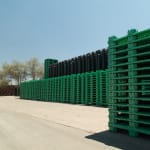
Nature lovers and globetrotters alike find even the mere mention of this region breath-taking: Patagonia. Besides rugged mountains shaped by Pacific winds and impressive landscapes, it is above all the fjords and coasts that – Covid travel restrictions apart – attract more and more visitors to this strip of land in southern Chile every year. Michel Compagnon from Santiago de Chile is one of them. Besides the magnificent spectacles of nature, one thing in particular caught his eye: discarded fishing nets and ropes, which are a burden on the environment and can bring the life of many sea creatures to an unhappy end. When asked about this, the local fishermen simply described the carelessly discarded rigging as waste. But for Compagnon, Commercial Manager at the plastics recycling company Comberplast, the unpleasant scene became a project to save the oceans and the incomparable beauty of Patagonia. And that is how the Atando Cabos project started.
What began in 2016 with a handful of samples in a travel suitcase is now a project that transforms over 3,000 metric tons of ropes and nets into new products every year. The entire recovery process, from shredding and cleaning to the extrusion and injection moulding of new products, takes place on site at the Comberplast facility in Santiago de Chile. For more than 25 years, the company has been committed to the circular economy, even before circular concepts in plastics recycling became the latest buzzword.
The many international awards for environmental protection and innovation confirm Julio JR Compagnon, CEO of Comberplast and co-founder of Atando Cabos, that he is on the right track: ‘The global awards make me so proud. They show us that another path is possible and that doing the right thing for people and the environment can also be a profitable business. Or to put it another way: the real purpose of business should always be to solve problems in both economically and environmentally sustainable ways.’ The large amounts of old fishing nets, lines and other discarded plastic materials are recycled and converted into innovative new products, for example for the agricultural and mining industries, or also turned into green pallets for an international brewery.
Since 2020, Comberplast has relied on the shredding technology of Lindner’s Micromat 1500, equipped with an optimised cutting system from the Mono-Fix kit. Julio Compagnon explains: ‘We process plastic waste from fish farming and fishing companies. These materials were developed by very clever people not to ever break or tear. Shredding is therefore an especially big challenge. In processing, we are always looking for new solutions to tackle more difficult projects and to keep production economically viable. In Lindner, we found an experienced partner who was willing to go the extra mile with us – not many companies will do that.’
The delivered materials are usually heavily loaded with abrasive substances such as sand, stones or organic material. That is why, when selecting the shredder, the main concerns besides high energy efficiency were the costs of wear and tear. Now, after a year in operation, Compagnon is pleased: ‘We got the Micromat in January 2020 – just at the start of the pandemic. The situation required us to find new ways of commissioning and servicing despite the physical distance. Thanks to the great cooperation of the Lindner team in Austria, the Chilean sales partner Ingeniería Delta Limitada and our technicians here on site, we were able to successfully install and commission the shredder – everyone involved did an excellent job. Since then, our shredder has been running like clockwork and we look forward to many more joint projects in the future.’