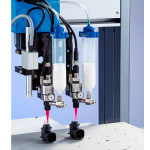
Almost 900 plant engineering and management personnel from diverse industries within the United States weigh in on specific challenges they face relating to their dispensing methods. Find out how to address some of these challenges to improve control in manufacturing processes.
The methods for dispensing adhesives, epoxies, grease, silicone, oils, sealants and a multitude of other assembly fluids cover a wide spectrum of techniques – from manual applications like squeeze bottles, toothpicks and hand-plunger syringes to semi-automated tabletop dispensing robots.
Each dispensing method presents unique challenges as manufacturers attempt to scale the sophistication of their fluid-dispensing processes to meet requirements for quality, volume throughput and cost efficiency.
Looking at a series of in-depth research studies conducted over a five-year period focused specifically on fluid dispensing in assembly processes, Nordson EFD has identified the top most common dispensing challenges. Having long been a key player in the design and manufacture of precision fluid dispensing systems for benchtop assembly processes and automated assembly lines, the company shares key guidelines for solving these challenges to improve process control.
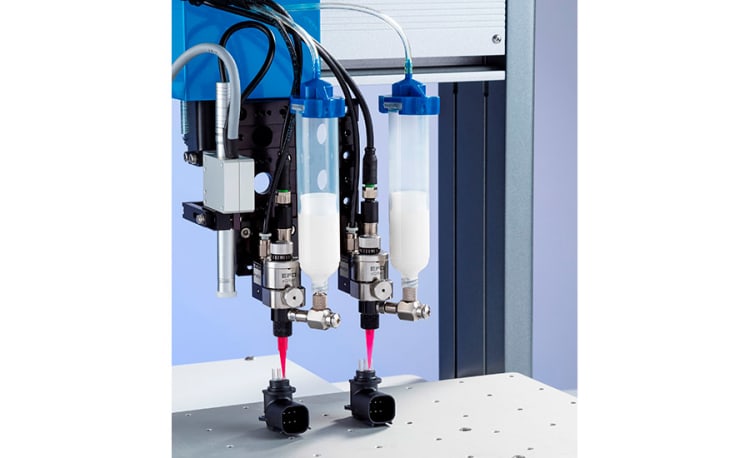
Methodology
Sponsored by Nordson EFD and conducted by Clear Seas Research, the market study was conducted over a five-year period, in three separate waves, from 2014 through 2018. Using largely identical questions, and similar size respondent bases from similar geographic sections of the country and industries, results from the three studies were then combined to achieve trending data.
890 respondents participated from manufacturing companies throughout the United States. Respondents were qualified as being involved in deciding which assembly fluids and dispensing equipment are used by their organizations' manufacturing process.
Highest scoring dispense challenges
These are the highest rated challenging factors relating to dispensing systems, based on data from the 2018 respondents:
- Shot-to-shot repeatability
- Shot-to-shot accuracy
- Equipment maintenance
- Need for faster production
- Fluid waste
- Operator training
- Rework, rejects
Shot-to-shot repeatability
This challenge appears to be more prevalent when using squeeze bottles and medical syringes to dispense assembly fluids for low-volume production. 44% of respondents from 2018 said shot-to-shot repeatability was the biggest challenge when using these manual methods. This is not surprising considering that the repeatability of the process likely varies from operator-to-operator.
Shot-to-shot repeatability becomes less and less of a challenge as manufacturers use more sophisticated dispensing equipment to apply assembly fluids in their production processes.
Consider that 37% of respondents cited shot-to-shot repeatability as a challenge when using air-powered benchtop dispensers. 32% of respondents that used pneumatic valves systems cited shot-to-shot repeatability as a challenge, and only 26% of respondents using positive displacement dispensing systems said this was a challenge.
Although, improving the sophistication of dispensing equipment can solve the problem of shot-to-shot repeatability, so can following other simple guidelines like ensuring there is no air in the assembly fluid being used. Air bubbles in fluid are undoubtedly one of the top culprits in ruining deposit consistency for manufacturers.
There are many ways to prevent air entrapment from ruining deposit consistency, including:
- Using a centrifuge to purge air from fluid in syringe barrel fluid reservoirs prior to dispensing
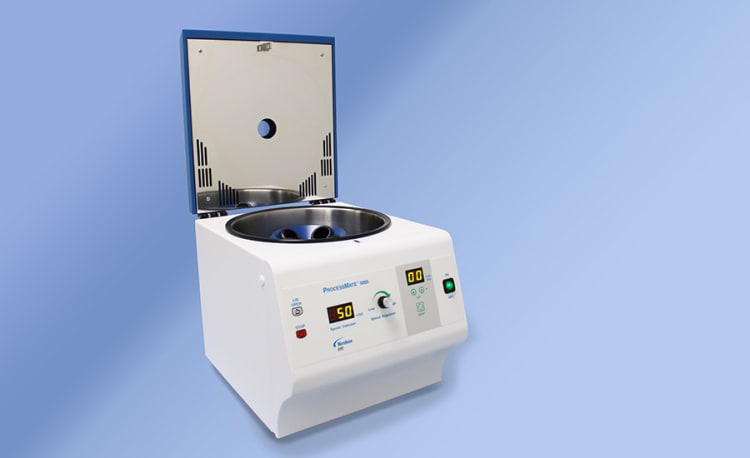
- Using the proper, high-quality dispensing components designed to purge air as dispensing takes place
- Following the guidelines for thawing frozen assembly fluids to prevent freeze-thaw voids in fluid
Shot-to-Shot Accuracy
Perhaps not surprisingly more respondents reported shot-to-shot accuracy as a challenge when using squeeze bottles and medical syringes to apply fluids than when using air-powered dispensers, 41% vs. 35% respectively according to 2018 respondents.
Dispensing accuracy becomes less of a challenge when using pneumatic valve systems, such as diaphragm and needle dispense valves. Precision increases as manufacturers use advanced jetting systems, such as electro-pneumatic jet valves and piezo-electric jet valves. These latest advances eliminate the barrier between speed and accuracy when dispensing assembly fluids.
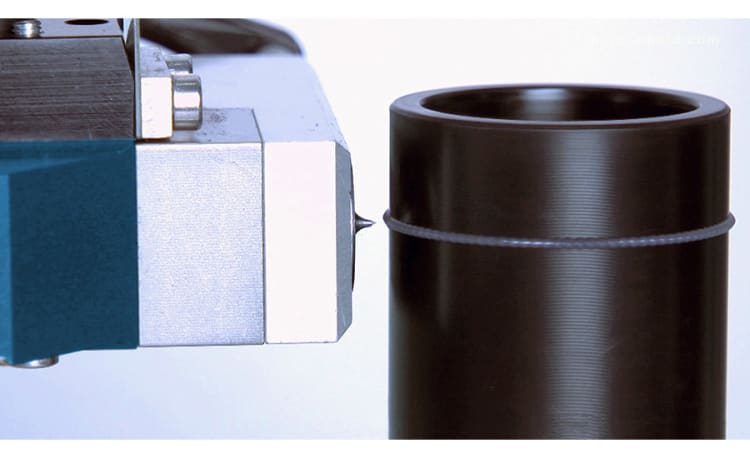
Recent advancements in air-powered dispensers are also helping solve the dispense accuracy challenge. Improvements in software allow features like multi-shot capabilities where an operator can program the dispenser to dispense multiple, accurate deposits with a single press of the foot pedal. This feature also can help speed production.
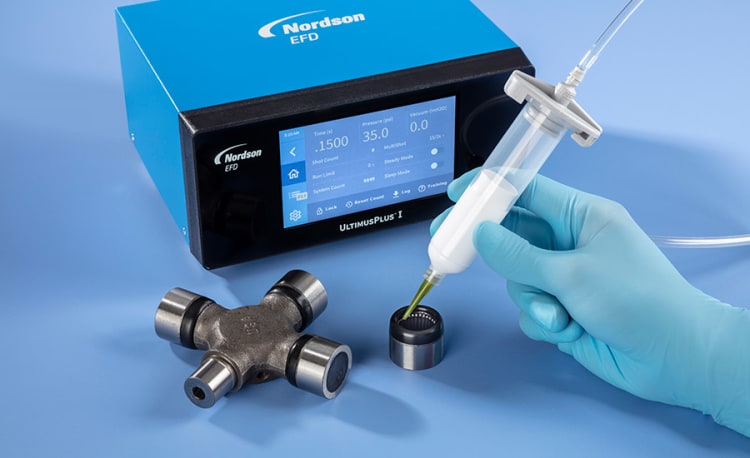
Entrapped air in assembly fluids can also impact shot-to-shot accuracy. Purging any air-entrapped fluid through the valve system or syringe barrel reservoir prior to use is key to experiencing consistent, accurate dispensing.