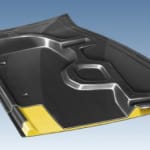
Automotive lightweight activities expanded
Opel Astra OPC seat pan: first serial application for continuous-fiber-reinforced thermoplastic composite containing Ultramid from BASF
The new Opel Astra OPC, a sports coupé that premiers in March 2012 at the Geneva Motor Show, features a seat pan made from continuous-fiber-reinforced thermoplastic laminate (known as “organo sheet”). The plastics used here are polyamide specialties from BASF’s Ultramid range. This is the world’s first auto seat pan in a mass-produced vehicle that uses this technology.
BASF developed two Ultramid specialties for the Opel Astra OPC seat pan: a non-reinforced grade serves as impregnating material for the glass-fiber fabric, while an impact-modified short-fiber-reinforced Ultramid grade is used for overmolding the preform, creating the required ribs and edges by a classic injection molding process. The high strength of the fiber-reinforced laminate allows significantly lower wall thicknesses, reducing the weight of the seat pan by 45 percent.
Body and structural parts for RTM mass production: roof module concept study
In mid-2011, BASF took another step forward on the road to plastic applications on automobile bodies and chassis by establishing its cross-divisional, multi-material Lightweight Composite Team. This team is simultaneously investigating the potential that three plastic matrix systems, epoxy resin, PUR and polyamide, hold for continuous-fiber reinforcement in resin injection processes suitable for mass production, including in particular resin transfer molding (RTM).
Under the Baxxodur and Elastolit R brands, BASF offers solutions based on epoxy resin and PUR systems, respectively, already at this stage. Both of these thermoset materials feature novel curing mechanisms that make them cross-link in a matter of minutes. They can be processed by means of common high- and low-pressure equipment. The new polyamide systems being developed start from very low-viscosity Caprolactam, a precursor of PA 6, and advanced activator and catalyst systems. These thermoplastic composites can accordingly be formed, recycled and welded. Apart from add-on parts like doors, tailgates and roof modules, potential applications also include highly loaded structural automotive parts.
A first demonstrator component based on BASF’s multi-faceted materials for RTM processing is the conceptual study of a multi-segmented convertible roof module in which a polyurethane foam core is sandwiched between carbon-fiber reinforced cover layers. The layer in the core of the demonstrator sandwich plate is a closed-cell structural PUR foam branded Elastolit D. With its low bulk density it acts as a spacer between the skins of the laminate, ensuring extremely high component stiffness. It also provides the roof module with good insulating properties. At a total weight of 2.6 kilograms, the roof segment based on a fiber-reinforced composite sandwich concept reduces weight by more than 40 % compared to an aluminum, and by more than 60 % compared to a steel structure.