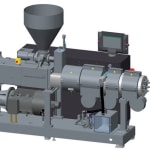
The new single screw extruder solEX NG 75 for the production of PO pipe will definitely be a highlight at the booth. Based on the solEX series, which is already established in the market, the NG series offers a completely redesigned barrel-screw combination. With this, battenfeld-cincinnati sets new benchmarks in the market in terms of output and energy consumption. The advantages of the "Next Generation" are lower melt temperatures, optimized, constant pressure build-up and reduced maintenance costs with significantly higher outputs compared to the previous models. Thanks to the lower drive energy and reduced energy losses, energy costs can be decreased by up to 15%. "With the design of the new NG series we again prove our innovativeness. We have succeeded in developing an extremely powerful and energy-efficient processing unit that has not yet been seen on the market in this form," emphasizes Grant Flaharty, battenfeld-cincinnati's Chief Sales and Marketing Officer.
In combination with the new PO extruder, the machinery manufacturer will show another innovation: the Fast Dimension Change (FDC) system. At the booth, three components will be shown - the pipe head, the calibration sleeve and the vacuum tank.
With the FDC pipe head, die changes are largely unnecessary, thanks to an adjustable melt gap. Therefore, it can be used universally for a wide pipe diameter range. For the first time, an adapter for the outer layer has been integrated in the adjustable die, offering the shortest purging times currently available, for example during a color change. Instead of a rigid calibration cylinder, the FDC calibration sleeve consists of movable elements that can be adjusted to almost every diameter, but do not leave any markings on the final product. Finally, the 1.5 m long FDC vacuum tank has scissors lift tables that allow the adjustment to every height with servomotors. A unique flexible and, above all, easily adjustable sealing technology ensures a secure sealing of the vacuum tank.
Multi-Touch roll stack reaps success worldwide
"We have proven in the past years that we are optimally prepared for the growth market packaging sheet with our high-speed ex-truders and the Multi-Touch roll stack which is unique in the indus-try. Customers all over the world have decided in favor of this technology and we have installed numerous systems worldwide," Dr. Henning Stieglitz, Chief Technology Officer, is pleased to report about the market success of thermoforming sheet extrusion equipment. This is why the machinery manufacturer will show a Multi-Touch roll stack at its booth - this time in a XXL-version. Multi-Touch roll stacks work with a combination of a roll stack with two rolls for pre-calibration and three, five or seven rolls in post-calibration. So they produce stress-free sheet with thickness tolerances of +/- 1% at high speeds. The newly developed XXL roll stack shows exceptionally high performance. Outputs of more than 3 t/h can be realized depending on the width and thickness of the sheet while at the same time there are no compromises in sheet quality.Of course, a complete extrusion line also requires a matching con-trol technology. Here, too, flexibility is key. A new control with a modern 21.5" full-HD multitouch display in landscape format will be presented at the booth. Not only does it offer a novel operating and visualization concept, but also additional features that are a perfect tool for processors in the realization of industry 4.0 agendas.
Flexibility is paramount for twin screw extruders
The machine portfolio at the booth is completed by several twin screw extruder exhibits for pipe and profile production. The high-light are two models from the completely newly developed conical twin screw extruder series that offers an exceptionally wide application range thanks to a newly designed processing unit. Apart from the processing technology, the complete machine was redesigned and optimized based on experiences in the field. "With this series we take into account, among other considerations, the increasing requirements of window profile producers. The machines offer a wide throughput range, as well as the possibility of processing diverse formulations," emphasizes Dr. Stieglitz in speaking of the new series' advantages. In addition to their flexibility, the extruders convince with gentle melt processing and easy handling.At K 2016, two extruders from the new series will be shown: a conEX NG 65 in stand-alone execution and a conEX NG 54 in a coextrusion setup. The latter is mounted on a pedestal and combined with a twinEX 93EP as main extruder. This new pedestal solution is suitable for a variety of setup options and can be adjusted individually to the location's requirements thanks to its modular system. The setup on display offers processors highest flexibility and an optimal price-performance ratio. In addition, the conEX NG 54 will feature an energy-saving kit. This includes a synchronous motor and a variety of additional features that significantly reduce the extruder's energy consumption.
Grant Flaharty feels certain: "With the different exhibits from our wide product portfolio for the extrusion industry, we are presenting modern, energy-efficient solutions that will meet the future requirements of the industry as well."
At K 2016 the company will be exhibiting in hall 16, B19.