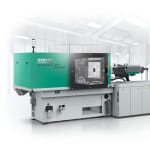
Plastpol from 20 to 23 May 2025 in Kielce is seen as an important indicator of the mood in the Polish plastics and rubber industry. At stand E30 in hall E, efficient and economical injection moulding production will be presented with an electric Allrounder 570 A and a hybrid Allrounder 470 H. Arburg also supplies the appropriate automation from a single source. In addition, a TiQ 2 3D printer will be demonstrating the additive manufacturing of operating resources and robotic grippers. Arburg experts will explain how customers can further increase the efficiency of their production using digital services such as the ALS host computer system and the arburgXworld customer portal.
“We see potential in the energy and electrical engineering sectors in particular”, states Konrad Szymczak, Managing Director of Arburg Polska Sp. z o o., recognising a positive trend away from the automotive sector, known to be weakening. “Everything indicates that investment will continue here in years to come.” He is also focussing on sectors such as packaging, medical technology, technical parts and construction. “Machine technology tailored to customer requirements, assistance functions in the control system and our digital solutions overcome numerous challenges, particularly with regard to reduced energy requirements and waste as well as repeatable and traceable production processes.”
Shatterproof: Electric Allrounder produces drinking cups
At Plastpol 2025, the production of high-quality drinking cups from transparent PC will be presented as a sensible and sustainable alternative to glass and disposable items. The exhibit, an electric Allrounder 570 A with a clamping force of 2,000 kN, is equipped with a single-cavity mould from Adoma. The cycle time for the production of the 0.5 litre cup is around 60 seconds. The Alldrive (A) series fulfils the highest standards of precision and efficiency. The exhibit is equipped with numerous assistance functions that ensure high production efficiency and part quality. The "aXw Control RecyclatePilot" in the Gestica control system, for example, reliably reduces fluctuations in the viscosity of the material and helps to maximise quality and reduce waste. Handling is performed by a Multilift Select 6 linear robotic system. Outside the production cell, a collaborative robot (cobot) places a small gift in each drinking cup and hands it out to the trade fair visitors.
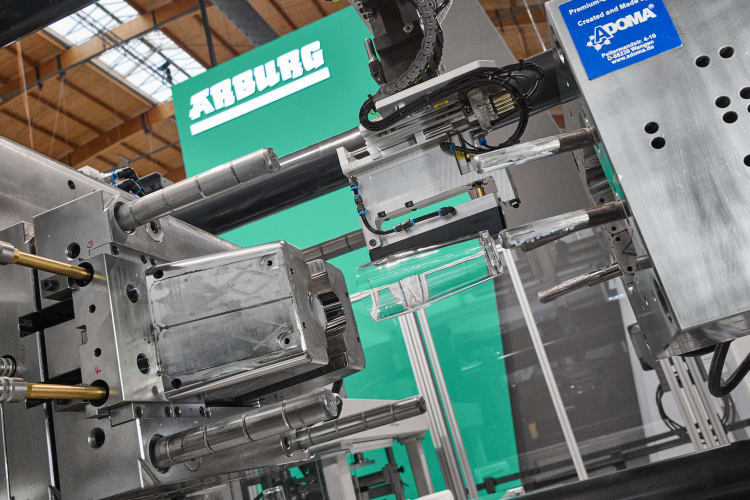
At Plastpol 2025, an electric Allrounder 570 A presents the production of high-quality drinking cups from transparent PC as a sensible and sustainable alternative to glass and disposable items.
Automated: Hybrid all-rounder produces spinning tops
The second injection moulding exhibit at Plastpol 2025 is a hybrid Allrounder 470 H "Comfort" with a clamping force of 1,000 kN. In a cycle time of around 62 seconds, it uses a 4-cavity mould to produce supern spinning tops from PP as give-aways for trade fair visitors. A linear robotic system Multilift Select 8 handles the moulded parts. The gripper is designed so that it can place the spinning tops on a flat surface with a spin of 1,200 to 1,800 revolutions per minute, making the finished product an eye-catcher.
The Allrounder hybrid Hidrive (H) series combines an electric, energy-efficient and precise clamping unit with a hydraulic, powerful and dynamic injection unit. Above all, this series impresses with reduced procurement and operating costs as well as an optimised energy balance and reduced cycle times.
(for more, see press release hybrid machines)
3D printing: TiQ 2 for entry into additive manufacturing
In Kielce, a TiQ 2 filament printer for personalised series production will be demonstrating the 3D printing of end-of-arm tooling (EOAT), fixtures and other equipment. This entry-level device is particularly suitable for everyday use in industrial and injection moulding environments. By way of example, it uses processes fused filament fabrication (FFF) fibre-reinforced filaments into resilient suction pads and mechanical grippers. TiQ 2 manufactures flexibly, quickly and economically on demand. The open material system is another reason why the TiQ 2 3D printer is predestined for successful entry into the world of additive manufacturing. Operation is simple and straightforward.
Solution partner: “More than a machine”
“When customers invest in an Arburg machine, they gain access to exceptional support and resources”, emphasises Konrad Szymczak. “In addition to automation, robotics and after-sales support, these also include digital services.” Visitors can get an overview of the comprehensive digital products and services at various stations on the exhibition stand. For example, Arburg experts will be demonstrating how the Arburg host computer system ALS, digital assistants and the features of the arburgXworld customer portal as well as the Arburg Remote Service ARS all help to make plastics production smarter, more efficient and more sustainable.
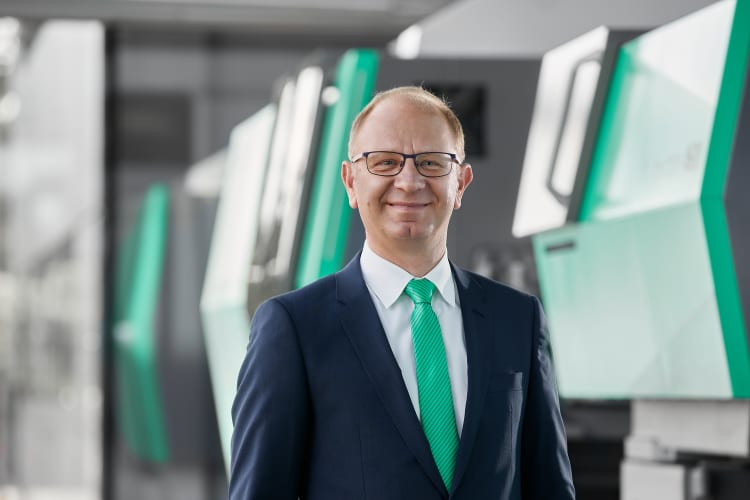
Konrad Szymczak, Managing Director of Arburg Polska Sp. z o o.