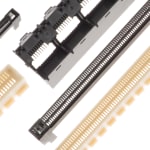
BASF’s engineering plastics of the Ultramid family have a long and very successful history in metal replacement. The BASF polyamides (PA) have allowed lightweight and high-performance parts to be used in many different applications, from the automotive and the E&E industries to mechanical engineering and consumer goods. In recent years, the challenges for plastic parts in these fields have increased drastically by trends such as further miniaturization of parts and systems, e-mobility and accelerated electronics, increased contact with chemicals and sophisticated flame-retardant systems - all leading to higher functional integration. These trends call for new plastic materials which can succeed under demanding application conditions and enable customers to develop new parts for future applications. As this fundamental market challenge cannot be solved by a single material, BASF has launched several new polyphthalamides (PPA) during the last four years. It is now in the unique position to offer customers a state-of-the art portfolio based on four PPA polymers comprising a product range of about 50 compounded grades. The PPA portfolio includes Ultramid Advanced N (PA9T), Ultramid Advanced T1000 (PA6T/6I), Ultramid Advanced T2000 (PA6T/66) – completed by the long-standing Ultramid T KR, a PA6T/6, which BASF has been selling since the 1990s. The PPA portfolio is globally available and supplemented by BASF's exceptional simulation tool Ultrasim and its profound application experience. This makes it possible for customers to choose the right material for the right part with a matching, tailor-made application profile.
"During our intensive PPA development work with customers across a lot of industries, we have experienced that they not only need a suitable material but a development partner who can make innovation feasible and faster, offers global reach and ensures high-quality products and services for more and more complex application requirements", says Abdullah Shaikh, head of the global PPA team. "With our PPA portfolio, we build on our deep knowledge of polyamides and applications to empower our customers to make innovation possible and access new trends. We are dedicated to continuously develop this portfolio with further customized compounds to extend and improve the products’ fit and performance."
The tailor-made Ultramid Advanced portfolio includes grades for injection molding and extrusion for easy and stable processing, grades with or without flame- retardants, from uncolored to laser-markable black, with short-glass, long-glass and carbon fiber reinforcement as well as with different heat stabilizers. Due to their partially aromatic chemical structure all Ultramid Advanced types offer good to excellent mechanics at elevated temperatures. Their hydrophobic nature allows them to withstand humidity and contact with challenging media and at the same time to maintain their strength. The low water uptake results in a high dimensional stability of the plastic parts in humid environments. They keep their strength also in lead-free soldering processes more and more often used in the electrical and electronics (E&E) industry.
Ultramid Advanced N – the superhero for engineers
As a PA9T, Ultramid Advanced N shows constant mechanics up to 100°C (glass transition temperature: 125°C), outstanding chemical resistance and low water absorption as well as very good tribological properties. Ultramid Advanced N can be employed in a wide processing window and enables short cycle times. It allows customers to design lighter, smaller and stronger plastic components. The material can solve problems in a wide range of applications: Ultramid Advanced N is suitable for small connectors and function-integrating housings in white goods, consumer electronics and mobile devices. It can be used in automotive components and structural parts near the engine and the gearbox. Applications like gear wheels and other wear parts can be implemented, too. There are now about 20 grades that customers can choose from to develop technically sophisticated parts for challenging environments where other materials reach their limits.
Ultramid Advanced T1000 – one T for 1000 tasks
Within the Ultramid family, Ultramid Advanced T1000 (PA6T/6I) is the product group with the highest strength and stiffness and with stable mechanical properties at temperatures of up to 125°C (dry) and 80°C (conditioned). It offers high resistance to humidity and to aggressive media – outperforming conventional polyamides and many other PPA materials on the market. Applications can be found in the automotive industry, especially in areas where materials have to remain strong, no matter what temperatures or climates they are exposed to, and in all other industries where resistance to humidity or chemicals is required: e.g. in thermostat housings and water pumps, in fuel circuits and selective catalytic reduction systems, for actuators and clutch parts in cars as well as in coffee machines, as furniture fittings, and in construction applications such as water distributors, heating systems and pumps. BASF offers about 10 grades to the market, from heat-stabilized, glass fiber-reinforced standard grades for different stiffness, strength and toughness values via special grades with improved hydrolysis resistance to a long-glass fiber reinforced, highly heat-stabilized compound.
Ultramid Advanced T2000 – connecting dielectric with mechanical strength
Ultramid Advanced T2000 is the latest PPA compound portfolio launched at Chinaplas 2019. Based on PA 6T/66 it combines excellent mechanical with dielectric strength at high temperatures - a combination which is particularly needed for connectors in the E&E industry. Ultramid Advanced T2000 is the ideal solution for parts that require high, constant stiffness and strength over a broad temperature range in combination with resistance to heat and humidity as well as optional flame- retardant (FR) properties. The PPA shows improved impact strength on par with standard PA66 and a lower water uptake than standard aliphatic polyamides resulting in high dimensional stability. Its high melting point (310°C) and heat deflection temperatures of >280°C (HDT-A) make it the ideal material for lead-free soldering without part deformation. Thus, delicate flame-retardant connectors, structural laptop parts as well as switches and miniature circuit breakers can be manufactured. Ultramid Advanced T2000 with about 10 grades is also a versatile candidate for metal replacement of automotive parts such as water outlet valves, water pumps, fuel system components as well as actuators, transmission sensors and clutch parts.
Ultramid T KR – one of the first PPAs on the market
Originally introduced at K fair 1989, Ultramid T KR was amongst the first PPAs on the market. In the last decades, the portfolio has been further developed and extended to now 15 grades, thereof glass-filled and flame-retardant grades, as well as an unreinforced and a food-contact grade. The PA6T/6 has a high melting point of 295°C and can still easily be processed. It provides high stiffness and strength, especially in the presence of humidity, and is at the same time the PPA material with the highest toughness. It possesses excellent heat resistance: The relative tracking index (RTI) of 160°C at 0.4 mm of Ultramid T KR4340 G6 is one of the highest RTIs in the whole polyamide market. It can also offer excellent flame- retardance, e.g. with UL94 V-0. Thus, Ultramid T KR is ideally suited for E&E applications like quick connectors, switchgears or relays, as well as for electrical control units or vehicle sensors.
Precise part design with Ultrasim for PPAs and in-depth application know- how
BASF’s simulation tool Ultrasim is used in the design of parts for all industries. With customized models, BASF has further developed the calculation tool in such a way that parts made of Ultramid Advanced grades can also be simulated. Using Ultrasim®, the physical behavior of the part can be predicted on the basis of manufacturing parameters, fiber anisotropy and load direction or speed. The mathematical part optimization can furthermore provide the best possible design under the given conditions. Ultrasim® is therefore a unique tool for optimizing customer parts at a very early stage so that they can handle highest loads. With these precise predictions, costs and time associated with prototypes or extensive mold corrections can be avoided.
With its long experience as well as its technical and material expertise of engineering plastics, BASF can contribute to realize challenging applications and provide the most efficient technical solutions for PPA applications across all industries. Emerging trends in the markets result in challenges that need intensive joint discussions and learnings. BASF has the experts to engage with the relevant experts at processors, manufacturers and OEMs and thus to provide extensive information on materials, consultation on new application development and technical service for processing.
Source: BASF