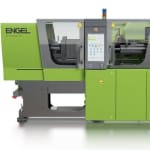
"Quality requirements in China are continuing to rise," as Gero Willmeroth, Sales and Service President at Engel Machinery (Shanghai) says in the run-up to Chinaplas. "The biggest challenge is reconciling increasing quality requirements with maximum efficiency and minimum unit cost." The key to this is tailored machine concepts, process integration and automation. In project business, in particular, it is important to not just be familiar with the requirements of the country markets, but also to understand the individual target industries. With its five business units, Automotive, Teletronics, Technical Moulding, Medical and Packaging, Engel is perfectly geared for this. Industry experts at Engel's headquarters in Schwertberg, Austria, cooperate closely with the subsidiaries, bundling know-how from global projects and defining important research and development focuses with their experience.
Engel e-motion TL – making precision economical
The latest machine innovation, the all-electric and tie-bar-less Engel e-motion TL, was designed specifically for manufacturing small precision parts, and premium optical components in the electronics industry. The objective here is to combine the highest levels of precision and productivity with maximum energy efficiency and an extremely compact machine design. In this market segment, all-electric machines are the standard. To offer highly compact manufacturing cells here, Engel combines all-electric drive technology with a tie-bar-less clamping unit in its Engel e-motion TL small-size machine.Engel will be using an Engel e‑motion 50/30 TL injection moulding machine with 300 kN clamping force at its trade fair stand to produce 60x board-to-board plug-in connectors in a 16-cavity mould. The very tight pin spacing of just 0.5 mm defines the required level of precision in this application. The machine's most important performance characteristics are an injection pressure of 3200 bar, an injection speed of 800 mm/s and acceleration of more than 40 m/s². At the same time, the high cavity count boosts productivity. Moulds with 4 to 8 cavities have generally been used in the production of FFC/FP connectors up to now.