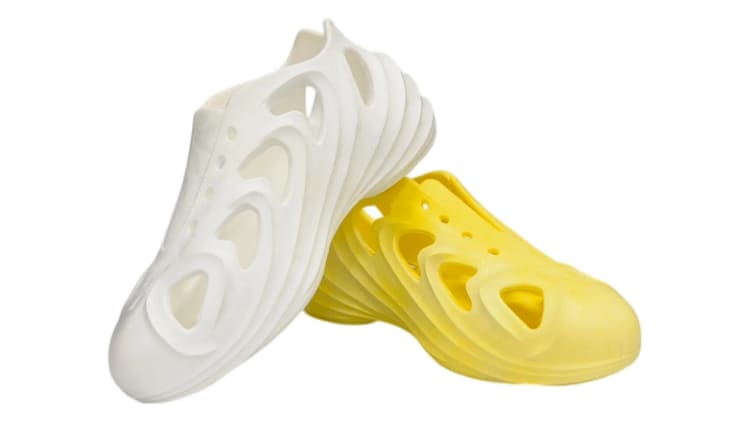
Combining Recycled Plastics (PCR) → Further Reduce Carbon Footprint
Virgin vs. Recycled Plastic Carbon Emissions Comparison:
- Virgin plastics (PP, ABS, PC) generate 2.5-6 kg of CO₂ per kg produced.
- Recycled plastics (PCR) generate 1-2 kg of CO₂ per kg, which is 50%–80% lower than virgin materials.
If MuCell reduces plastic use by 30% and combines 50% PCR, then:
- Emissions from 1,000 tons of plastic can be cut from 5,000 tons CO₂ to 1,500 tons CO₂-a 70% reduction.
- This is equivalent to the CO₂ absorption of 318,000 trees (each absorbing 22 kg CO₂ per year).
- MuCell also enhances the use of recycled plastics by:
- Improving mechanical strength to compensate for rigidity loss in recycled material.
- Lowering injection temperature and pressure to reduce thermal degradation and improve processability.
MuCell not only reduces the use of virgin plastics but also enhances the applicability of recycled materials-expanding the potential of sustainable plastics.
Application Examples of MuCell Technology in Mobility & Bicycle Industry
MuCell technology is expected to see wide application in bicycles, e-scooters, motorcycles, and sporting goods, focusing on weight reduction, strength enhancement, and lower production energy consumption-supporting carbon reduction and sustainability.
Application of MuCell in the bicycle industry. Goal: Reduce the weight of plastic support structures used with carbon fiber and aluminum parts, improving overall energy efficiency.
MuCell Technology in Bicycle Components:
- Internal plastic reinforcement for bike frames → Estimated 5%-10% weight reduction
- Plastic housings for bike lights and e-assist systems → Estimated 25% plastic savings
- Foamed plastic parts for saddles and handlebars → Estimated 15% lighter with added rigidity
Energy and Carbon Reduction Outcomes:
- Each bike is expected to reduce 300-500 g of CO₂
- Annual output of 500,000 bikes = 15,000-25,000 tons of CO₂ reduced, equivalent to planting 1.36 million trees
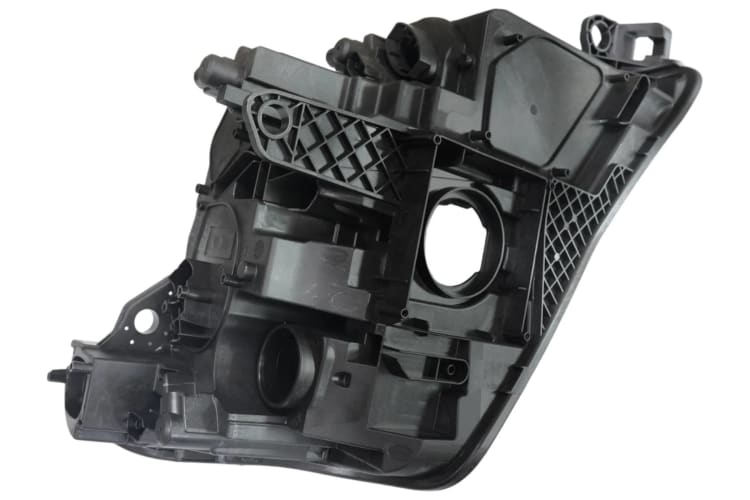
MuCell + Recycled Plastics = Optimal Green Manufacturing Solution
Combining MuCell technology with recycled plastics (PCR) enables not only lightweighting, but also enhances environmental benefits-achieving lower carbon emissions, reduced raw material waste, and a more sustainable production process. This combination offers the best green solution across industries. Key benefits include:
- Reduced use of virgin plastics
- Lower carbon emissions
- Support for sustainable manufacturing
- Cost savings
MuCell + Recycled Plastics enables lightweighting, raw material savings, significantly lower carbon emissions, reduced energy use, and plastic waste reduction.
- Each ton of plastic saved reduces 1,250-2,000 kg CO₂-equivalent to planting 113,000-181,000 trees
- This green manufacturing approach helps companies achieve carbon neutrality goals and promotes the transition to sustainable development
MuCell technology combined with recycled plastics is the optimal strategy for sustainability, carbon reduction, and competitive manufacturing!