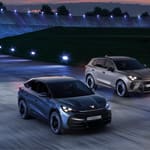
European automotive design is catching up to its American and Chinese counterparts when it comes to a trend: illuminated emblems on the front and rear of vehicles. Recent changes to European vehicle lighting regulations have expanded opportunities for brand showcasing, creating an exciting new application for Plexiglas molding compounds in automotive manufacturing. After all, producing illuminated logos and lettering requires high-quality, light-diffusing materials.
A trailblazer with an illuminated emblem
A pioneer of this trend, Cupra is launching one of Europe’s first series models featuring an illuminated front emblem with its new Tavascan model in fall 2024. The Spanish automotive manufacturer aims to set an eye-catching example for its electric future with innovative lighting design. The Cupra Tavascan is the first fully electric SUV coupé from the young Barcelona-based brand, which emerged from Seat’s sports division.
On most models, the Cupra logo is found on the hood. With the Tavascan, the design team placed the copper-colored emblem on a glossy black background, outlining it with a slim contour of light-diffusing Plexiglas Softlight. By day, the outline takes on a soft white appearance. At night, with the vehicle lights turned on, it transforms to outline the brand’s distinctive emblem with a luminous glow. This effect is achieved by backlighting the sleek, injection-molded emblem with LEDs.
The triangular shape of the illuminated emblem complements the triangular signature light design of the headlights, which are linked by three horizontal light strips. This striking front-end design of the Cupra Tavascan impressed the judges of the 2024 Red Dot Design Award, who named it the winner in the product design category: “This electric coupé impresses with its dynamic, emotional design and the memorability of its distinctive vehicle face.”
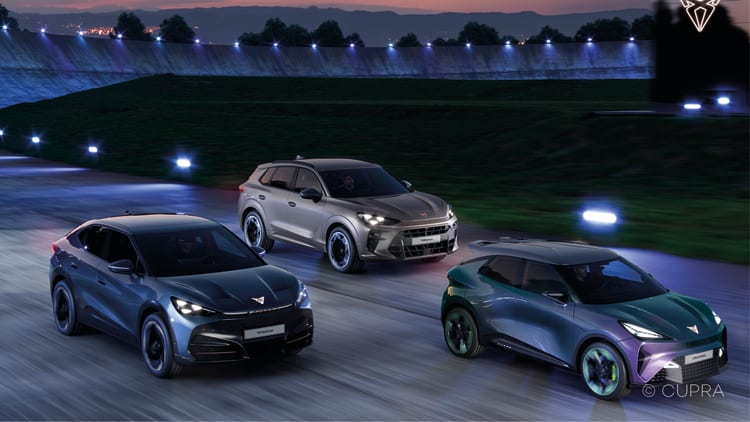
Plexiglas Softlight: Specialty for light guides
Röhm offers the ideal material for this kind of unusual signature front lights and illuminated emblems: Plexiglas Softlight with additional impact resistance features. As Francisco Félix Vicent, Project Manager in Seat’s Lighting Department, stresses: “Any plastic components used in vehicle front-end assemblies must be extremely tough and breakproof. This special Plexiglas product provides us with the ideal combination of properties for this. It has the necessary impact strength coupled with the light diffusion we need.”
Ramon Vilardell, Senior Business Manager in Röhm’s Molding Compounds business unit, describes the special features of Plexiglas Softlight: “The product family offers a wide range of polymethyl methacrylate molding compounds with light-guiding and homogeneous light diffusion properties. They are ideal for backlit components. If required, we can also provide Plexiglas Softlight with addionally increased impact resistance.”
“This robust type of Plexiglas is a next-generation material that opens up many new applications in vehicle front-end design,” concludes automotive engineer and Seat lighting specialist Vicent.
Plexiglas Softlight can be processed easily and precisely in all common injection molding processes. Moreover, the exceptional UV and weather resistance of all Plexiglas molding compounds eliminates the need for automotive manufacturers to apply an additional UV coating.