Optimum holding pressure time with just one click
The e-mac machine displayed at the Swiss Plastics Expo will be equipped not only with iQ flow control, but with all assistance systems available as part of Engel’s inject 4.0 programme. These can be activated and deactivated to enable visitors to the trade show to track functionality live, highlighting the major benefits of specific iQ solutions in terms of the day-to-day challenges of injection moulding. Experts from Engel will present various scenarios illustrating such topics as greater energy efficiency and consistent part quality, even where raw materials are subject to batch fluctuations.
Live on show: iQ hold control, the new smart assistant for nominal values that determines the ideal holding pressure time. Until now, holding pressure time has generally been determined empirically, which takes a long time and consumes a lot of raw materials. iQ hold control puts an end to the waste. The assistance system analyses mould breathing and pinpoints the position of the plasticising screw in order to calculate the ideal holding pressure time and pass this on to the set-up technician.
The holding pressure time is determined objectively, meaning that even less experienced process technicians can adjust the process parameters with just one click in case of a batch change. Further efficiency gains can result from the automatically determined optimum holding pressure time being lower than the holding pressure time set initially. In these cases, the cycle time is reduced and the energy requirement decreases.
Another highlight is the iQ process observer, which keeps track of hundreds of parameters in all four phases of the injection moulding process - plasticising, injection, cooling and demoulding. Through continuous analysis and preparation of the data obtained, the iQ process observer enables the fast diagnosis of quality variations. The software incorporates intelligent drift detection, which can be used to indicate process changes proactively, thereby keeping the number of rejects under control.
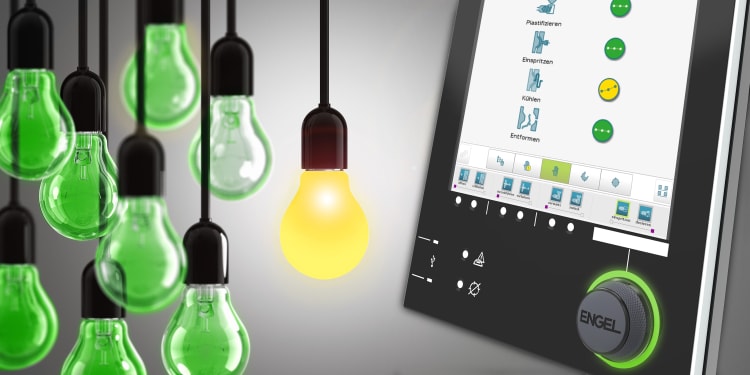
High performance in a compact and cost-effective package
With the e-mac, Engel has complemented its range with an all-electric injection moulding machine that combines high precision, performance and energy efficiency with an extremely compact machine design, all for a relatively low investment cost. The machine is tailored to the needs of the medium performance segment, which is characterised by cycle times in excess of four seconds. The injection moulding machines in the all-electric e-mac series are used in technical moulding applications and the packaging and medical sectors as well as the teletronics industry.
All movements of the Engel e-mac - including the nozzle movement and ejection - are performed by servo-electric drives. This means that the machine achieves very high overall efficiency. The Engel e-mac injection unit was developed from scratch with a focus on even better dynamics. It is available in three performance classes to ensure the machine can adapt to precise requirements while maximising overall efficiency.
Across the whole series, e-mac machines of the latest generation are some of the most compact in the world in their respective performance segments when compared against other all-electric injection moulding machines on the market. Thanks to optimised toggle lever geometry, the machines are shorter than previous versions, without reducing the opening stroke. This guarantees a high productivity per unit of area – an increasingly important indicator of efficiency for many businesses.
Engel at the Swiss Plastics Expo 2023: Hall 1, stand A 1001
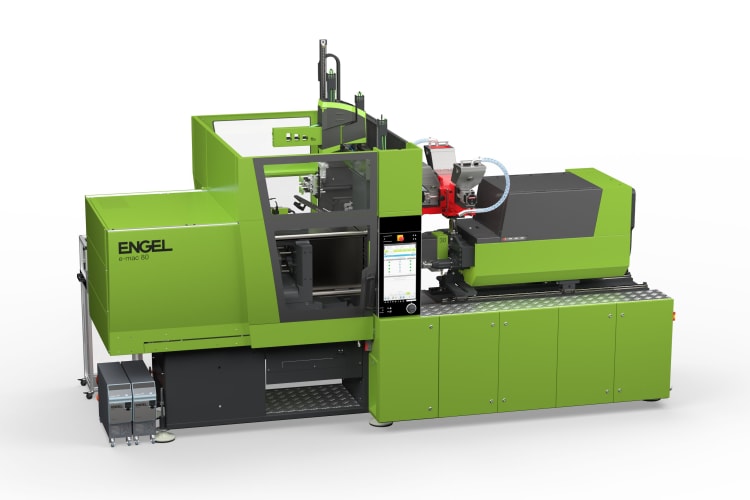