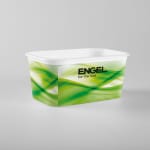
Sustainability and the circular economy are the focus of Engel's stand at ArabPlast 2021 from 15 to 18 November in Dubai, United Arab Emirates. Recycling, energy efficiency and thin-wall technology are the key factors in reducing the CO2 footprint. Engel is presenting the technological answers for this in the form of applications from the fields of logistics and packaging.
"It takes innovative technologies to establish a circular economy," as Andreas Leitner, Sales Director Middle East with Engel, emphasises. The focus here is on new processing methods and digitalisation.
The trend towards more sustainability is becoming particularly evident in the area of logistics. Companies in the Middle East have set themselves the target of completely doing without wooden pallets in the long term. In many cases, plastic pallets are significantly lighter and have a higher load capacity, which reduces CO2 emissions in freight. In addition, they do not contain environmentally harmful pesticides and fungicides, are neither hygroscopic nor flammable and do not splinter. "Today, pallets are already often produced from one hundred percent recycled material," says Leitner, describing a further milestone. Large machines from the Engel duo series, equipped with smart assistance, are being used for this.
With their very powerful plasticising units, compact dual-platen large machines by Engel are optimally equipped for processing very heavy shot weights. The screws are individually adapted to the recycling material to be processed.
Stable processes with recycled material
Both post-consumer and post-industrial materials – usually PP or HDPE – are used in the production of pallets. What they have in common is strong fluctuations in material properties. The iQ weight control smart assistance system ensures that a stable production process and consistently high product quality are maintained despite this. The software, developed by Engel, continually analyses the pressure profile at the screw position during injection and compares the measured values with a reference cycle. On this basis, new process parameters are calculated and process settings are automatically readjusted for the cycle that is already in progress. This calculation and readjustment takes place in fractions of a second, and is repeated for each cycle. In this way rejects are proactively prevented.
In this way, smart assistance makes it possible to use recycled materials even for challenging products and contributes substantially to the establishment of a circular economy for plastics. "We want to replace the downcycling of products that has prevailed to date with recycling or even upcycling," says Leitner. "This is the goal that drives us in development."
Automation from a single source
Engel globally offers complete system solutions for integrated and automated injection moulding processes from a single source. Both Engel easix articulated robots and Engel viper linear robots are used in pallet production. To achieve full linear automation even for larger dimensions, Engel has a viper robot with a nominal payload capacity of up to 120 kg in its portfolio. The Engel viper 120 enables a demoulding stroke of 3,000 mm and reach of 3,550 mm.
In addition to injection moulding machines and robots, Engel develops and produces custom automation solutions and process technologies in-house. Beyond this, Engel integrates solutions from partner companies. In the Packaging business area, Engel is exhibiting at ArabPlast in collaboration with Switzerland-based Beck Automation, a company which specialises in fast demoulding robots and in-mould labelling, and with IMD vista, which specialises in vision inspection and is also headquartered in Switzerland. The three partners can point to many collaborative reference projects in the United Arab Emirates.

The trend is towards sustainable plastic pallets. The iQ weight control smart assistance system ensures consistently high product quality also in applications which use recycled materials.
Thin-wall injection moulding with stack moulds
At the stand, Engel, Beck and IMD have various examples of innovative thin-wall packaging and resource-saving caps and closures on show. Further reduction of the wall thickness toughens the demands on injection moulding machines. Engel has the perfect answer for small to large clamping forces in the form of the e-speed. The injection moulding machine, designed for continuous high performance in thin-wall applications, ensures very fast and, above all, precise short strokes. Thanks to this dynamic, it is also suitable for stack moulds.
The Engel e-speed injection moulding machine with hybrid injection unit and electric clamping unit combines very short cycle times with maximum precision and very high injection speeds of up to 1200 mm per second, and it operates in an extremely energy efficient way. The energy recovery system absorbs the braking energy from the mould mounting platens and returns the stored energy to the motor – for example, to accelerate the platens again.
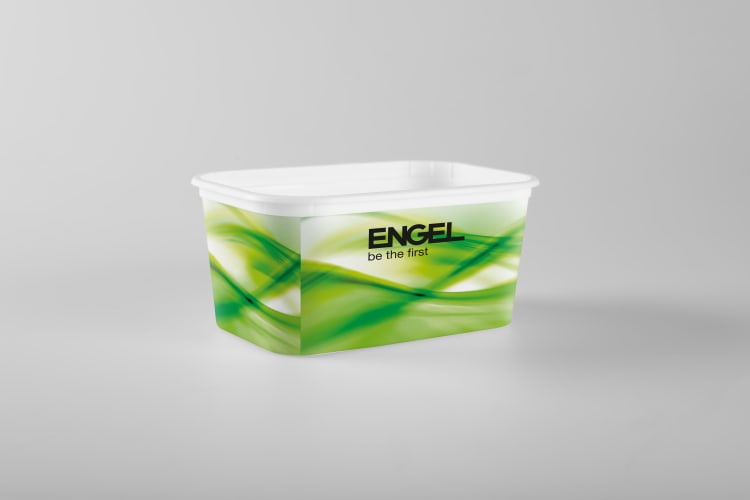
In the production of thin-walled containers, ENGEL e-speed injection moulding machines combine very short cycle times, maximum precision and very high injection speeds with maximum energy efficiency.
The toggle lever is encapsulated to ensure particularly low oil consumption and maximum cleanliness. In this way, the e-speed series machines meet the strict requirements of the food industry as standard.
A deep understanding of local markets and individual customer requirements is a prerequisite for developing tailor-made injection moulding solutions. To ensure close proximity to its customers worldwide, Engel is continuously expanding its sales and service network. Dubai also has its own service base.