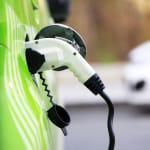
BASF will be showcasing its innovative power solutions at The Battery Show Europe 2024 in Stuttgart, Germany. Taking place between June 18-20, Europe’s largest industry event brings together the battery and electric vehicle (EV) community combining real-world commercial and technical aspects.
As a leading solution provider for various battery applications, BASF will be presenting its range of products specifically targeted to enable advancements of battery technologies and future automotive mobility at booth 10-C110.
Innovative batteries with BASF battery materials and recycling solutions
Battery materials are at the heart of lithium-ion batteries as they significantly determine their performance. BASF offers one of the broadest cathode active material (CAM) portfolios with a well-established position in key CAM technologies like NCA (nickel-cobalt-aluminum-oxide), NCM (nickel-cobalt-manganese-oxide) and LCO (lithium-cobalt-oxide). By leveraging industry-leading R&D platforms and passion for innovation, BASF Battery Materials already today looks into future CAM products ranging from cost-efficient manganese-rich solutions to high-performance ultra-high nickel products, high-performance LMO (lithium manganese oxide) as well as CAM dedicated for sodium-ion applications. BASF also provides base metals sourcing and management to ensure a stable, responsible, and sustainable supply chain for the production of cathode active materials.
In addition, BASF’s portfolio also includes comprehensive battery recycling solutions in order to offer its customers recycled metals with a lower carbon footprint compared to virgin metals, thus helping to meet regulatory requirements. In March, BASF started operating its prototype metal refinery for battery recycling in Schwarzheide, Germany, to further improve the process of recovering valuable metals such as lithium, nickel, cobalt, manganese and copper from end-of-life batteries and battery production scrap. It complements BASF’s existing CAM plant and the battery recycling plant to produce black mass, which is scheduled to start operations later this year. The portfolio addresses various customer requirements, including closed loop offerings and digital end-to-end solutions to set up regional recycling value chains.
Products for high voltage connectors
With the Ultramid DC grades (Durable Color), BASF offers a broad portfolio of engineering plastics for the eMobility market – even in the flame-retardant sector. High technical requirements from the industry require innovative solutions based on PA66 and PA6. In the case of already proven Ultradur (PBT) products, color stability can be largely guaranteed, especially in orange (RAL 2003) which is in high demand in the industry. In addition, some grades are specially optimized for laser markability with high contrast values.
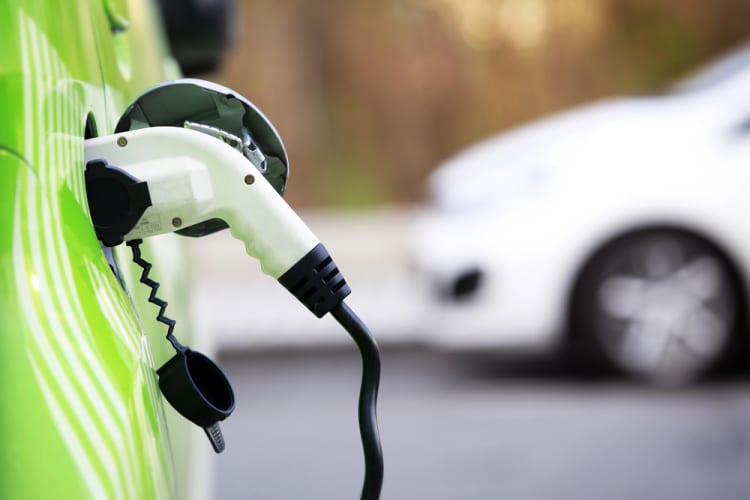
New advancements in busbar technology for high voltage power electronics
Busbars play a crucial role in providing electrical isolation and connecting various components in high voltage power electronics. In the case of battery electric vehicles (BEVs), busbars serve as a connection between the inverter and the electric motor or play an important role inside the HV battery pack. This requires a high level of electrical insulation. In case the plastic is used in a busbar holder function, a certain stiffness and strength must be ensured. On the other hand, being used as a busbar sheathing for HV in the battery pack the orange signal color is a must-have. Additionally, these plastics need to show excellent temperature resistance and electrical isolation properties even after harsh aging. All Ultramid and Ultradur grades for busbars meet these requirements.
Furthermore, the use of thermoplastic polyurethane (TPU) Elastollan in busbar applications offers stronger resistance to thermal cycling due to optimized thermal linear expansion. This reduces the risk of cracks occurring during temperature changes which increases the safety standard.
Materializing eMobility ambitions with Elastollan (TPU)
The increasing demand for a broader charging infrastructure for Electric Vehicles (EV) is driving the need for robust and lasting charging cables at home and on the road. Those cables need to withstand harsh environmental conditions and be rugged enough to hold up over time. To cope with these challenges BASF's TPU Elastollan are particularly suitable for cable sheathings ensuring a strong resistance to UV, weathering, ozone, and microbes. To make the charging process safe, cables should be made flame retardant without halogens, and must be coilable and flexible. Elastollan further sets itself apart from other materials by being recyclable.