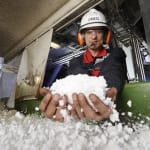
Laboratory staff will carry out a full range of tests on the Keltan EPDM product, including all industry standards such as Mooney and gel tests. Until now, these production quality tests have been carried out by external resources. The Arlanxeo Quality Laboratory will operate continuously on a 24/7 basis, to ensure the consistent high quality of the production plant's output.
By moving to internal tests at the new Q-Laboratory, Arlanxeo is strengthening the competitive position of its global EPDM business in the ongoing challenging market environment, while at the same time optimizing its global footprint. The opening of the new Q-Laboratory comes as Arlanxeo marks the 50th anniversary of the introduction of Keltan EPDM. This well-established brand is best known for its premium quality and best service, and linked to global partnership and sustainable innovation. Keltan has a global footprint with plants in every strategic region with the ability to serve customers with premium products locally.
Opening the new Q-Laboratory, Christian Widdershoven, Head of Keltan Elastomers and Managing Director Arlanxeo Netherlands B.V. said: "This year, Keltan EPDM is marking its 50th anniversary. We are proud of the product's unrivalled track record and globally recognised high quality standards, established here in Geleen.
Since our customers rely on the quality and consistency of our products, manufacturing quality control tests have always been part of the primary process. The opening of this new facility underlines the importance we place on ongoing quality and demonstrates our commitment to this product site. Moreover, it highlights our belief in the future of Keltan, as we take quality control to the next level."
Christian Widdershoven concluded: "We are preparing for the future by developing a more sustainable EPDM production technology. Key examples include the use of Keltan ACE catalyst technology, and the recent introduction of Keltan Eco EPDM grades, the world's first EPDM rubber based on bio-ethylene."