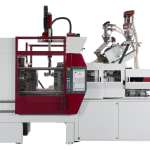
From May 20 to 23, Wittmann Battenfeld Polska will present to trade visitors its latest injection molding technology at the Plastpol in Kielce, Poland, at booth No. 6-08 in hall 6. The main highlight of the exhibition program will be a SmartPower Combimould machine equipped with a servo-electric injection aggregate. Examples demonstrating the company’s expertise in the area of robots and auxiliary equipment will be on show as well.
The Polish market is one of the most important European markets for the Wittmann Group. Consequently, the Plastpol is a key platform for presenting its latest technologies to this market.
The highlight of this year’s product presentation is a SmartPower Combimould machine with a servo-electric injection unit. With this servo-electric injection aggregate, the machine combines the advantages of the servo-hydraulic SmartPower, in particular its flexible, generously dimensioned mold space, with those of the all-electric EcoPower in terms of its highly dynamic control system with extremely accurate shot-by-shot repeatability.
At the Plastpol, the production of a bottle opener made of PC and TPE will be demonstrated on a SmartPower 120/350H/130S with a servo-electric main aggregate, using a mold supplied by FKT Formenbau und Kunststofftechnik, Germany. The SmartPower B8X 120/350H/130S comes as a compact Insider solution with a W918 robot from Wittmann and a conveyor belt integrated in the work cell. The robot inserts the metal parts fed from a magazine plus the decorative foil into the mold, where they are over-molded with polycarbonate. The resulting base body is subsequently passed on to the second station by a rotary unit and there over-molded with TPE, to give it a better grip. The finished parts are then deposited on the conveyor belt of the Insider cell.
Material drying will be carried out inside an Aton plus beside-the-press dryer, from which the material transport can be controlled, such as that to fill the drying hopper and to feed the two materials PC and TPE (not pre-dried) to the injection units. Via the generously dimensioned touch-screen terminal of the Aton plus, the most important dryer information such as the dew point can be visualized, and the drying temperatures or handling times can be adjusted.
Automation and auxiliaries
In addition to the robots and auxiliary appliances connected to the machine on display, several stand-alone solutions will be shown at the Plastpol as well.
To provide some pleasant entertainment at the trade fair booth, a Wittmann robot will be used in combination with a photo box. Here, visitors can have fun taking photos of themselves sitting on the horizontal axis of the robot. After the photo has been taken, the time while the photo is being printed out can be used to examine the structure of the Primus 148T robot model used in in this case. The appliance comes with a generously dimensioned Z carrier (as its main axis), which provides the necessary stability for handling tasks on injection molding machines with a clamping force of up to 9,000 kN. Close-up examination of the (vertical) Y axis’ performance is also possible. This axis is used in several different appliances from Wittmann and offers sufficient reserves to support precise movements of grippers weighing up to 35 kg. The drive concept of the 148T is laid out for payloads of up to 20 kg.
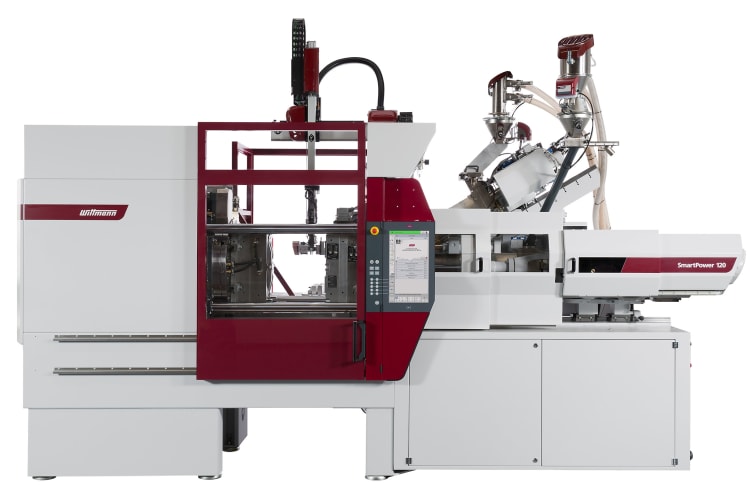
The auxiliary equipment to be shown by Wittmann Battenfeld Polska at this year’s Plastpol includes a central materials handling system, to demonstrate to trade fair visitors the advantages offered by the Feedmax B central material loaders, which are made of stainless steel. Various options to increase production reliability can be tried out with the Codemax, a RFID-controlled material distributor. Valuable insights can also be gained about the complex functionality of the M8 network control system.
In the area of mold tempering, the enormous savings potential of combining a digital flow monitoring system for each cooling circuit with a temperature controller will be presented. The WFC 120 is a monitoring device for keeping flow rates and temperature in every circuit within tolerance. Each circuit is equipped with a maintenance-free flow measurement unit for operating temperatures of up to 120 °C. At the fair, a WFC 120 with manual control valves will be contrasted to one with automatic proportional valves. Using the automatic step motors of the latter offers the advantage of having the set flow rate or the set temperature for the application regulated within tolerance limits automatically, thus maintaining reliable production conditions without intervention by machine operators. If in a combination of Tempro plus EcoDrive with WFC 120 the system is also set for a specific flow quantity, the pump speed varies accordingly, too, without any intervention by personnel. What is more, energy savings of up to 70% can be achieved by combining Tempro plus EcoDrive and WFC 120 with each other.