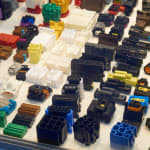
Sumitomo (SHI) Demag Plastics Machinery GmbH has launched a highly competitive, energy efficient all-electric Multi-Component machine. The new IntElectMulti is available to customers globally from September 2019.
Catering to brand leaders seeking innovative and creative ways to integrate multiple colours, resins and sensory features into products, in addition to maximising productivity, the machine’s energy efficiency helps moulders to conserve valuable resources.
With its dynamic motor design, the IntElectrange, now comprising the Multi machine, provides up to a 20% increase in production output, up to 60% reduction in energy consumption and faster machine return-on-investment (ROI) -typically around 18 months.
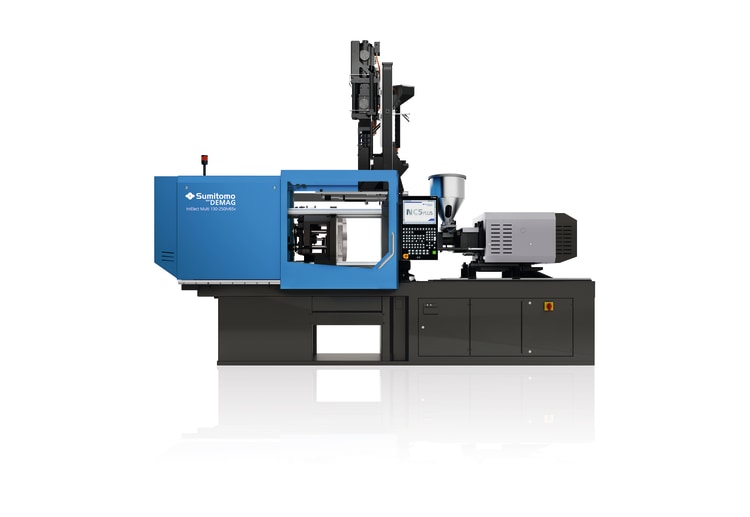
Sumitomo (SHI) Demag launches the energy-efficient IntElectMulti, its most advanced Multi-Component moulding machine to-date
Product manager Peter Gladigau explains: “The IntElect Multi is our most advanced Multi-Component mouldingmachine yet. Featuring direct drives, it delivers the highest level of precision and repeatability for multi-component moulding. This ultimately offers shorter cycle times compared to hydraulic concepts. Additionally, the series fills a vital gap for multi-component moulders seeking greater production flexibility using a more compact and energy efficient machine.”
Sizing up options
Currently available in three machine sizes -100, 130 and 180 ton -injection moulders can now opt for a machine that delivers the level of flexibility and precision required for high volume multi-component manufacturing. Additional machine sizes will follow in time. From small to big shot weights, simultaneous to sequenced multi-component moulding, the all-electric IntElect can handle every type of application effortlessly.
When co-injecting multiple materials, the number of cavities mostly double. In addition, rotating the mould 180° by turntable requires more mould space. The IntElect Multi has been adapted to fit a mould measuring up to 800mm in height and support a turning diameter of up to 825 mm, with a tie bar clearance of 570 mm1. “Compactness isa big consideration for moulders. Most parts produced on a multi-component machine are high volume but relatively small, e.g. automotive and electronic connector housings. Previously, moulders may have opted for a larger machine to accommodate the tool and turntable. By increasing the mould space, Sumitomo (SHI) Demag has addressed this issue,” says Peter.
Enhanced safety
Given the complexity and value of multi-component tools, the IntElectMulti includes an advanced mould safety system as standard. Featuring high resolution sensors built into the toggle system itself, the signals produced are so accurate the machine can detect even the slightest change in force patterns and respond accordingly. The safety system monitors the mould closing sequence, closingforce and mould speed.
Additionally, the machines assist moulders to monitor the ejector force. Through this, the machine can detect parts and mould elements that have jammed, issues that arise with wear in the ejector system, as well as broken ejector rods.
On trend ... Available now
The launchof the highly precise IntElectMulti addresses a rising global movement towards more complex parts that feature two different materials.
Combining materialsisespecially popular in the personal care market. Some of the most common examples include disposable razors andtoothbrushes. “As manufacturers look to boost their market position, they will for different ways enhance the consumer experience,”adds Peter.
The machine also offers a solution for sandwich moulding, which from a circular economy standpoint offers more options to integrate recycled materials for the inner parts of components.
Additionally, moulders can use an inner foam material wrapped in a rigid plastic, resulting in a lighter weight component and savings on materials, or alternatively combine hard and soft materials to improve the aesthetics and comfort of parts. Another option, covering an inner glass fibre material with an unfilled material delivers increased stiffness and creates a brilliant surface. All of these multi-component variations are feasible on the new IntElect Multi.
According to the latest report issued by Transparency Market Research, the market for Multi-Component moulding is anticipated to reach US$ 11.58 billion by 2024. Although popular in the manufacturing of automotive parts, the report predicts that the medical, consumer goods, electrical and electronics segments will experience the biggest growth in the next five years.
Peter agrees with these forecasts, commenting: “For a number of moulded applications today, aesthetics are increasingly important for design differentiation. Additional benefits are also achieved fordurability and functionality.”
Crediting Sumitomo(SHI) Demag’s prowess in all-electric machines -currently the company has installed more than 65,000 all-electric machines globally -Peter emphasises the significance of the optimised motor design. “When working with two materials, perfecting the injection process control is even more critical given that a second material is being injected on top of the first shot.”
Geared towards top dynamics, precision and repeatability, the IntElectdrive technology is equally critical for the smooth and fast rotation of the mould. The machine’s integrated turntable perfects this 180° motion, ensuring components are positioned perfectly to receive the second shot, all within less than one second of the turning time.
The IntElectMulti is now available to customers worldwide. As with the entire IntElect range, additional machine sizes will be added to complete the portfolio.