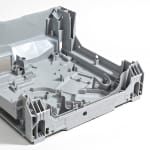
Detergent bottles are frequently manufactured using recycled plastic; however, as far as higher value-added applications are concerned, these recyclates have yet to be deployed on a large scale. Researchers at the Fraunhofer Institute for Structural Durability and System Reliability LBF, working together with partner companies, have demonstrated that recycled plastic performs similarly to virgin plastic - not only that, it is also a suitable material for dishwasher case bottoms.
Recycling plastic plays a key role in climate and environmental protection. While a portion of packaging is often manufactured from recycled plastic, experts and companies are still reluctant to do the same with higher-end products. Ultimately, batch variations of what used to be waste means properties such as strength, odor and appearance, differ from the properties of newly made plastic. However, if the recyclate is processed efficiently, its properties can be adapted to match those of virgin plastic. "There is still a lack of trust in recycled materials," asserts Dominik Spancken, Scientist at Fraunhofer LBF in Darmstadt.
Fraunhofer researchers want to change the status quo and show that recycled materials can be trusted. "We therefore worked together with Bosch GmbH and Bosch-Siemens-Hausgeräte GmbH (BSH) to investigate what recycled plastic can actually achieve," says Spancken. To that end, Bosch firstly optimized recyclate from the housing of automotive starter batteries - additives were used, for example, to increase the strength and enhance the visual properties. Next, we had to identify whether the optimized material would be suitable for manufacturing dishwasher case bottoms. This component, weighing approximately two kilograms, forms the base structure of a dishwasher, holding the side walls and housing ancillary components such as the pump, status sensors and salt reservoir. If these case bottoms could be produced from recyclate, this would be a significant contribution to making household appliances more sustainable: Based on a production figure of three million dishwashers per year, using the recyclate (and thus fewer resources) would save around 2500 tons of crude oil annually – equivalent to the amount of oil transported on a 110-meter-long barge.
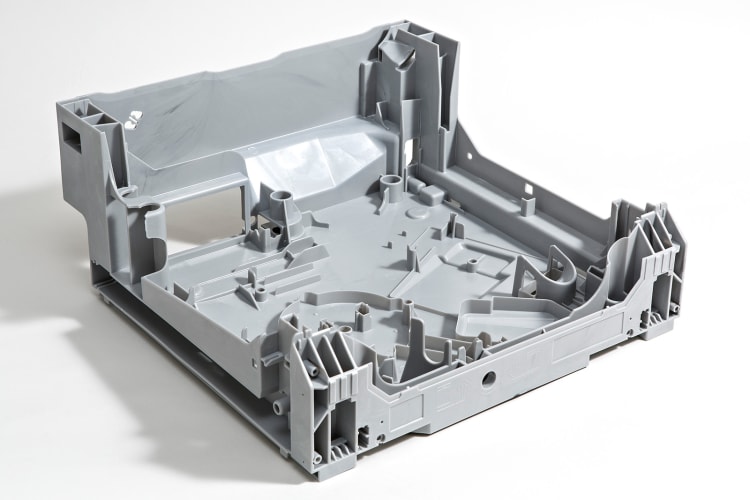
What can the recycled material achieve?
"At Fraunhofer LBF, we initially investigated how the optimized recyclate behaved under mechanical stresses," explains Spancken. The researchers therefore produced a test specimen and subjected it to a set force around 100,000 times - in an automated process, of course. This number reflects the typical use and load range for large white goods. This sets the limit for how much stress the material must be able to withstand without becoming damaged. In accordance with these specifications, the experts at Fraunhofer LBF, Bosch and BSH established parameters for the design.
As regards the 100,000 cycles, this figure is primarily based on a finger-thick pin on the dishwasher case bottom. This is subject to mechanical stress every time the dishwasher door is opened and closed, and represents the area subject to the greatest load on the dishwasher case bottom. If we assume that the dishwasher door is opened 15 times a day and that the appliance has a lifespan of around 18 years, the door will be opened around 100,000 times throughout the dishwasher’s entire service life. Can a pin made from recyclate withstand this? "While the recyclate is less strong - 15 percent weaker - it has similar stiffness properties to that of virgin plastic. More importantly, however, both materials behave exactly the same way in terms of plastic deformability. In summary, it is fair to say that the recyclate can handle the same stresses as virgin material," confirms Spancken.
How robust is the component made from recyclate?
To confirm this result, the researchers also conducted tests on the component itself, in addition to the pure material testing. "We calculated material characteristics from the material tests. Using these characteristic values, we then developed an assessment methodology to check whether the pin is durable," explains the scientist. In other words: The research team clamped the pins from case bottoms made from virgin material in a test bench and applied loads to simulate those resulting from use of the dishwasher, specifically when the machine door is opened and closed. Given that underfloor heating and radiant heat from the dishwasher could heat the pin to up to 50 degrees, Spancken and the team adjusted its temperature to 50 degrees to reflect this. How much force was required to break the pin? How often could it withstand the opening process? Using the experimental data, the researchers created a validated calculation and design methodology - and then "fed" this methodology with the recyclate’s material characteristics. "We were able to extrapolate the behavior of a pin made from recyclate using the tests on the virgin material and the calculation methodology," says Spancken. The result is encouraging: The resilience values recorded for the pins made from recyclate differ only very slightly to those made from virgin material. It can be concluded from the feasibility study that a dishwasher case bottom made from recyclate is indeed possible and swapping from virgin plastic to recyclate would make a significant contribution to a sustainable complete appliance.