New process technology for high optical purity
LEDs are becoming more and more versatile in their use in vehicles, increasingly being added as distinctive design elements. The level of variation in their shape is growing accordingly, creating new challenges for optical fibre manufacturers. ENGEL has developed a new plasticising process specifically for PMMA processing to ensure high luminous efficiency, also for use cases involving complex geometries and long structures. The principle of starve-feeding is decisive from a technological standpoint. It allows the plasticising screw to be only partially filled with pellets in the intake zone, which in turn reduces the shear load of the melt. In this way, the melt homogeneity and purity can be improved.
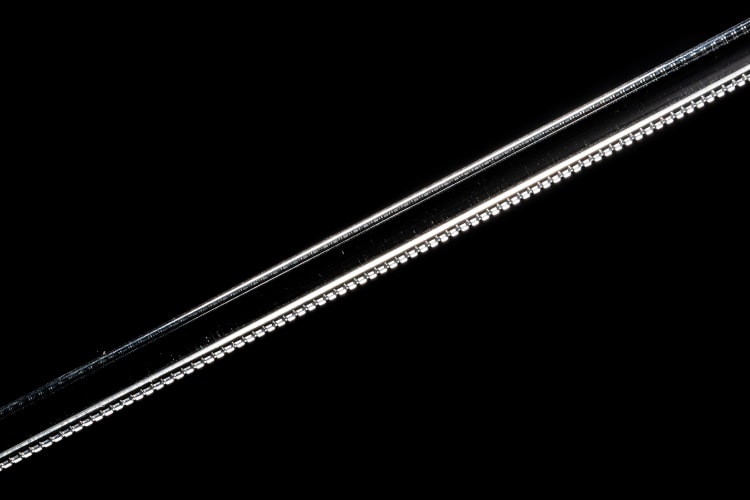
ENGEL is demonstrating the huge potential of the new processing technology by produced light guides of different lengths and curvatures in a family mould by Oerlikon hrsflow on an ENGEL victory 320/120 injection moulding machine with an integrated ENGEL viper 20 linear robot. The ENGEL victory machine with its tie-bar-less clamping unit ensures high overall efficiency here. Thanks to tie-bar-less technology, the large family mould fits on a relatively small injection moulding machine. The robot can reach the cavities directly from the side without needing to working around interfering edges, which keeps the handling time short.
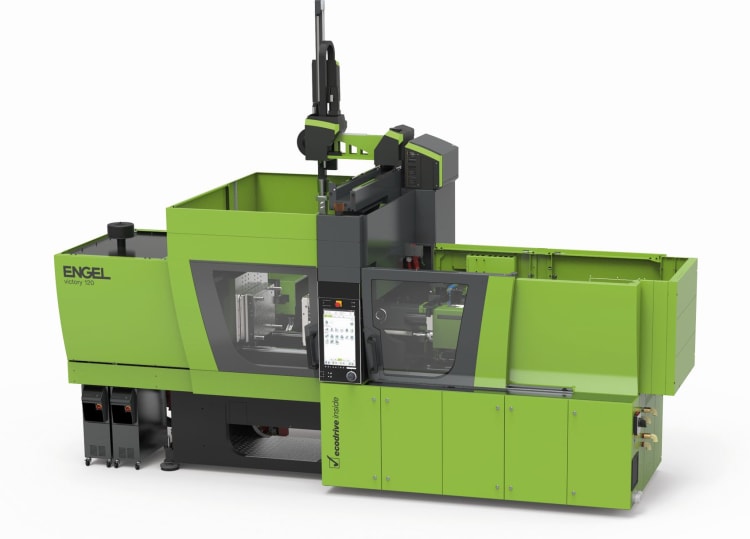
Online support for a high degree of machine availability
All four production cells at the stand are equipped with e-connect.24, ENGEL's online support and remote maintenance tool, and connected to the same network. All of the production cells can be monitored and controlled via a central monitor at the stand. In daily production, the tool is used to enable ENGEL service staff to connect to the injection moulding machine from an external location to be able to respond without losing time in support cases, for example. The screen pages of the machine control unit are mirrored via the internet on a computer that can be several thousand kilometres away. The current state of the machine is reflected at all times. As a result, the machine operators on the ground and external support staff can see the same settings and production data and can consult and guide each other. The manufacturing cell can even be controlled remotely when necessary.
Thanks to this range of options, e-connect.24 ensures very high machine availability and delivery capability, also in times of crisis such as those experienced during the Covid-19 pandemic. "In the past two years, in which options for on-site service calls have been limited, many customers have made intensive use of e-connect.24", says Willmeroth. "Not only in service cases, but also in the scope of on-going projects. Virtual collaboration with e-connect.24 has enabled us, for example, to successfully conclude process optimisation projects started before the pandemic broke out without any loss of time."
Live on site and virtual at the same time
Personal contacts always have been and always will be important – as was confirmed by the first face-to-face events after two whole years of the Corona pandemic. Even though the pandemic has shown in the past few months that digital formats work very well, and even offer advantages in certain areas. The future is hybrid – ENGEL is convinced of this and has established a virtual showroom for this reason. More than 20 machine exhibits with many challenging applications are waiting to be explored in the virtual showroom. At Chinaplas, ENGEL is building a bridge between the physical and virtual trade fair world. Trade visitors can use large touchscreens to access the virtual exhibits. "This means that, in Shanghai, we are exhibiting the widest range of applications, machines and system solutions that we have ever shown at Chinaplas," says Gero Willmeroth.
ENGEL at Chinaplas 2022: Hall 5.1, stand B48