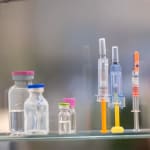
The pandemic has thrown into sharp relief the importance of cleanrooms in the manufacturing of medical products. Packaging companies have developed special solutions to meet these requirements.
In doctors’ surgeries, operating theatres or vaccination centres, syringes, ampoules, swabs and the like need to be quickly on hand and above all sterile. To ensure that in extreme situations, life-saving medical products reach their point of use in perfect condition, they are specially packaged. Even the packaging process itself takes place under specially protected conditions: in the cleanroom. Computer chips and other electric components or automotive parts are also packaged under cleanroom conditions, i.e., wherever air-borne particles could contaminate and damage the product. Air locks prevent particles from being carried into the working area. Standards have been developed to ensure that these processes take place under the same conditions all over the world. For example, cleanrooms are divided into various classes that determine how many particles per cubic metre of air the room may contain. In Germany, for example, the handling of consumables like packaging is governed by VDI Guideline 2083 Sheet 9.2. This means that even suppliers of packaging materials need to adhere to the most stringent standards.
Sharp rise in demand for cleanroom technology
The global COVID-19 pandemic has placed heavy demands on medical technology and pharmaceutical companies: alongside rapid tests, face masks and medicines, production of the necessary consumables for ICUs also had to be quickly ramped up. It goes without saying that these products must be manufactured and packaged in cleanrooms. It is therefore not surprising that demand for the solutions of cleanroom specialists has grown significantly.
Research and Markets forecasts that the market for cleanroom technologies will grow from USD 5.1 bn in 2020 to USD 7.3 bn in 2025. This corresponds to a mean growth rate of 7.2% by 2025. The growth of this market will be driven mainly by strict statutory regulations, the expansion of the biologics segment, the increasing demand for sterile pharmaceutical preparations and for medical devices, and the technological advances in cleanroom technology. The rising demand in emerging markets and increasing focus on energy-efficient cleanrooms will also offer substantial growth opportunities in the next few years, predict the analysts.
Controlled manufacturing environments ensure process safety
The manufacturers of medical technology products often use service providers to package their products. These contractors specialising in the packaging of especially sophisticated items also offer cleanrooms and the necessary machines and specialist expertise. During transport from the manufacturer to the packaging contractor the products are exposed to the risk of contamination. They therefore need to be professionally sterilised before packing using various processes such as gamma irradiation or fumigation with ethylene oxide. For the latter, the medical products are sterilised with ethylene oxide in a vacuum/pressurisation chamber. Ethylene oxide also penetrates the packaging and reliably kills microbes. Plastic packaging is especially suitable for primary packaging purposes.
Automation increases safety
Packaging and bottling machines used in cleanrooms are specially designed and certified. To ensure thorough cleaning, these machines are made from stainless steel and other materials authorised for use in cleanrooms. The equipment needs to be easy to dismantle and the downtime for cleaning should be kept to a minimum. Moreover, such equipment is increasingly being automated to reduce human intervention and thus the risk of contamination. In recent years, packaging machine manufacturers exhibiting at Fachpack have increasingly been offering modular solutions. Manufacturers and contract packagers can choose the combination best suited to them and tailored to the specific tasks involved, from packaging, palletising and labelling to the feeding and assembly of medical technology products. In this context, modern robot technology ensures high precision, productivity and product safety. Manufacturers emphasise the low particle emission of robots, which is especially important in cleanrooms. As with the packaging machinery, there are also scalable and modular systems for robots, allowing for a flexible response to modified products and packaging.
Although medical products do impose special requirements on packaging, the exhibitors at Fachpack already have suitable solutions on offer: packaging materials, packaging and accessories, bottling and packaging machinery, labelling, marking and identification technology, packaging printing and finishing equipment, palletising technology, intra-logistics or services for the packaging industry.