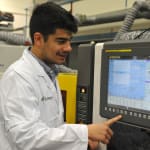
Clariant’s Additives business and Floreon-Transforming Packaging Limited announce an exciting new collaboration to further extend the performance properties and market potential of biopolymers, whilst preserving their environmental benefits.
By integrating the benefits of Clariant’s additives with Floreon’s proprietary material solutions, the collaboration aims to open up additional possibilities for plastic manufacturers and brand owners to consider biopolymers as a viable, low carbon footprint alternative to fossil-based plastics for both single-use and durable applications. Markets set to benefit from the new enhanced grades include rigid and flexible Packaging, Electrical & Electronic equipment (E&E), Hygiene products, Consumer goods and Automotive.
Floreon develops and markets proprietary compounds based on PLA and containing 70-90% renewable, plant-based raw materials, thus containing carbon sequestered from the atmosphere by plants. They are typically mechanically tougher than traditional PLA and can deliver significant energy savings in processing. Floreon compounds are recyclable and they can also be composted via industrial composting. That makes Floreon’s materials viable for applications where, at this stage, contamination with food waste and organic matter make mechanical recycling unfeasible.
Clariant’s industry-leading portfolio of sustainable additives includes a wide range of bio-based additives, which reliably deliver both high performance and sustainability to the plastics value chain. Introduced at the K 2019 Plastics Trade Fair under the Exolit OP Terra, Licocene Terra and Licocare RBW Vita trade names, they help to reduce fossil resource intensity and enable more sustainable material choices. Clariant’s experts will support the Floreon development team to enhance the performance possibilities and processing characteristics of bioplastics.
The scope of benefits is vast. Examples include achieving less energy use and faster cycle times by increasing the processing efficiency or adding completely new properties to the material. Product manufacturers will have the possibility to tailor compounds to suit specific processing technologies and applications, including in some cases those where bioplastics have so far not been able to meet the challenges of demanding conditions or environments.
Shaun Chatterton, CEO, Floreon-Transforming Packaging Limited, said: “Brand owners and plastic converters are seeking more sustainable material solutions to offer their customers, driven by goals ranging from recyclable solutions and improving waste management to lowering carbon footprint and reducing resource use. Floreon can really contribute towards these goals. As a small business, our team is very excited to be able to take the benefits of biopolymers to new heights by drawing on Clariant’s extensive capabilities in developing additives focused on the performance needs of the plastics industry. Floreon has the potential to transform not just packaging but many industries, and we expect to launch our first product from this collaboration into market during the first half of 2020.”
Stephan Lynen, Head of Business Unit Additives, Clariant, commented: “We are excited to be working together with Floreon using the advantages of our range of sustainable additives to close the performance gap between biopolymers and other materials. This is just another way we can contribute to giving the plastics value chain a greater choice of options for meeting sustainability targets and consumer demands, and in doing so, support the transformation to a circular economy. For society, our environment, and future generations, it is our responsibility to continuously improve sustainability performance and reduce carbon footprint and waste.”
Clariant’s collaboration with Floreon constitutes together with Clariant’s EcoCircle, a corporate-wide initiative supporting the transition from a one-way plastics value chain to a circular plastics economy, another step forward to jointly develop new circular materials and technologies together with partners from the entire value chain to enable a circular economy.