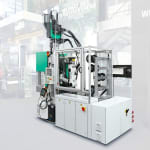
As a pioneer in its sector in Industry 4.0 and digitalisation, Arburg offers numerous "smart" solutions and digital products for efficient plastics processing. This year's Plastpol, to be held from 28 to 31 May 2019 in Kielce, Poland, will focus on the "Road to Digitalisation", turnkey solutions and automation. At stand E30 in hall E, a flexibly automated production cell will be producing elastic tension straps while integrating customer requirements into the running injection moulding process online. The second machine exhibit, an electric Allrounder from the Golden Electric series, will automatically manufacture cable ties.
Plastpol is the central meeting point for the plastics industry in Central and Eastern Europe, and we have maintained a very successful presence here for decades", explains Sławomir Śniady, Managing Director of Arburg Polska Sp. z o. "As a pioneer in digitalisation and a competent partner for turnkey solutions, we are joining our customers on the journey into the digital future of plastics processing and will be presenting practical solutions and applications in Kielce."
Key Industry 4.0 component: Arburg host computer system
Arburg has more than 30 years of know-how in IT-networked production. Its portfolio for production-efficient plastic parts manufacturing ranges from digital assistance packages, predictive maintenance and Arburg Remote Service to the new "arburgXworld" customer portal and Arburg's own MES, the ALS host computer system. As a central component of Industry 4.0, ALS enables online data exchange across production facilities and locations (horizontal integration) as well as with a PPC/ERP system (vertical integration). At Plastpol 2019, both exhibits are networked via ALS. Arburg experts will demonstrate on a monitor how all relevant production and quality data can be recorded and archived, and how continuous traceability of orders, batches or individual parts is possible.
Multiple variants: high-volume production “on demand”
As a "smart" exhibit, a compact turnkey system built around a vertical Allrounder 375 V produces elastic tension straps "on demand" from shot to shot - without any need for conversion, thanks to a clever product and mould design and Industry 4.0 components. The customer requirements are integrated into the running injection moulding process online. At Plastpol 2019, visitors will be able to choose between elastic tension straps of three different lengths in three colours and with three different end piece combinations, entering their variant of choice directly at the terminal. After the order has been transferred to the central Selogica control system, the tension strap is cut to the selected length and handled by a space-saving six-axis robot located within the machine installation area. It places the ends of the strap in the cavities of the 4-cavity mould, where hook/hook, hook/eyelet or eyelet/eyelet combinations are moulded in a cycle time of about 40 seconds. In industrial practice, such an application would be ideal for cable assembly in the automotive industry, for example.
Electric: efficient automated injection moulding production
With its second exhibit at Plastpol 2019, Arburg will be demonstrating the enormous potential of the Golden Electric electric series for the cost-efficient automated production of plastic parts. An Allrounder 570 E Golden Electric with 2,000 kN of clamping force and a size 800 injection unit will produce PP cable ties on an 8-cavity mould in a cycle time of around 20 seconds. The injection moulding machine features compact automation with a Multilift Select. The linear robotic system is integrated into the Selogica control system and removes the moulded parts from the mould to set them down on a conveyor belt.
Individual turnkey solutions
Automation is increasingly enabling additional and more complex process steps to be implemented in injection moulding, as well as simplifying material flows and logistics processes. Arburg turnkey experts at the German headquarters in Lossburg and from the Polish subsidiary provide turnkey systems and work closely with customers to develop individual solutions that increase part quality, process reliability, availability, productivity and cost-effectiveness in the production processes. In addition, turnkey systems can be used to integrate other functions into parts. A holistic view is important in all cases: this begins with product design, but also encompasses mould and process technology and the configuration of production cells, including functional tests and data provision.
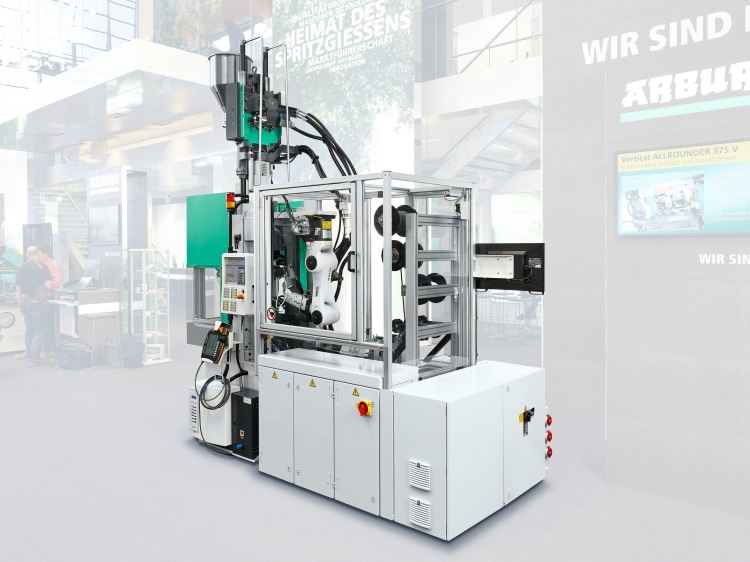
Allrounder 375 V
Source: Arburg