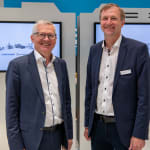
How to achieve consistent recycled pellet quality in plastics recycling by exchanging data between the extruder and washing system, and how intelligent energy management reduces costs, was revealed at IFAT in Munich by the Erema Group and Lindner. This presentation saw the two Austrian companies show the first results of their joint venture.
Breaking new ground in plastics recycling means assessing the value chain from end to end. The big opportunities for the future are in fine-tuning the individual process steps; from the collection of recyclable materials to the recycling process and the end product. This is exactly where the cooperation of Lindner and the Erema Group comes in, officially launched following the 50/50 founding of the holding Blueone Solutions in August last year to which shares of Lindner Washtech were contributed. The expertise and experience of Erema, a manufacturer of extruders and filtration solutions for plastics recycling and the largest company within the Erema Group, has now been combined with the expert know-how from Lindner Washtech, a leading provider of all-in-one solutions for shredding, sorting and washing plastic feed materials.
Data transfer ensures more efficient recycling processes
Process control is an especially important aspect of plastics recycling, which is why standardising the process control system was what the two companies focused on first. "Together, we have developed a platform that allows data to be exchanged between the extruder and the washing system," says Manfred Hackl, CEO of the Erema Group at IFAT in Munich. "This enables us to analyse the data more precisely so that effective improvement measures can be deduced." All key parameters are taken into account and monitored via a digital interface. For example, it is possible to use information relating to the current throughput of the Erema Pre Conditioning Unit to optimise the washing process as soon as possible so that it can compensate for fluctuations in capacity and achieve a significant increase in output. This data transfer represents a new step on the roadmap to digitalization.
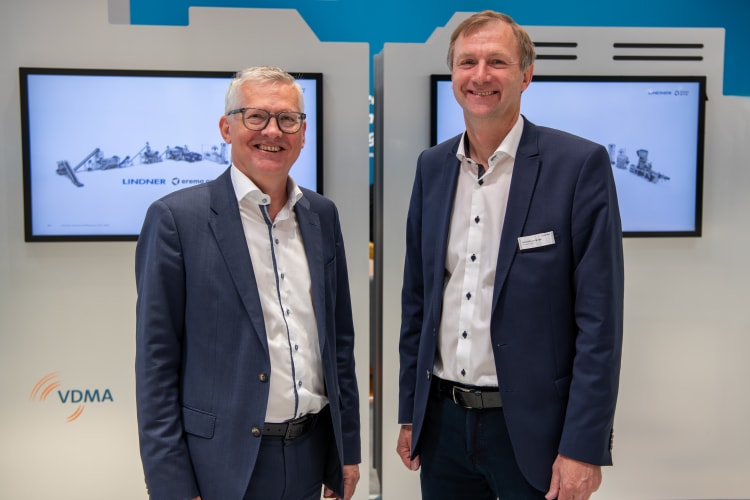
High efficiency due to smart energy management
"To ensure sustainable recycling, it is necessary to find the right process for each application and to make sure that the individual process steps are perfectly coordinated," emphasizes Michael Lackner, Managing Director of Lindner. Coordinating the process steps has already achieved initial success in energy management, and a clear example of this is heat recovery. "We use the latent heat generated during the extrusion process as an energy source for the washing and drying process," explains Lackner. "This enables our customers to sustainably reduce their energy costs and carbon emissions".
Making the most of synergies along the value chain
Synergies need to be used to establish the quality standards specified for each end application. "The key question is how we can improve the end product and increase the overall efficiency of the recycling process at the same time," agree Manfred Hackl and Michael Lackner. This will only work if companies work together along the value chain. The industry leaders can already point to several examples where together they have improved recycling processes and made it possible to move away from downcycling. "An example of this is the recycling loop of HDPE starting material, which is processed into high-quality, food-safe rHDPE pellets using our two technologies," says Lackner. Lindner Washtech and Erema continue to work intensively together to develop strategies for upcycling plastics and increase recycling rates.
Everything considered, the joint venture offers companies from the waste and recycling industry an additional special service and improves the end-to-end process. "We want to encourage our customers to come to us with their feed material so that we can discuss the options that are open to them. With the combined expertise of Lindner Washtech and Erema, we can find the optimum solution for every scenario," says Hackl.