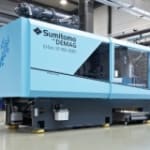
There is every reason for the Plastimagen 2014 to laud the advantages of plastics for a clean environment in its motto. In order to save resources and energy as early as during the production process and simultaneously maximise production efficiency, Sumitomo (SHI) Demag has introduced the Blue Technolution strategy for its entire product range. In Mexico City, Avance Industrial will be showing three energy-efficient, high-performance machine concepts for applications in the packaging and consumer goods sector.
Sumitomo (SHI) Demag high-speed injection moulding machines of the El-Exis series celebrate their 15th anniversary in 2014, with more than 10,000 machines of this series sold worldwide.
At the Plastimagen, Avance Industrial will exhibit the hybrid injection moulding machine in El-Exis SP 450-3000 design (4,500 kN clamping force) with a 96-cavity hot-runner mould from Plastisud SAS, Castelnaudary, France, which manufactures HDPE screw caps (29/25 mm) with a weight of 1.2 g at cycle times of approx. 2 seconds. The ancillary equipment is comprised of a water-cooled compact chiller from Frigel Firenze S.p.A., Florence, Italy, and a hot-runner temperature control from S.I.S.E, Oyonnax, France. To verify the repeatable high process stability and to permit a 100%-check of all screw caps, the production unit is equipped with an IMDvista optical inspection system from the Swiss company IMD Ltd., Brügg, Switzerland. All ancillary equipment is integrated into the NC5 machine control and can thus be operated centrally.
A Systec SP 160-600 with a clamping force of 1,600 kN equipped with a special mould for thin-wall lightweight applications from StackTeck Inc., Ontario, Canada, shows exactly the potential that can be tapped when machine, mould and ancillary equipment are perfectly matched to each other. During the Plastimagen, food containers with a part weight of about 19 g will be manufactured with the system, using IML with cycle times of approximately 4 seconds.
The patented technology from StackTeck promises a reduction in unit weight of between 20 and 40%, while the hybrid machine drive saves up to 60% energy compared with a standard machine. A material conveying system from Motan-Colortronic GmbH, Friedrichsdorf, Germany, plus a water-cooled compact chiller from Frigel Firenze complete the innovative system concept.
When it comes to high-speed production, hybrid machines still offer the best relation between performance and energy efficiency. At the Plastimagen, the new electrically driven SE 180 EV with a clamping force of 1,800 kN delivers a highly impressive demonstration of where the technological journey is heading when the topic of resource conservation is a major factor in the design of a plastics production system. Like all models of the SE product line, this machine is also equipped with "zero-moulding" technology, which eliminates reject and defect production. Direct servo drives and intelligent servo controllers make for high precision and process stability. Closures for fruit juice carafes with a part weight of around 64 g will be produced at the Plastimagen with cycle times of about 10 seconds. The automation control S5-15 is from Sepro Robotique, La Roche-sur-Yon, France. The material conveyors and metering systems from Motan-Colortronic as well as a water-cooled compact chiller from Frigel Firenze complete the system.