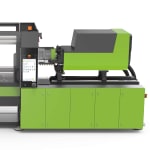
Technology competence, digitalisation, sustainability – these are the three success factors with which ENGEL solves the toughest challenges in injection moulding. The Austrian injection moulding machine manufacturer and system solution provider with its own production facility in Shanghai is bringing four applications to Chinaplas 2022 from 25 to 28 April.
Featuring two exciting applications on e-mac injection moulding machines, ENGEL is demonstrating the amazing sustainability and precision potential of its all-electric drive technology during the four days of the trade fair. "The demand for all-electric machines is growing, also for applications where hydraulic or hybrid machines have been used previously", as Gero Willmeroth, President East Asia and Oceania at ENGEL reports. "There are three main arguments in favour of electric drive technology: precision, total cost of ownership over the entire machine service life including maintenance and energy consumption, and sustainability, that is, the smallest possible CO2 footprint."
All-electric for great overall efficiency
Ecology and economy need to go hand in hand; this is clarified by the two applications in Shanghai. Barrels for 1-ml syringes made of polypropylene in a 32-cavity mould by Liankai are being produced on an e-mac 465/180. Another e-mac 465/180 is demonstrating an LSR application, by manufacturing seals in a 128-cavity mould. The partner for mould-making and the LSR metering technology in this application is Nexus.
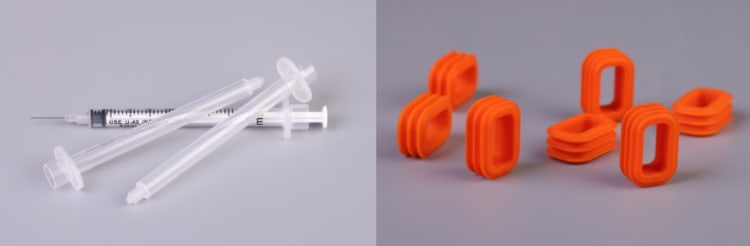
Among the all-electric injection moulding machines on the market, the new generation e-mac machines are some of the most compact worldwide. For example, the 180-tonne machines on show in Shanghai are 450 mm shorter than the previous 180-tonne version, without reducing the opening stroke, thanks to their optimised toggle lever geometry. The result is a boost in productivity per unit of area, which is an important gage of efficiency in many operations.
All movements of the ENGEL e-mac – including the nozzle movement and ejection – are performed by servo-electric drives. This means that the machine achieves very high overall efficiency. If required, a servo-hydraulic unit can be integrated into the machine frame without requiring additional space.
The ENGEL e-mac injection moulding machines combine precision with efficiency and are the most cost effective solution for many applications in the field of all-electric injection moulding machines and applications with cycle times of more than four seconds. They are deployed in a wide range of applications, from medical technologies, through technical moulding, to packaging and to teletronics.
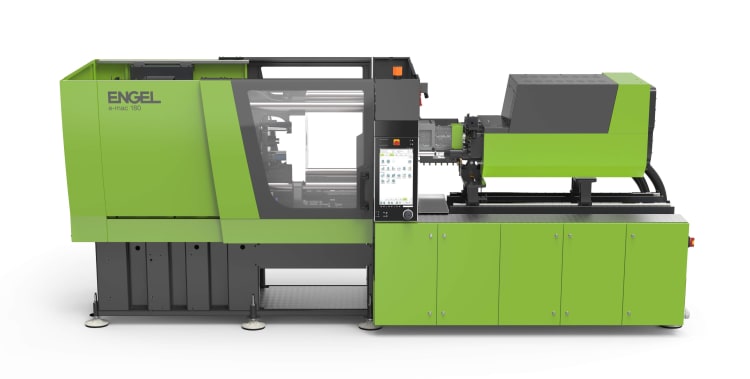
Smart assistance for high process consistency
Whether for headlamps, front panels with integrated sensors or displays, whether in the vehicle interior or on the exterior, applications with transparent materials, for which the most exacting optical requirements apply, are increasing. With a wide spectrum of technologies and a wealth of experience with the optimelt and glazemelt technologies, ENGEL develops production solutions which are a perfect fit for all types of transparent parts. At the trade fair, ENGEL is demonstrating what this can look like in practical terms by manufacturing polycarbonate outer lenses for vehicle headlamps on an ENGEL duo 5160/800 injection moulding machine with an integrated ENGEL easix articulated robot.
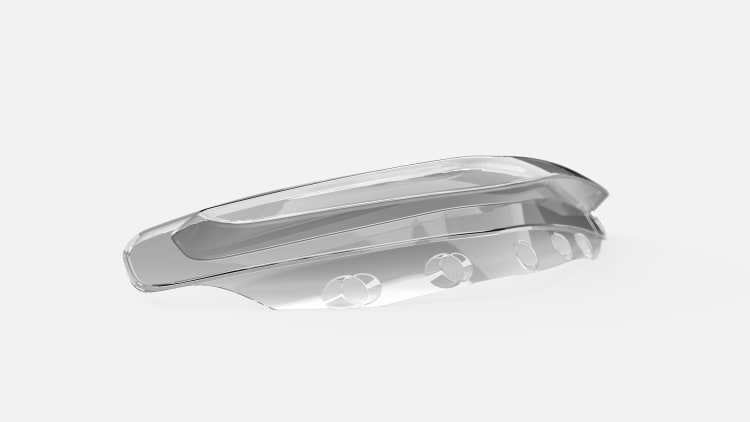
With a wall thickness of 1.8 mm and a length of more than 800 mm, the part poses strict requirements in terms of reproduction of surface detail. Smart assistance systems from the ENGEL inject 4.0 program supplement the great precision of the duo machine's movements. While iQ weight control keeps the injected melt volume consistent from shot to shot, iQ clamp control determines the optimum clamping force for the mould in order to avoid burn marks and flash.
The integrated easix robot offers great flexibility for the integration of downstream process units, such as quality control or assembly systems. The fact that the ENGEL robot's control unit is fully integrated in the CC300 control unit of the injection moulding machine makes using articulated robots particularly easy. The complete production cell offers a uniform control logic. The robot and machine access the same database and can precisely coordinate their motion sequences. This reduces the handling time in many applications.
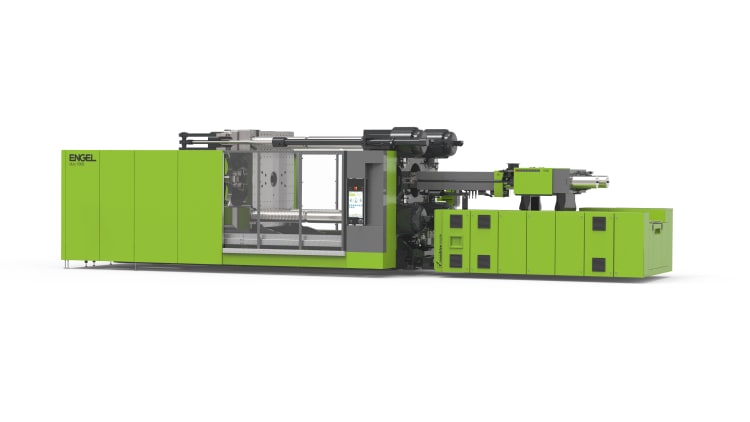