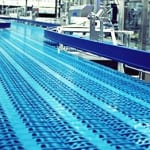
"The growing challenge is to manufacture smaller, stronger, higher performing products faster and more cost effectively so that OEMs are able to meet market demand and remain competitive," said Scott Sutton, president of Materials Solutions for Celanese. "Celanese has developed the broadest, most technically advanced engineering polymer platform that continues to advance in strength, durability and wear to keep up with our customers' most challenging tribological requirements."
Since so many external conditions influence tribological behavior, Celanese experts work directly with manufacturers to select and test the advanced engineering polymers that will work best for each application. Celanese polymers are developed with precise specifications so moving parts have little to no friction and noise while also withstanding extreme temperatures, chemical contact and speeds. Additionally, through the use of these polymers, manufacturers can eliminate oil, grease or other lubrication additives, thereby removing dust and dirt, which improves overall mechanical operation and service life.
The Celanese tribology product platform includes the most advanced engineering polymers to help meet emerging trends across many market segments, including stronger, more flexible conveyer systems for manufacturers as well as lighter weight, more durable bearings and bushings for consumer products. Celanese also fills tribologically demanding needs for manufacturers of consumer electronics, office furniture and automotive components.
Celanese has the industry's broadest tribology product platform available today. The portfolio includes these materials, each with multiple grades, as well as custom solutions:
- Celanex polybutylene terephthalate (PBT) is effective in aggressive environments that require contact with harsh chemicals and flame retardant properties enabling longer service life with less part maintenance and downtime.
- Celstran Long Fiber Technology is commonly used to replace metal because of its unique combination of mechanical properties, light weight and strength. It performs as well as metal in many applications while costing less and providing greater design freedom.
- Hostaform/Celcon acetal copolymer is well established as the preferred solution to meeting tribological requirements across a wide range of applications and markets.
- Hostaform Extreme Glass Coupled (XGC) POM is a tough, stiff, low-friction glass-fiber material that maintains dimensional stability in extreme temperatures and in hostile environments.
- Hostaform SlideX POM offers superior wear, noise and friction performance for applications requiring premium tribological performance.
- Fortron Polyphenylene Sulfide (PPS) is an inherently flame retardant and chemically resistant polymer that performs well in high temperatures.
- GUR is an ultra-high molecular weight polyethylene that provides extreme impact and abrasion resistance in temperatures as low as -200C.