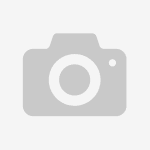
The Engel duo machine with an integrated ZSE MAXX extruder makes it possible to continuously and directly introduce the compounded material into the injection moulding process. The Engel advantage: if required, the injection moulding machine can also be operated independently of the extruder for standard injection moulding processes.
During compounding, different thermoplastics and other materials are prepared with additives using synchronous twin-screw extruders. Depending on the additive, the material receives specific characteristics which determine the properties of the final product. In injection-moulding compounding, this process is integrated directly into the injection moulding process. Here, the extruder transports the plasticized material through heated melt lines into the barrel.
During injection and the post-injection pressure, the mass is put into intermediate storage in a melt pot. Due to this in-line compounding, the product does not have to undergo another round of energetic stress; this results both in an economic advantage - up to 50 percent power reduction - and often in improved mechanical properties of the final product. For example, the length of glass fibres is generally retained. Accordingly, the areas of application are mainly in the automobile industry, but also in the areas of packing (pallets, boxes) and in processing natural fibres.
In co-operation with the Nuremberg-based Leistritz Extrusionstechnik GmbH, ENGEL have now developed a two colour injection-moulding compounder. Integrated in a 1000 t duo machine, the ENGEL injection-moulding compounder offers a number of advantages.
For example, when the machine is used as a "universal machine", it can also carry out the functions of a standard injection-moulding machine. Multi-component applications can be provided very easily due to the construction and high degree of flexibility of the Leistritz ZSE MAXX extruder series with the help of a piggy-back unit.
The sequence - with standard plasticization, a melt buffer (with the ENGEL post-injection pressure technique) and a twin-screw extruder - allows the compounder to process continuously, making it also suitable for difficult compounding jobs. Other advantages: the low height and the simple (decoupled) arrangement with optimal possibilities for automation. As a result, the machine is easier to access for maintenance work; due to the separate side-by-side construction, vibration effects on plasticizing are eliminated.
Particularly today, when increasing prices for raw materials force manufacturers to again and again think about alternatives, the injection-moulding compounder is an ideal solution. The double value added as a result of (plastic) shaping AND material preparation represents a significant advantage. Furthermore, with the help of compounding that is integrated in the injection moulding process, the user can build up his own recipe know-how and can also cheaply create small batches with special compounds.