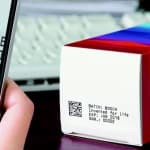
Consistent process safety
Detailed information about each machine, line or process status is provided by the Condition Monitoring platform. It records data in real-time, enabling maintenance staff to react before cost-intensive process deviations or downtimes occur. An example shown at interpack is the monitoring of filters, which ensure the consistent sterility of production processes. Special sensors within the machine control the sterilization status of these filters. In case pre-defined parameters are infringed, operators receive a notification. This enables them to initiate maintenance activities quickly, and to prevent product loss due to non-sterile processes.To ensure constant product quality, all process steps are subject to strict regulations. This is particularly true in the pharmaceutical industry, for instance regarding electronic records and signatures. The Bosch Pharma Manufacturing Execution System (MES) enables pharmaceutical companies to take the step towards a transparent, paperless production. To this end, Bosch works with the software provider Parsec Automation Corp. and configures the MES software TrakSYS according to the requirements of the pharmaceutical industry. Together with a complete audit trail, it includes all necessary functionalities to manage machines and processes, and to generate electronic batch records (EBR), thus facilitating the approval for batch releases by qualified persons. The Bosch Pharma MES can be integrated into any Bosch or third-party machines and lines, as well as into complete manufacturing facilities.
Counterfeit-proof packaging
When it comes to packaging, pharmaceutical manufacturers must also comply with strict regulations. The unambiguous serialization of secondary packaging aims at protecting patients from counterfeit medicine, and ensures the traceability along the production chain. The Track & Trace solution from Bosch fulfills both requirements. It consists of the CPI software and machine modules, which are connected within the serialization process. At the machine level, CPS modules print data matrix codes onto folding cartons, verify the codes and, if required, equip the packaging with a tamper-evident seal. The CPI software integrates the CPS modules into the company IT. This ensures a reliable serialization - from the allocation of the serial numbers through to the last aggregation step."In the food industry, the requirements regarding product safety are also rising continuously," says König. "While we already drew on the comprehensive know-how of the Bosch Group during the development of our Track & Trace solution, for instance from the automotive division, we can now transfer this expertise to the food industry." At interpack, Bosch showcases such an application for yoghurt packaging for the first time. The packaging machine is connected with the CPI software. The software transfers the information directly into the Bosch IoT Cloud. Thanks to the QR code printed onto the lid of the yoghurt cup, end consumers can verify whether they have bought an original product. "The cloud further enables producers to actively communicate with their customers," König explains. "In case of a faulty product, consumers can immediately inform the manufacturer - and support them in securing the quality of their products." Apart from product verification, manufacturers also make use of well-known online marketing possibilities via the code by adding further, product-specific information such as ingredients, allergens or recipes.
Bosch at interpack: hall 6, booth A30-C58